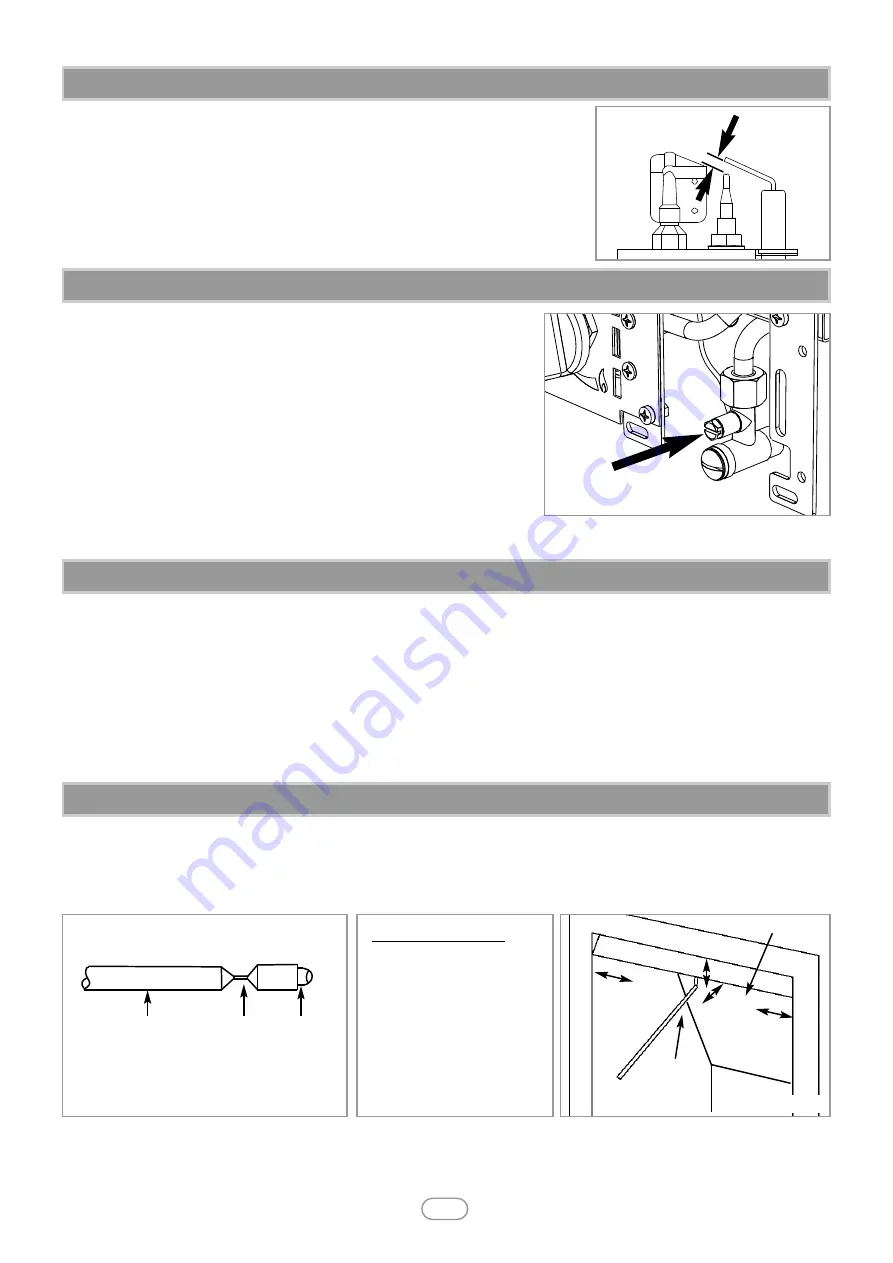
The spark gap (shown in figure 5) between the spark electrode and the thermocouple
should be 3.5 - 4.5mm to produce a good spark.
There should be no need to adjust this.
