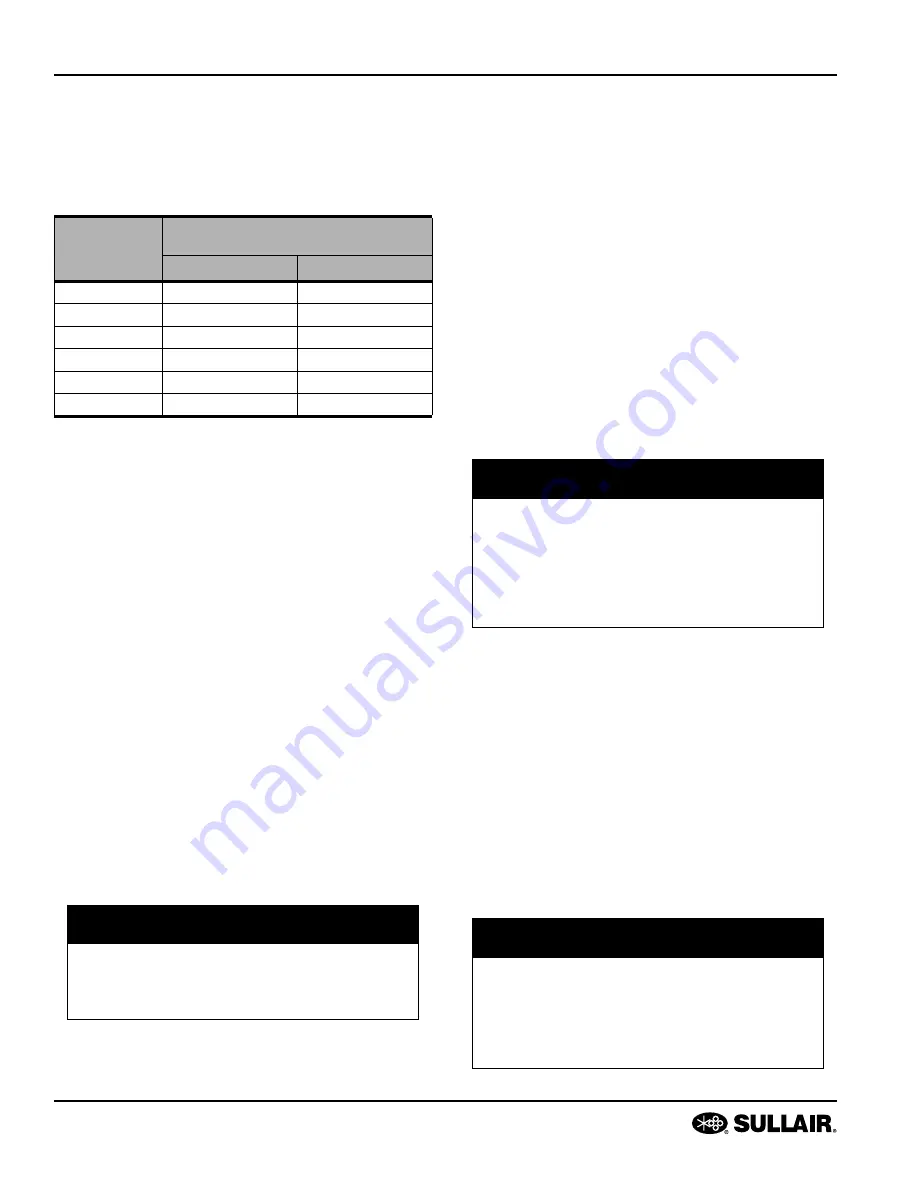
4: Installation
3000PB, 3700B, 4500B, 3000PVB, 3700VB, 4500VB User Manual
02250216-786 R01
46
Subject to EAR, ECCN EAR99 and related export control restrictions.
(1 m) before the cooler. The orifice size must be calcu-
lated to ensure that the maximum seawater flow rate can-
not be exceeded. Without these precautions, the
seawater flow rate through the cooler may be several
times the recommended maximum, which will lead to
rapid system failure.
No oil cooler manufacturer can guarantee that its prod-
ucts will have an indefinite life and for this reason, we
suggest that the cooling system be designed to minimize
any damage caused by oil cooler leaking. This can be
achieved as follows:
1. The oil pressure should be maintained at a
pressure higher than the seawater pressure.
In the event of a leak occurring, the oil will be
prevented from becoming contaminated.
2. When the hydraulic system is not in use, the
coolers should be isolated from incoming
seawater under pressure.
3. The seawater outlet pipe from the cooler
should have an open run to waste piping.
4.3
Outdoor installation (sheltered)
Many times a compressor must be installed outside due to
available space or other job site conditions. When this is nec-
essary, there are certain items that should be incorporated
into the system to help ensure trouble-free operation. The
unit must be purchased with a TEFC motor and optional
NEMA 4 controls, which are watertight. The standard
machine has NEMA 12 rated controls, which are dust-tight.
The compressor should be on a concrete pad, which is
designed to drain water away from it. If the concrete pad
is sloped, then the compressor must be mounted so that
it is level. The base or skid must be fully supported where
it contacts the concrete pad.
A weatherhood option should be selected to prevent
direct rain and snow from falling on the unit. If local
weather conditions can be extreme such that direct rain
or snow may fall on the unit, it should be in a fully
enclosed room or building.
If installed under a shelter, air-cooled machines must be
positioned in a way that prevents air recirculation (i.e.,
hot exhaust being allowed back to the system air inlet).
In installations that include more than one compressor,
hot air exhaust should not be directed toward the fresh
air intake of the second unit or an air dryer.
A standard machine installed outside must not be started
or run if the ambient temperature in and around the com-
pressor drops or may drop below 40°F (4.4°C).
For installation in a below freezing climate, a low ambient
option with heat tracing and a separator/sump tank
heater must be installed.
4.4
Service air piping
Review carefully the total air system before installing a
new compressor. Items to consider for the total air sys-
tem include liquid carryover, pipe sizing, and the use of
an auxiliary receiver tank. The installation of a drip leg or
multiple drip legs, installation of a line filter(s) and the
installation of isolation valve or valves. These consider-
ations are important to ensure a safe and effective sys-
tem. See
.
Seawater
pressure
Orifice diameter for maximum seawater
flow (or 40 US gal/min [152 L/min])
in
mm
25 psi (1.7 bar)
0.675
17
35 psi (2.4 bar)
0.62
16
45 psi (3.1 bar)
0.58
15
55 psi (3.8 bar)
0.55
14
65 psi (4.5 bar)
0.53
13.5
75 psi (5.2 bar)
0.51
13
NOTE
Variable speed drive compressors are NEMA 12
rated and must not be installed outside or
exposed to the elements.
NOTE
Compressors with integral dryers can be dam-
aged by ambient temperatures below freezing.
The dryer electrical system is NEMA 12 rated
and should not be installed outdoors or in an
unheated space, subject to freezing tempera-
tures.
NOTE
Discharged air contains a very small amount of
compressor lubricating oil, and care should be
taken to ensure that this oil would not interfere
with downstream equipment. Downstream fil-
ters and an air dryer can remove any carryover.