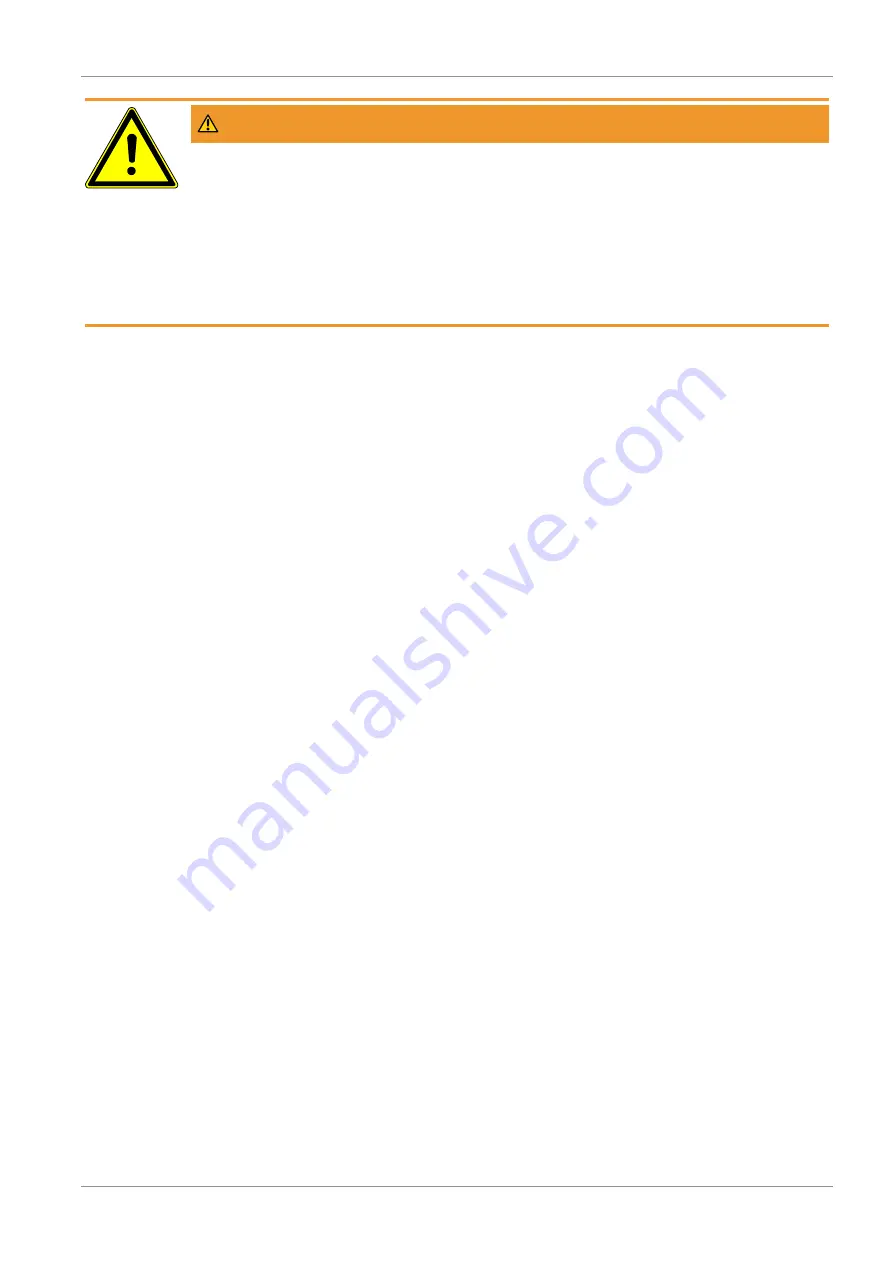
Spectron Gas Control Systems GmbH
Operation | 7
GES_BE56-2U_0720
23
WARNING
Gas source exchange
If a gas source exchange is performed incorrectly, gas leakage and poisoning of persons may
occur.
a) The gas source exchange are to be carried out by trained specialist personnel and never
unattended.
b) A pressure test must be conducted after each gas source exchange.
c) For each gas source exchange, a new seal suitable for the used gas is to be used.
d) Wear the personal protective equipment prescribed in the risk assessment.
With each gas source exchange, check the port for leak-tightness. We strongly recommend re-
placing the seal every time the gas source is exchanged. Always turn the shut-off valves slowly
and as far as the stop when opening or closing them!
Changing the supply side
1. The position of the lever indicates which side the gas is drawn from:
Switching lever up – gas is drawn from the gas cylinders on the left-hand side: The outlet
pressure of the pressure regulator on the left is set higher than that of the pressure regulator
on the right.
Switching lever down – gas is drawn from the gas cylinders on the right-hand side:
The outlet pressure of the pressure regulator on the right is set higher than that of the pres-
sure regulator on the left.
Middle position - If the handle is positioned horizontally, the two pressure regulators are set
to the same outlet pressure.
2. The gas cylinder pressure on the preselected side falls below the outlet pressure of the re-
serve side: the reserve side takes over the job of supplying process gas to the connected
consumers without interruption.
With single-stage switching panels, the outlet pressure falls markedly when there is
an automatic switch from the preselected operational side to the reserve side. When
the switching lever is operated, the reserve side is raised to the normal outlet pres-
sure level and thus becomes the operational side. Two-stage switching panels keep
the pressure very largely constant.
3. Move the switching lever to increase the outlet pressure again on the reserve side that has
now become the operational side.
4. Change the gas cylinder on the side that has now become the reserve side.
Removing the empty process gas source:
1. Close the process gas source valve.
2. Close valve HPI.
3. Open valve HPV to reduce the pressure.
4. Close valve HPV.
5. Disconnect the process gas source connection.
6. Mount the sealing nut on the gas source valve and protective cap on the process gas
source.
7. Identify, secure and remove the empty process gas source.
Connecting the new process gas source:
1. Provide new process gas source, position in front of the bracket and secure using the safety
chain.
2. Remove and retain the protective cap and screw plug.
3. Check the port thread and sealing; a new sealing must be used each time the gas source is
exchanged.