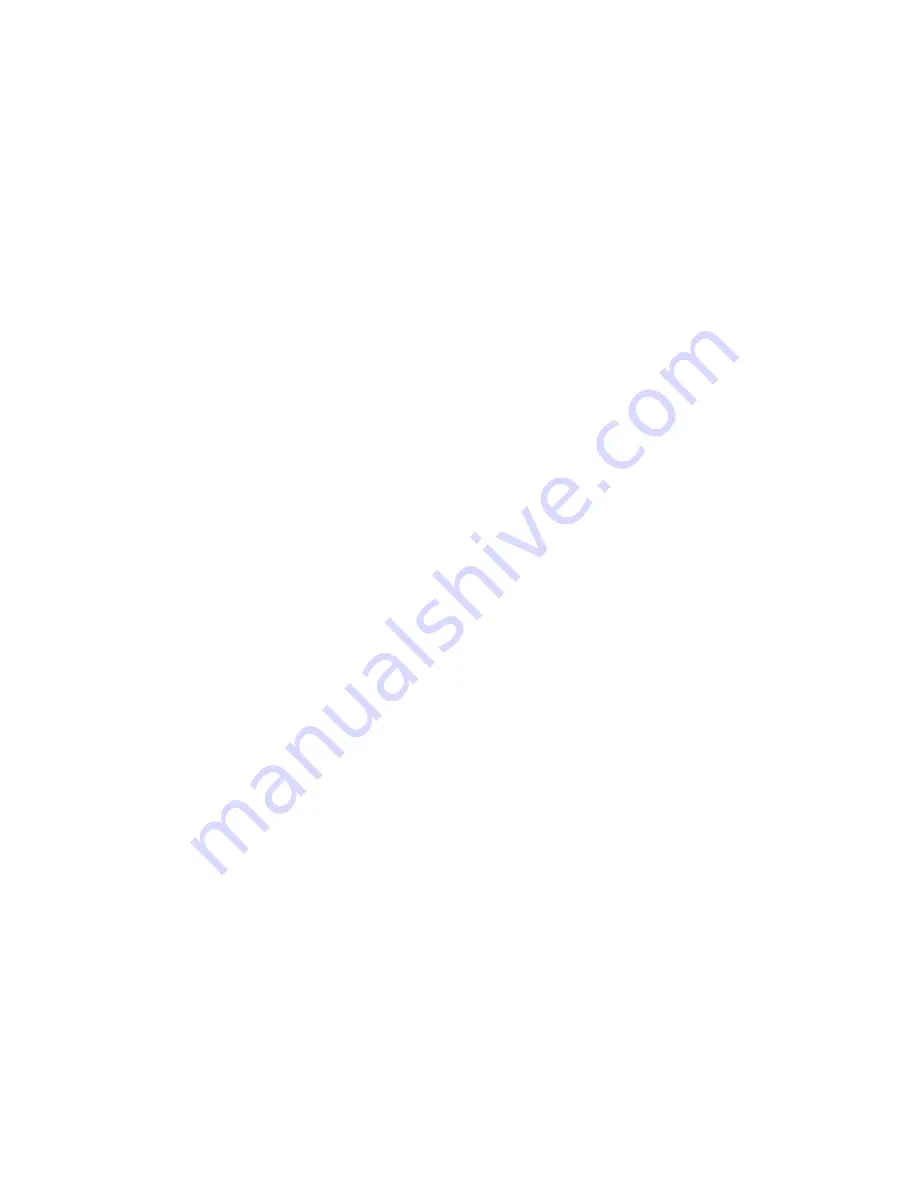
20
value. For attenuation under different frequencies, it will increase as the
frequency.
Secondly, due to coarse crystal particle and if coarse out-phase structure
exists, it will cause abnormal reflection, i.e. the grass-shaped echo or
tree-shaped echo, so that the measuring will have error reading, and
cause wrong judgment.
Thirdly, as the crystal particle is coarse, the anisotropy in flexibility in
metal’s cryst
allizing direction will be obvious, which results in difference
in sound velocities in different directions, and the max. difference can
even be up to 5.5%. What’s more, the compactness in different positions
of the work piece is different, which will also cause difference in sound
velocity. All of these will produce inaccuracy in measurement. Therefore,
one must be very careful in measuring castings.
During measuring castings, please pay attention to the following points:
1.
When measuring casting with un-machined surface, please use engine
oil, consistent grease and water glass as coupling agent.
2.
Calibrate the sound velocity for the object with a standard test piece
having the same material and measuring direction as that for the object
to be measured.
3.
If necessary, take 2-point calibration.
6 Preventing errors in measurement
6.1 Ultra-thin Material
For any ultrasonic thickness-gauge, when the thickness of object is less
than the low limit of the probe, it will cause measurement error. When
necessary, measure the min. limit thickness by comparing with the test
pieces.
When measuring ultra-
thin object, sometimes error called “double
refraction” may occur, its result is that the displayed readout is twice of