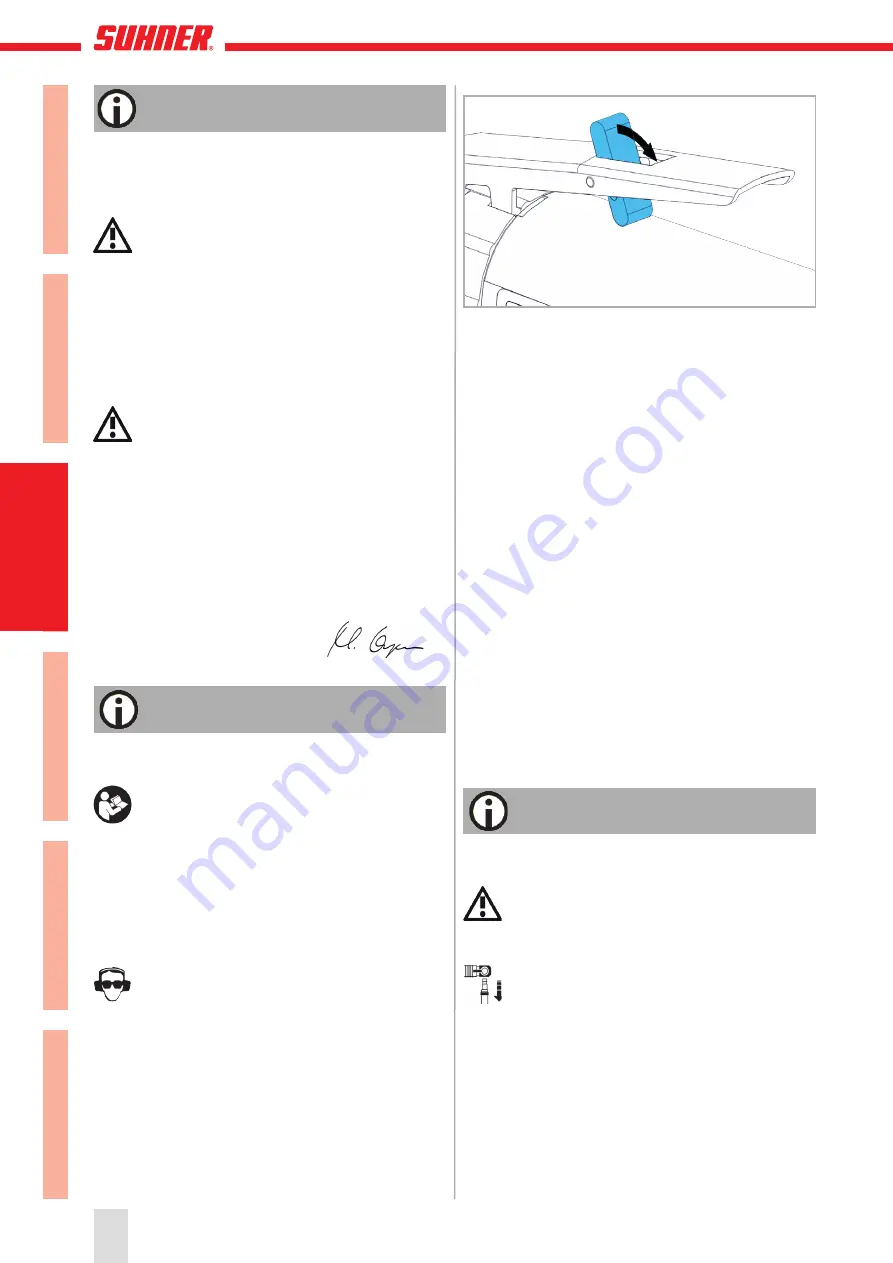
1.1 g
enerAl
notes
on
sAfety
This operation manual is applicable for the machine LWG
12.
The machine may only be handled by personnel
who are qualified.
1.2 u
se
of
the
mAchine
for
PurPoses
for
which
it
is
intended
The machine ist intended for the cutting, roughing and
brushing of metal and stone materials.
1.3 i
ncorrect
use
All uses other than those described under section
1.2 are regarded as incorrect use and are there-
fore not admissible.
1.4 ec
declArAtion
of
conformity
Otto Suhner GmbH, Trottäcker 50, D-79701 Bad Säck-
ingen, hereby declares under sole responsibility that
the product with the serial or batch no. (see reverse
side) complies with the requirements under the Directive
2006/42/EG. Applied standards: EN ISO 12100, EN ISO
11148. Document Agent: M. Voyame. D-Bad Säckingen,
08/2017.
M. Voyame/Division manager
2. c
ommISSIonIng
2.1 P
rior
to
tAKing
the
mAchine
into
serVice
Fitting of hose coupling (inside diameter min. 7
mm, available as optional accessory, item no. 908
057, type DN 8). Use oiled compressed air (see
also air quality under section 2.3). Observe national regu-
lations.
2.2 t
AKing
the
mAchine
into
serVice
2.2.1
turn
on
/t
urn
off
1. n
oteS
on
S
afety
Tilt lock forward an press lever onplastic sleeve. Releas-
ing the lever switches the machine OFF.
2.3 r
Ating
dAtA
Pressure
max. 6.3bar
Power output
900W
Air consumption full load
1.1m
3
/min
Air consumption at idling
0.6m
3
/min
Setting oiler idle
2-3 drops/min
Wheel diameter
max. 125mm
Spindel thread
M14 / 5/8”
Length of spindle thread stud
20mm
No-load speed
12’000min
-1
Sound pressure level EN ISO 15744 81dB(A), K=3dB(A)
Sound power level EN ISO 15744
92dB(A), K=3dB(A)
Vibration EN ISO 28927-12
7.8m/s
2
, K=2.6m/s
2
Air quality DIN ISO 8573-1
3/4/4
Weight 1.700kg
2.4 o
PerAting
conditions
Temperature range during operation: 0 to +40°C
Relative air humidity: 95% at +10°C not condensed
3. h
andlIng
/o
peratIon
3.1 P
rotection
deVices
The machine may only be operated with the safety
guards and the additional handle fitted!
3.1.1 s
Afety
guArd
The safety guard was already correctly adjusted in
the factory. With this adjustment it can be brought
into the desired working position, or removed.
When the pressure point is overcome the protective guard
must rotate and snap in again without the use of exces-
sive force. Otherwise, either the protective guard has to
be readjusted or the locking mechanism has to be
cleaned.
16
P
ortugúes
Español
Italiano
English
F
rançais
Deutsch
English