If under any circumstances the electric spark fails, the pilot may be lit manually by proceed-
ing with the ignition sequence as previously described, and after turning the control knob
through the spark position, the knob should be held in and the pilot lit with a taper.
Release the pressure test point screw, and attach a pressure gauge. Light the
fire on the HIGH setting. To commission the appliance, the operating pressure
must be in accordance with the figures stated in section 2.0 of these instruc-
tions. The fire is factory set to achieve the correct flow rates at the specified
inlet pressure. Any significant variation in the inlet pressure could indicate a
supply problem. If the inlet pressure is too high, the gas supply meter/governor
may be set incorrectly. This should be checked with the fire running and if nec-
essary reset by the gas supplier. If the inlet pressure is too low, then check the
meter/governor pressure with the appliance running. If this is less than the
inlet pressure stated in section 2.0 of these instructions it will need to be reset
by the gas supplier. If the inlet pressure is too low, but the meter/governor
pressure is acceptable, then a problem in the supply pipework is to be sus-
pected. Upon satisfactory checking of the inlet pressure, turn the fire off, dis-
connect the pressure gauge and refit the test point screw. Light the fire and
check for gas soundness. In the event that the inlet pressure is not in accor-
dance with the figures stated in the data section of these instructions, the appliance must not be commissioned, and the problem
investigated and rectified.
This fire is fitted with a flue spillage safety device (ODS). If the fire shuts down during use for no apparent reason then several
things may be suspected. If a door or window has been opened creating a draught, then pilot disturbance is the problem, and
removal of the draught should resolve this. If a grommet seal has been left out of the firebox (if fitted) then this also will also
cause intermittent shutdown. The gas pressure reaching the fire must also be checked. The thermocouple connection into the
back of the gas control valve may also have worked loose during installation, simply tighten to remedy if this is the case.
If pilot disturbance is not the cause, then the ODS safety system may be in operation. Switch the appliance OFF, check the flue
and carry out any remedial work required. Re-light the fire and carry out a spillage test. DO NOT allow the appliance to be used
if it continues to fail a spillage test.
The aeration hole of the pilot must be carefully cleaned out on each annual service to ensure continued function of the ODS.
The spillage monitoring system shall not be adjusted, modified, or put out of operation by the installer. Any spare parts fitted
MUST be of a type supplied for the purpose by the appliance manufacturer.
If the fire is not spilling, then further guidance should be sought, using the Troubleshooting section as a guide.
Close all doors and windows to the room containing the appliance. Let the fire run on HIGH for five minutes. Take a smoke match,
light it, and using a smoke match tube, hold it at the top edge of the fire opening, 25mm down and 25mm in. Starting 50mm in
from either side, run the smoke match across the opening. All the smoke should be drawn away up the flue. Any smoke return-
ing into the room indicates that spillage is occurring. If the initial spillage test fails, run the fire for a further 10 minutes and repeat
the test. When the test has been completed satisfactorily, repeat with any extractor fans in the premises running on the highest
setting, and any communicating doors open. Finally, repeat with all doors open.
NOTE: If spillage is still indicated after undertaking all of the above, there may be a fault in the flue, or insufficient ven-
tilation is present.
If the problem cannot be rectified immediately, then expert advice should be sought. Inform the user, discon-
nect the fire, and attach an explanatory label.
12.0 SPARK GAP
12.1 OPERATING PRESSURE
Figure 5
Spark gap
Figure 6
12.2 FLUE SPILLAGE MONITORING SYSTEM
12.3 TESTING FOR SPILLAGE
Match
Crimp
Tube
Figure 7 : Cross section of smoke match tube
Make a smoke match tube from 10mm diameter
tube. Seal off one end and crimp the tube to pre-
vent the smoke match from sliding down inside.
Spillage test - Figure 8
A.25mm down from top of
opening
B. 25mm in from front of
opening.
C. Disregard outer 50mm
either side of fireplace
opening
C
C
B
A
Fireplace Opening
Smoke Match
In Tube
Figure 9
6
©
2011 Focal Point Fires plc.