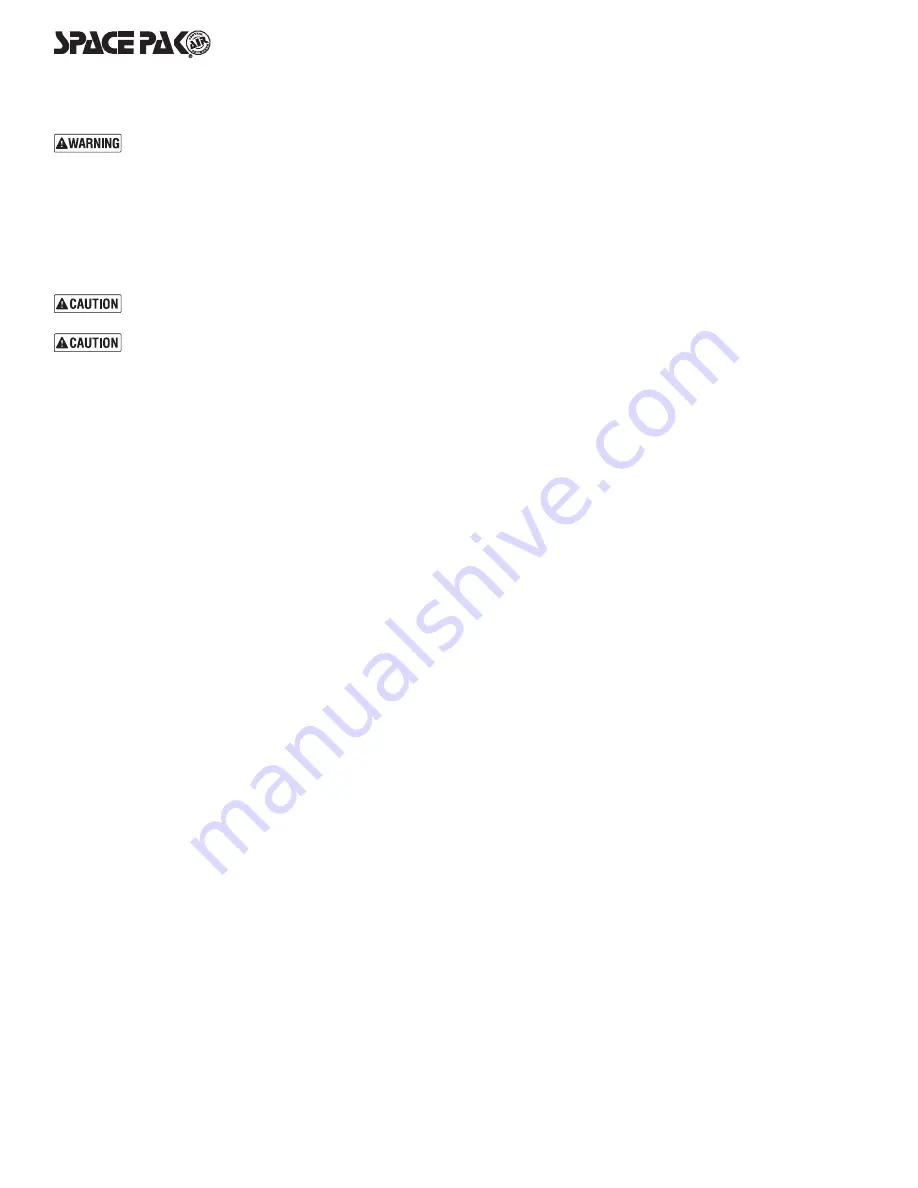
– 8 –
Split Inverter Air-to-Water Heat Pump
Glycol / Water Mixture
If unit is operating in a cooling capacity then the
water system must contain a mixture of inhibited
glycol and water with thermal protection sufficient
for the coldest expected temperature for the
installation. The inhibitor level can degrade over
time, and may need to be adjusted periodically.
The inhibitor is essential to prevent the glycol from
accelerating corrosion of metal components in the
system. The glycol and inhibitor levels must be
checked regularly (no less than once annually).
The minimum allowable concentration of glycol is
10% by volume in all installations.
Automotive glycol is not suitable for use in the SIS
system. Over time it may leave deposits which will
degrade the performance and damage pumps or
other devices in the system. Use only propylene
glycol mixtures specifically labeled for boiler or
HVAC use.
Obtain all components specified in the Typical System Diagram.
Make sure all components and piping comply with applicable
local codes.
DO NOT
use galvanized pipe anywhere in the system.
Galvanizing will react with the glycol and can cause glycol
degradation and sludge in the system.
• Confirm charge of expansion tank is 12-15 PSIG (with no
water or pressure in the system).
• Install the system piping. DO NOT connect the SpacePak
unit to the system piping until the system has been cleaned
as required below.
The SIS must NOT be connected to the system during this
process.
1.
Connect a hose from a fresh water supply to the system fill
hose bib. Note the drain port can be used for this purpose.
The hose bib purge/drain valve should be located low in the
system and close to the SIS return connection.
2.
Open the high point purge valve, (not shown in illustration, as
it may be inside the air handler) while slowly filling the system.
Close the valve when air is removed from the system and water
begins to flow out of the valve.
3.
Fill the system with fresh water and run water until the system
has been thoroughly flushed clean.
Automatic Fill – When an automatic fill system is installed, the
cooling fluid (Glycol/water) must be inspected at least every 3
months, or whenever a leak is detected to ensure the proper
glycol concentration is maintained.
Pressure Test The System
1. Add water to the system as needed to raise the pressure to
25 PSIG (verify that all system components are suitable for
this pressure). Verify that the pressure remains constant for
at least one hour. Locate and correct any leaks.
2. After successfully testing, drain the system and remove the
fresh water hose.
3. After testing and draining the system, apply pipe insulation.
Fill system with glycol/water mixture. Calculate the system
volume.
4. See Table 1, for required glycol concentration for the minimum
expected outside temperature.
5. Obtain the required volume inhibited glycol/water solution
premixed or mix in a clean container. (The glycol must contain
an inhibitor to prevent metal corrosion.)
6. Pump the glycol/water solution into the system, allowing air
to escape through the purge valve(s).
7. After filling the system, sample the system fluid and verify
glycol and inhibitor percentages, following instructions
provided with the glycol.