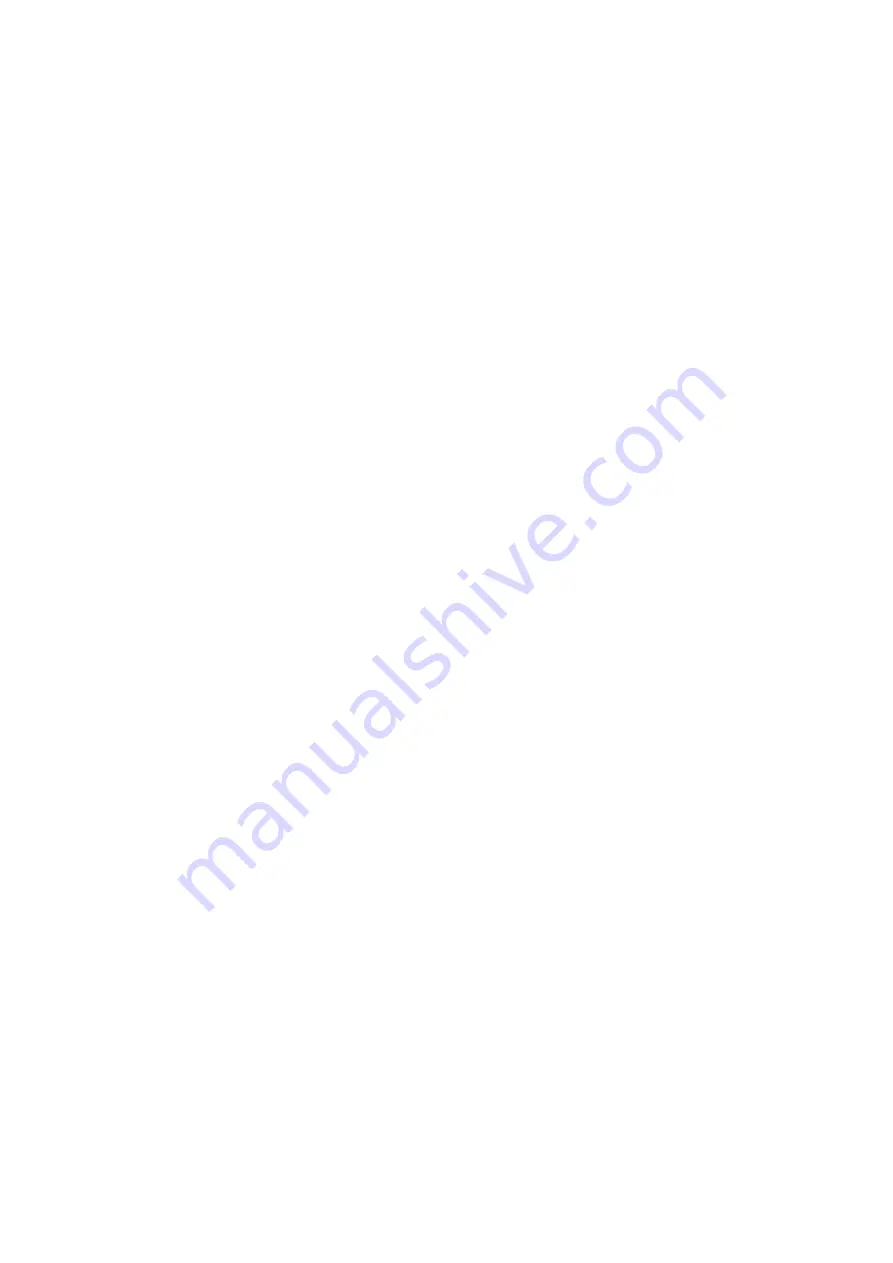
- 16 -
14. Plug mains electric supply into back of control (Item 14) and lock into position.
When
wiring up the mains supply the earth must be wired to the factory mains earthing
system.
15. Item 15 at the back of the control is for a remote trigger for tuning the unit to switch on
and off with an existing production line. If not using, make sure the dust cap is fitted and
locked into place.
16. Wire the earthing cables from the drum to the earthing point at the rear of the control.
Item 13.
17. The drum must be earthed in 2 places. With the earthing contacts rubbing against the
wall of the drum. The out going vibratory conveyor from the drum must always be
earthed.
ATOMIZATION
1. The part to be coated must be connected to the ground continuously.
2. Keep the spray unit perfectly clean.
3. Do not use the equipment if there is an air leak in the hoses.
4. Be sure that the product does not come closer than 15 cm / 6" and no further than
45cm/18” from the spray head.
5. Before plugging in the power supply unit, be certain the electrostatic generating unit’s
spray nozzel is installed correctly. There are inserts on the spray nozzle which rest on the
electrostatic generating head. (If fitted incorrectly the locking ring will not engage Item 1
Page 13)
POWDER FLOW SYSTEM
1 -
Position the cone under the screw feeder (using an addaptor if required), it must
be aligned correctly to allow the powder to fall into the cone
NOT IN THE CENTRE
BUT TO ONE SIDE
so the powder
rolls
into the injector.If the powder is dropped in the
centre it will
block up
the injector inlets
2 - Screw the injector into the bottom of the cone
(Make sure the the injector is screwed
together tightly and is fully closed to the end of the thread)
3 - Attach the powder feed hose into the spray nozzle. (See page 13)
(Make sure the hose
is pressed fully home in the nozzle and the locking ring is pulled firmly into place)
4 - Position the spray head at about a 45 angle to the product
5 - The electrostatic generating head need not be moved for cleaning. The system is IP65
6 - The system must be set-up to freely transport the powder at the maximum line rate, i.e.
set the air pressure at the electrode spray nozzle (0.25 - 2.0bar) as if the plant is at
maximum production.