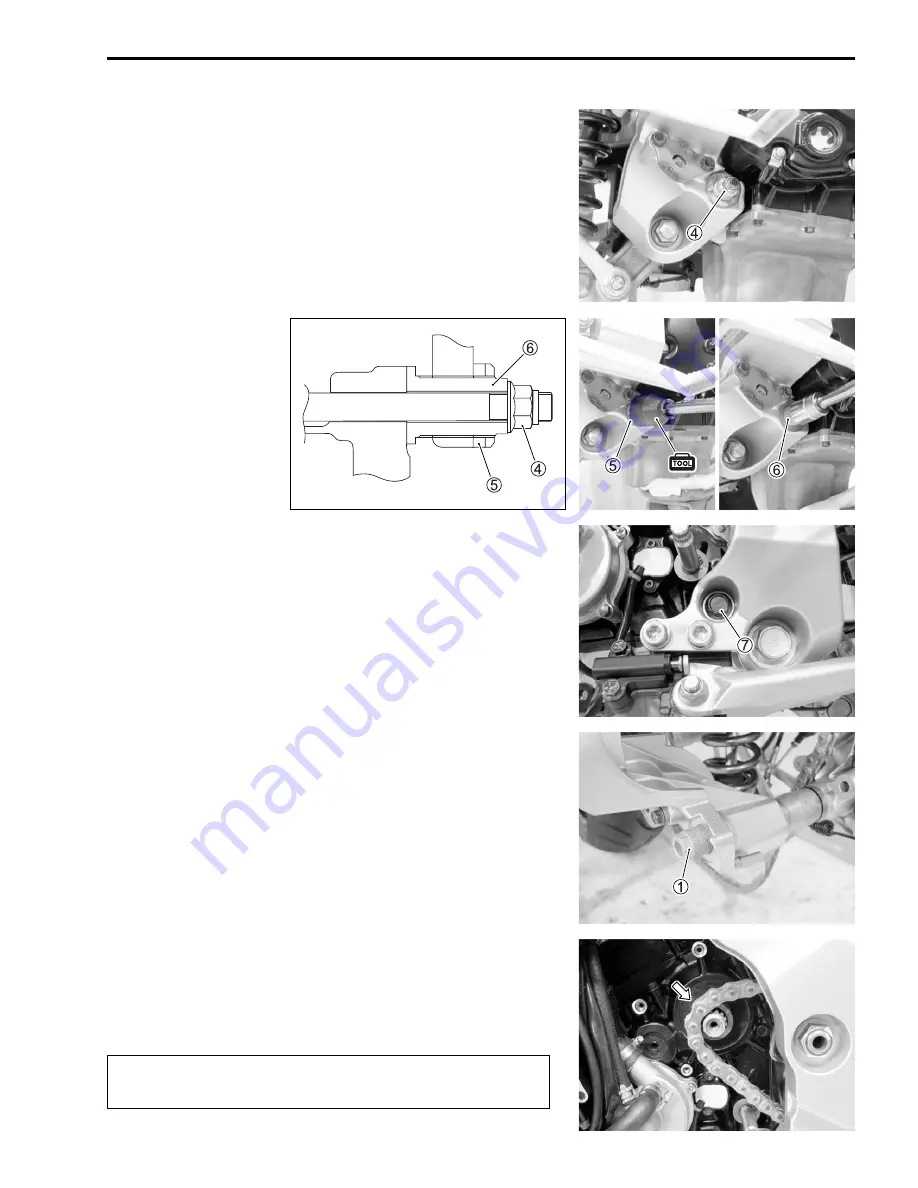
ENGINE 3-9
• Remove the engine mounting nut
4
.
• Loosen the engine mounting thrust adjuster lock-nut
5
with
the special tool.
• Loosen the engine mounting thrust adjuster
6
.
09940-14980: Engine mounting thrust adjuster socket
wrench
NOTE:
Do not remove the engine mounting bolt
7
at this stage.
• Remove the engine mounting bolt
7
. Then, take off the drive
chain from the driveshaft.
• Remove the engine assembly.
ENGINE INSTALLATION
Install the engine in the reverse order of removal.
Pay attention to the following points:
NOTE:
Be careful not to damage the frame and engine when installing
the engine.
• Before installing the engine, install the engine mounting thrust
adjuster
1
.
• Gradually raise the rear side of the engine assembly, and
then put the drive chain on the driveshaft.
• Install all engine mounting bolts and tighten them temporarily.
(
3-11)
Be careful not to catch the wiring harness between the
frame and the engine.
Содержание 2006 GSR600
Страница 1: ...GSR600 9 9 5 0 0 3 6 1 6 0 0 1 E...
Страница 47: ...2 30 PERIODIC MAINTENANCE...
Страница 99: ...ENGINE 3 47 TRANSMISSION PARTS LOCATION 1 Countershaft 2 Driveshaft...