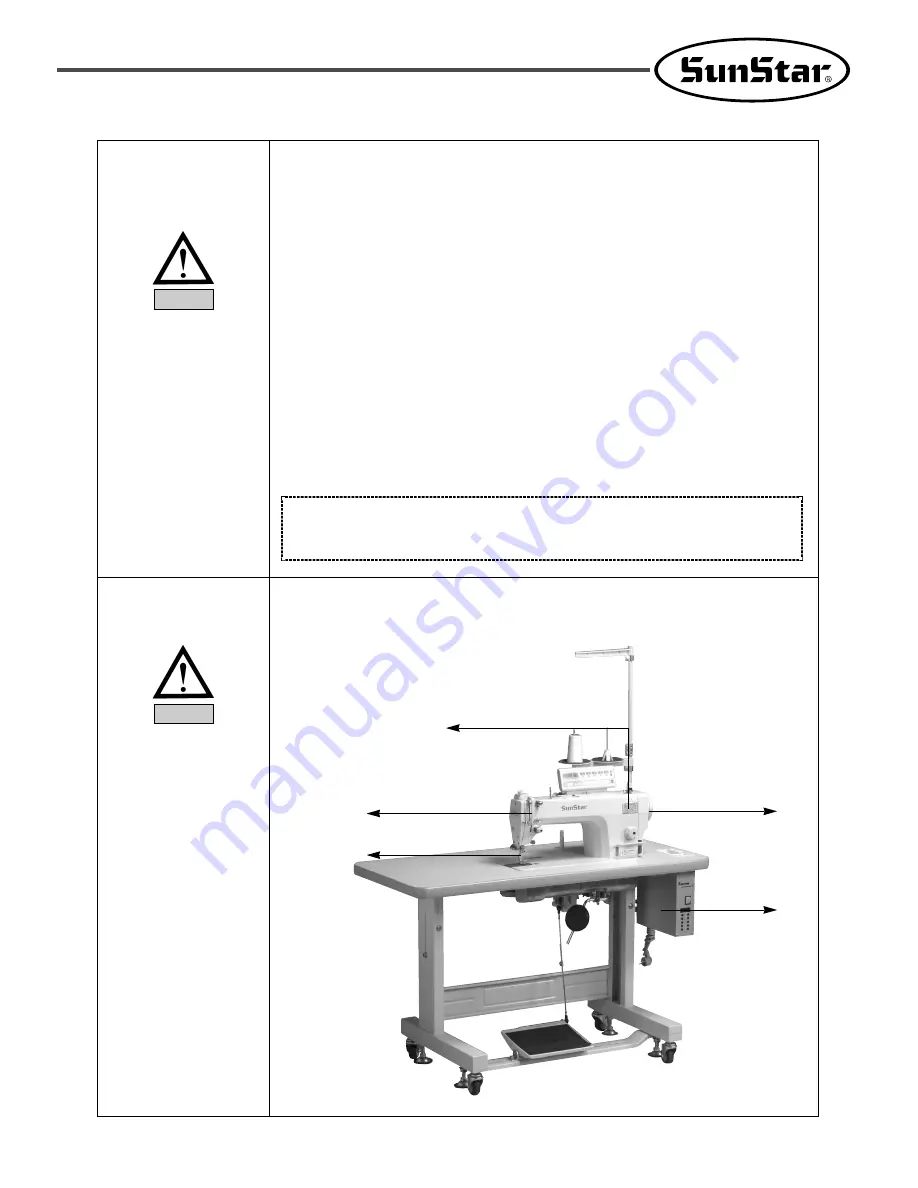
ⓐ
ⓔ
ⓑ
ⓓ
ⓒ
5
KM-2300 Series is made to sew patterns on fabrics and other similar materials for industrial
use.
Follow the following indications when operating the machine.
ⓐ
Read through this manual carefully and completely before operating the
machine.
ⓑ
Wear proper clothes for work.
ⓒ
Keep hands or other parts of the body away from the machine’s operation
parts(needle, shuttle, thread take-up lever, pulley, etc.) when the
machine is operating.
ⓓ
Keep the covers and finger guard on the machine during operation.
ⓔ
Be sure to connect the earthing conductor.
ⓕ
Turn off the main power and check if the switch is turned
“
off
”
before opening electric boxes such as the control box.
ⓖ
Stop the machine before threading the needle or checking after work.
ⓗ
Do not step on the pedal when turning the power on.
ⓘ
If possible, install the machine away from source of strong electrical noise
such as high frequency welding machines
1-4) Operating
machine
Warning
Notice
[ Warning ]
Keep motor cover in place before operating, turn off power before inspecting or adjusting.
1-5) Safety devices
ⓐ
Safety label : It describes cautions during the machine operation.
ⓑ
Thread take-up cover : It prevents any contact between body and take-up lever.
ⓒ
Motor cover : A device to prevent hands, feet and clothing from getting jammed by the
motor.
ⓓ
Label for specification of power : It describes cautions for safety to protect electric shock
during the motors’ rotation. (Voltage input / use Hz)
ⓔ
Finger guard : It prevent contacts between finger and needle.
Содержание KM-2300
Страница 2: ......