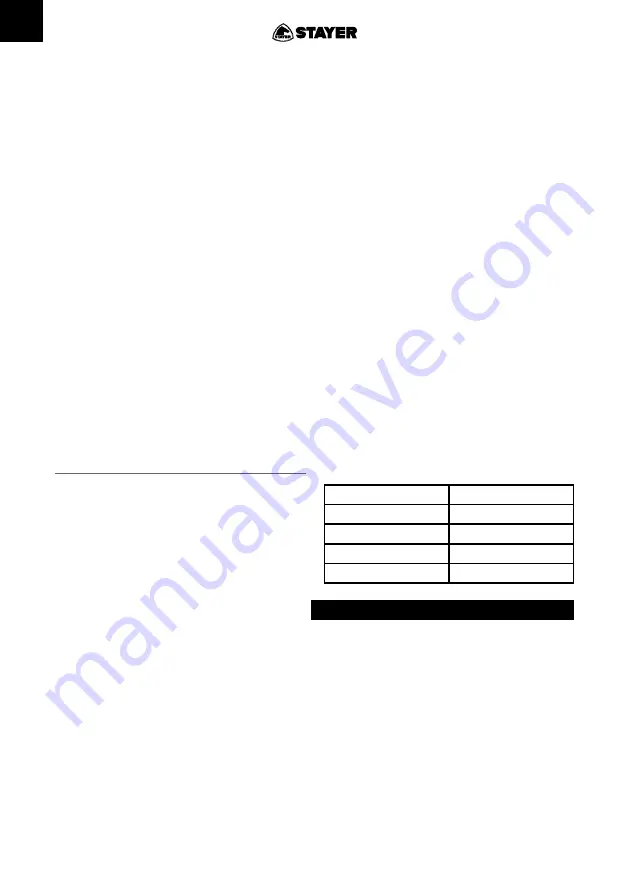
gb
-
10
-
Tightening torque adjustment
In the tool's rear there is an LCD screen which signals
the tightening torque. Under the screen there are two
buttons, one to fasten the torque and the other one
to loosen it. You can set the automatic tightening stop
within 150Nm and 350Nm. If you keep pressing the
fastening button the screen will show a '888' message
meaning the tool will keep tightening as long as the
trigger is activated.
Loosening torque adjustment.
T
he tool does not have a loosening adjustment. The
tool will apply the maximum torque 500Nm spinning to
the left for a fast and efficient loosening.
Reversing the rotational direction
The rotational direction switch is used to reverse the
rotational direction of the machine. However, this is not
possible with the On/Off switch actuated.
–
Right rotation:
Press the rotational direction switch rightward to
the stop.
–
Left rotation:
Press the rotational direction switch leftward to the
stop.
Switching On and Off
– To start
the machine, press the On/Off switch and
keep it pressed.
– To switch off the machine, release the On/Off
switch.
To save energy, only switch the power tool on
when using it.
WORKING ADVICE
Before any work on the machine itself, pull the
mains plug.
Apply the power tool to the screw/nut only when
it is switched off.
Rotating tool inserts can slip off.
At temperatures below the freezing point, run the ma-
chine for approx. 3 minutes at no-load to improve its
lubricating capacity.
The torque depends on the impact duration. The maxi-
mum achieved torque results from the sum of all indivi-
dual torques achieved through impact. The maximum
torque is achieved after an impact duration of 3–5
seconds. After this duration, the tightening torque is
increased only minimally.
However, the transmission housing heats up
noticeably.
Note:
The consequences of excessive heating-up are
high wear of all hammer mechanism components and
a high requirement of lubricant.
The impact duration is to be determined for each
required tightening torque. The actually achieved
tightening torque is always to be checked with a torque
wrench.
Screw Applications with Hard, Spring-loaded or
Soft Seat
When in a test, the achieved torques in an impact
series are measured and transferred into a diagram,
resulting in the curve of a torque characteristic. The
height of the curve corresponds with the maximum
reachable torque, and the steepness indicates the
duration in which this is achieved.
A torque gradient depends on the following factors:
– Strength properties of the screws/nuts
– Type of backing (washer, disc spring, seal)
– Strength properties of the material being screwed/
bolted together
– Lubrication conditions at the screw/bolt connection
The following application cases result accordingly:
– A
hard seat
is given for metal-to-metal screw
applications with the use of washers. After a relatively
short impact duration, the maximum torque is reached
(steep characteristic curve). Unnecessary long impact
duration only causes damage to the machine.
– A
spring-loaded seat
is given for metal-to-metal
screw applications, however with the use of spring
washers, disc springs, studs or screws/nuts with coni-
cal seat as well as when using extensions.
– A
soft seat
is given for screw applications, e. g.,
metal on wood or when using lead washers or fibre
washers as backing.
For a spring-loaded seat as well as for a soft seat, the
maximum tightening torque is lower than for a hard
seat. Also, a clearly longer impact duration is required.
Reference Values for Maximum Screw/Bolt
Tightening Torques
Calculated from the tensional cross-section; utilization
of the yield point 90 % (with friction coefficient μtotal =
0.12). As a control measure, always check the tighte-
ning torque with a torque wrench.
Nut size
Nm
M10-M12
40-80
M12-M16
100-200
M14-M16
120-200
M18-M24
200-350
2_MAINTENANCE AND SERVICE
Maintenance and Cleaning
Before any work on the machine itself, pull the
mains plug.
For safe and proper working, always keep the ma-
chine and ventilation slots clean.
In extreme working conditions, conductive dust
can accumulate in the interior of the machine
when working with metal. The protective insula-
tion of the machine can be degraded. The use of
a stationary extraction system is recommended in
such cases as well as frequently blowing out the
ventilation slots and installing a residual current
device (RCD).
Содержание IW 500 D K
Страница 12: ...NOTES...
Страница 13: ...NOTES...