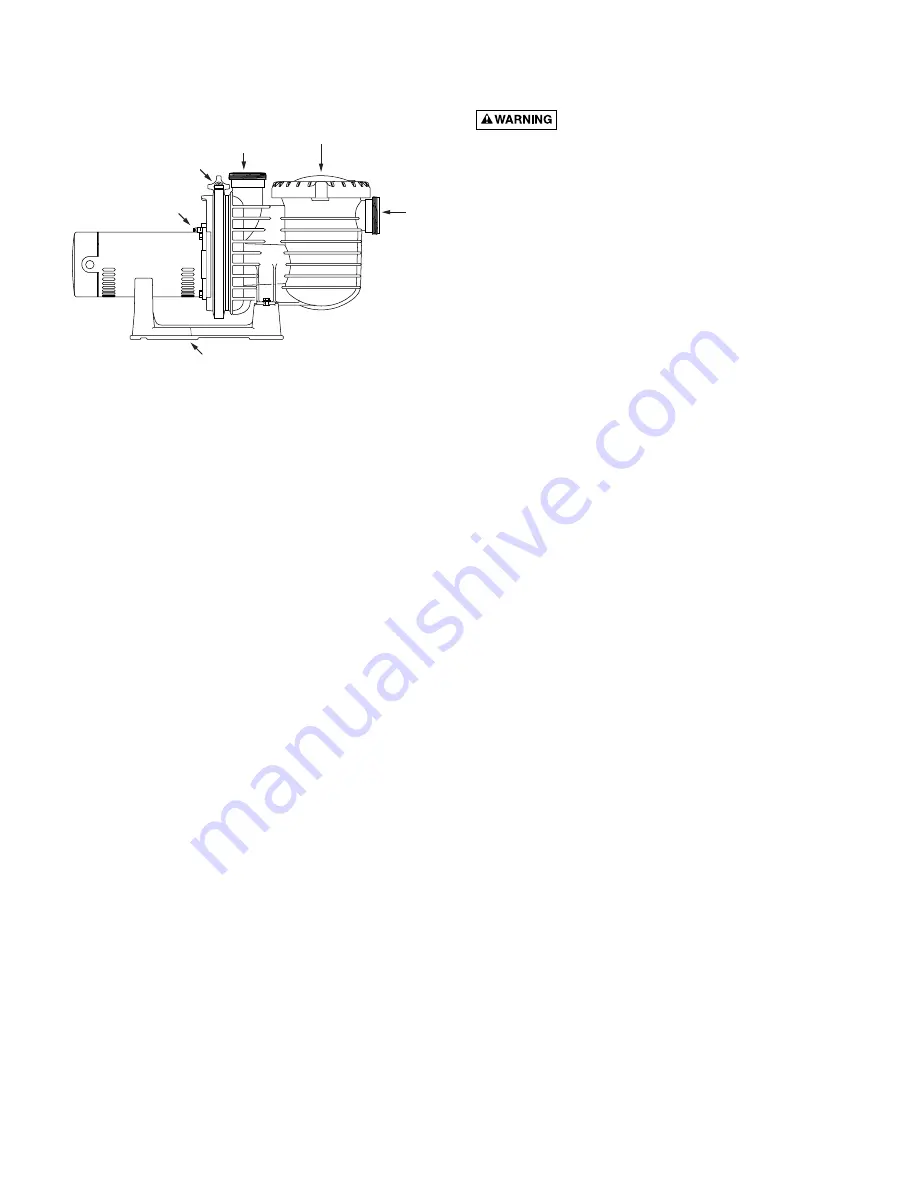
3
INSTALLATION
Only qualified, licensed personnel should install pump
and wiring.
Pump mount must:
Be located away from corrosive or flammable chemicals.
Have enough ventilation to maintain air temperature at less
than the maximum ambient temperature rating (Max. Amb.)
listed on the motor model plate. If this pump is installed in
an enclosure/pump house, the enclosure must have ade-
quate ventilation and air circulation to keep the tempera-
ture in the enclosure at or below the motor’s rated ambient
temperature whenever the pump is running.
Be solid - Level - Rigid - Vibration free. (To reduce vibra-
tion and pipe stress, bolt pump to mount.)
Allow pump suction inlet height to be as close to water
level as possible.
Allow use of short, direct suction pipe (To reduce friction
losses).
Allow for gate valves in suction and discharge piping.
Have adequate floor drainage to prevent flooding.
Be protected from excess moisture.
Allow adequate access for servicing pump and piping.
NOTICE:
Use Teflon tape or Plasto-Joint Stik
1
for making
all threaded connections to the pump. Do not use pipe
dope; pipe dope will cause stress cracking in the pump.
NOTICE:
Pump suction and discharge connections have
molded in thread stops. DO NOT try to screw pipe in be-
yond these stops.
Fire and burn hazard.
Modern motors run at
high temperatures. To reduce the risk of fire, do not allow
leaves, debris, or foreign matter to collect around the
pump motor. To avoid burns when handling the motor, let
it cool for 20 minutes before trying to work on it.
Teflon Taping Instructions:
Use only new or clean PVC pipe fittings.
Wrap male pipe threads with one to two layers of Teflon
tape. Cover entire threaded portion of pipe.
Do not
overtighten or tighten past thread stop in pump
port!
If leaks occur, remove pipe, clean off old tape, rewrap
with one to two additional layers of tape and remake the
connection.
NOTICE:
Support all piping connected with pump!
1
Lake Chemical Co., Chicago, Illinois
Piping:
Use at least 2" IPS PVC (51mm) pipe. Increase size if a
long run is needed.
To avoid strains on the pump, support both suction and
discharge pipes independently. Place these supports near
the pump.
To avoid a strain left by a gap at the last connection, start
all piping at the pump and run pipe
away
from the pump.
Never use a suction pipe smaller than pump suction con-
nection.
To avoid airlocking, slope suction pipe slightly upward
toward the pump.
NOTICE:
To prevent flooding when removing pump for
service, all flooded suction systems
must
have gate valves
in suction and discharge pipes.
Fittings:
Fittings restrict flow; for best efficiency use fewest possi-
ble fittings.
Avoid fittings which could cause an air trap.
Pool fittings must conform to International Association of
Plumbing and Mechanical Officials (IAPMO) standards.
Use only non-entrapping suction fitting or double suction.
Suction
Port
from
pool or
vacuum
filters
Strainer Basket
cover
Discharge Port
to filter
or pool
Clamp
Knob
Bonding Lug
Pump may be bolted to level
foundation or mounting bracket
4284 1102
Figure 1