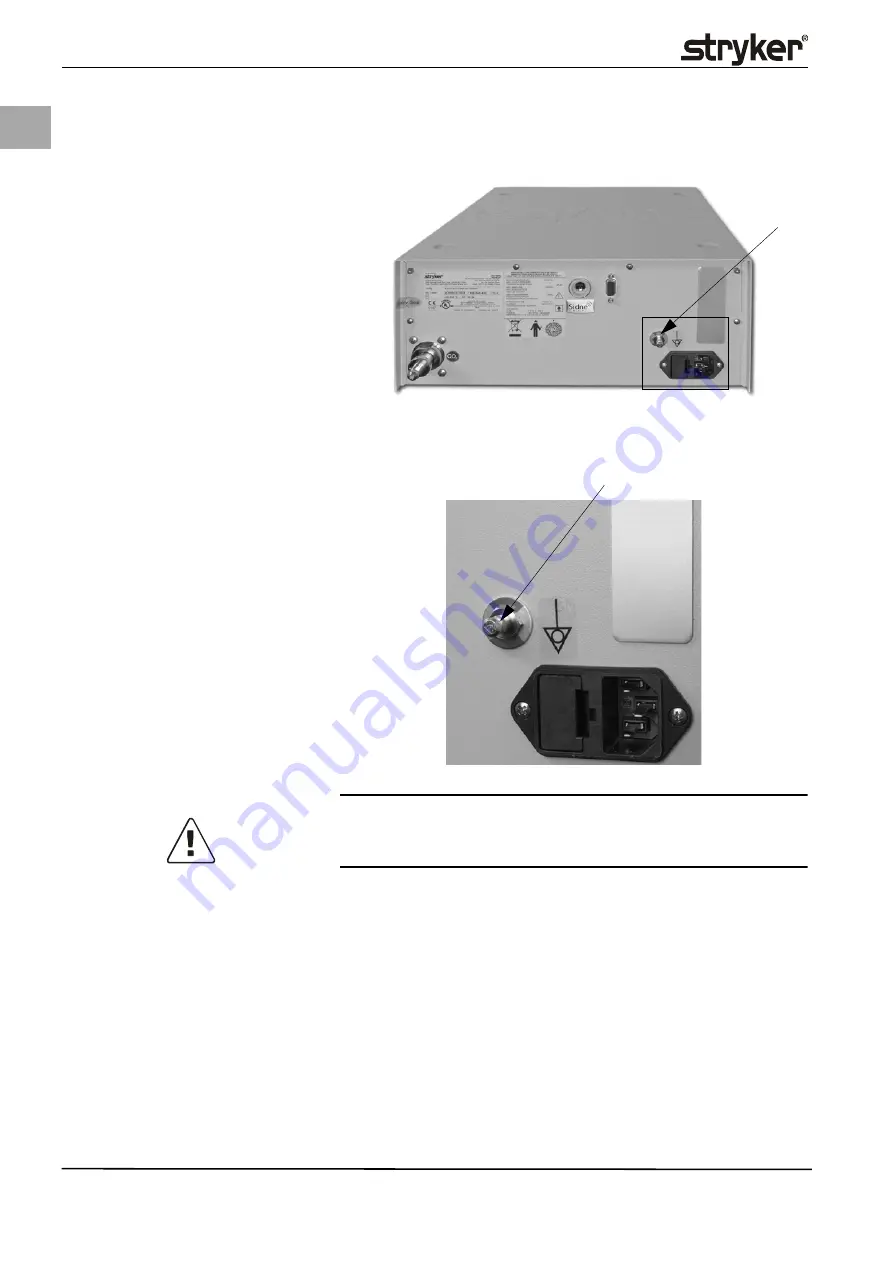
48
EN
Replacing Components and Modules
6.7
Uninstalling/Installing Potential equalization MC-Plug
DANGER!
Disconnect device from power supply.
1. Remove power connection cable from mains socket.
2. Use a size 10 socket wrench to remove the potential equalization plug
(1)
from the rear panel of the device.
3. Follow these steps in reverse for assembly.
Perform the following tests after installing the new component:
• Electrical safety test (see chapter 4.1 Safety Test).
Fig. 6-14 Position of potential equaliza-
tion plug
(1)
Potential equalization plug
A
(1)
Fig. 6-15 Detail A: Potential equalization
plug
(1)
Potential equalization plug
A
(1)
Содержание PneumoSure
Страница 10: ...8 EN Device Setup 3 3 Pneumo Sure Wiring Diagram ...
Страница 26: ...24 EN Service Menu 5 1 Service Menu Access ...
Страница 27: ...Service Menu 25 EN 5 2 Service Menu Overview 5 3 Chapter 5 4 5 5 5 11 5 14 5 6 5 7 5 8 5 9 5 10 5 12 5 13 ...
Страница 40: ...38 EN Service Menu ...
Страница 75: ......