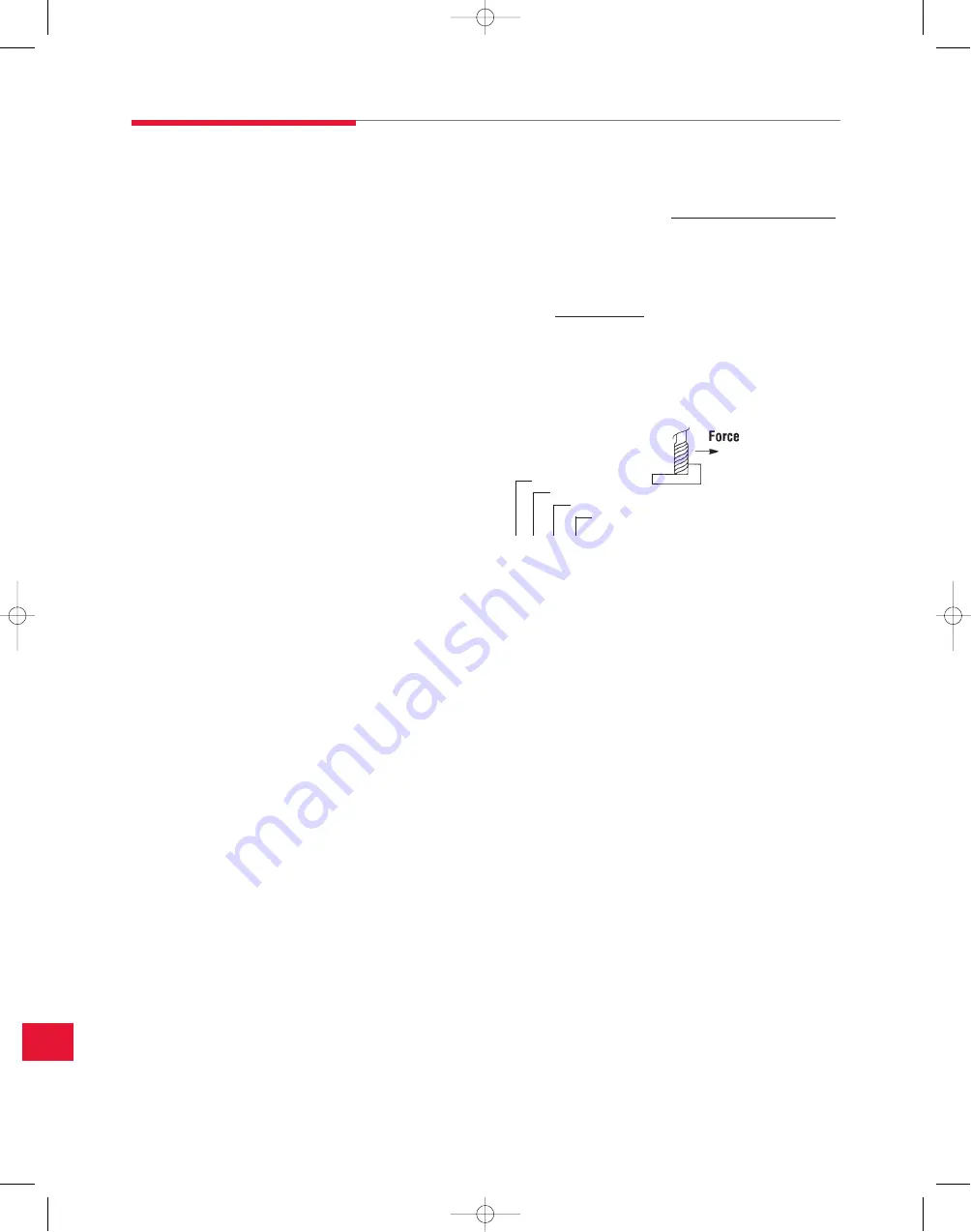
15.12
Subject to technical modifications without notice
DE-STA-CO
S
tr
o
n
g
H
o
ld
C
la
m
p
in
g
S
y
s
te
m
T
M
System Bleeding
Air trapped in the hydraulic system is the most common cause of erratic
operation and slow return times. The most common way to bleed a
system is to pressurize the circuit and carefully loosen a fitting just
enough to let fluid escape. The trapped air will usually be flushed out
with the fluid. With conventionally mounted components, the fittings
required for connection provide ideal bleeding locations. Since manifold
mounting eliminates external fittings and lines, the fixture
designer/builder no longer gets bleeding points by default and must
now consciously plan for system bleeding.
As workholding hydraulic systems become more sophisticated, compact
and automated, proper bleeding becomes increasingly important. Air
trapped in the system is most often revealed by the slow retraction of
single-acting (spring return) components. To understand why, picture
the following example:
Single-acting actuators – return springs develop 15 PSI
Flow required to clamp – 1 cu. in.
System pressure – 3,000 PSI
Return time for this application is dictated by the time it takes to force
1 cu. in. of fluid through all of the return line restrictions at 15 PSI.
Take the same example with 1 cu. in. of air (at atmospheric pressure)
trapped anywhere in the system:
When pressurized, this “bubble” compresses and becomes
200 times smaller or .005 cu. in. This means that .995 cuin,
of oil must be pumped into the system just to compress the
bubble. Now when the clamps are released, 1.995 cu. in. of
fluid must leave the system – nearly double that of the same
system without air.
Calculating Machining Forces
To help you choose the right cylinders, clamps, and work supports, it is
important to know how much clamping or supporting force
is necessary.
There are numerous ways to calculate the approximate forces that the
cutting tool places on the workpiece.
Please note that the results of
these calculations are estimates and must never replace experience,
common sense, and caution.
In addition, these results indicate only the
magnitude of the force, not the direction. Depending on the specific
application, the direction of the force may vary significantly from the
beginning to the end of the cut.
Milling, Turning and Boring
A rough estimate of cutting tool force – if the horsepower required to
make the cut is known – is the result of the following equation:
For example, an operation is expected to take 5 horsepower with a cutting
speed of 150 surface feet per minute.
Where horsepower is not yet known, a value called unit power comes
into play. Unit power is the horsepower required to remove one cubic
inch of material in one minute. (Refer to Table A on Page 10.)
Milling
Example: a 4-flute end mill is used to machine aluminum. The cut is
1⁄2" deep and the feed per tooth is .002". From the table the unit power
value is 0.4. So the cutting force transferred to the workpiece is:
.5 x .002 x 4 x .4 x 125,950 = 202 lbs.
Cutting Force
Note that this calculation assumes a full width cut. Applications using
less than the full cut may reduce the calculated force by the percentage
of the full cut being taken.
Turning and Boring
A similar calculation applies to turning and boring. Note that the cutting
force is usually perpendicular to the cutting tool but since the tool or
workpiece is rotating, the direction of the force relative to the work
piece is constantly changing.
HP x 24,750
Cutting Speed (SFPM)
Cutting Force (lbs.) =
5 x 24,750
150
= 825 lbs. Cutting Force
Depth of Cut (in.)
Feed per Tooth (in.)
Number of Teeth
Unit Power
___X___X___X___ X 125,950 = _____ lbs.
Cutting Force
System design information
15_StrongHold.qxp:15_DES_StrongHold-1-14.indd 1/2/08 9:03 AM Page 15.12