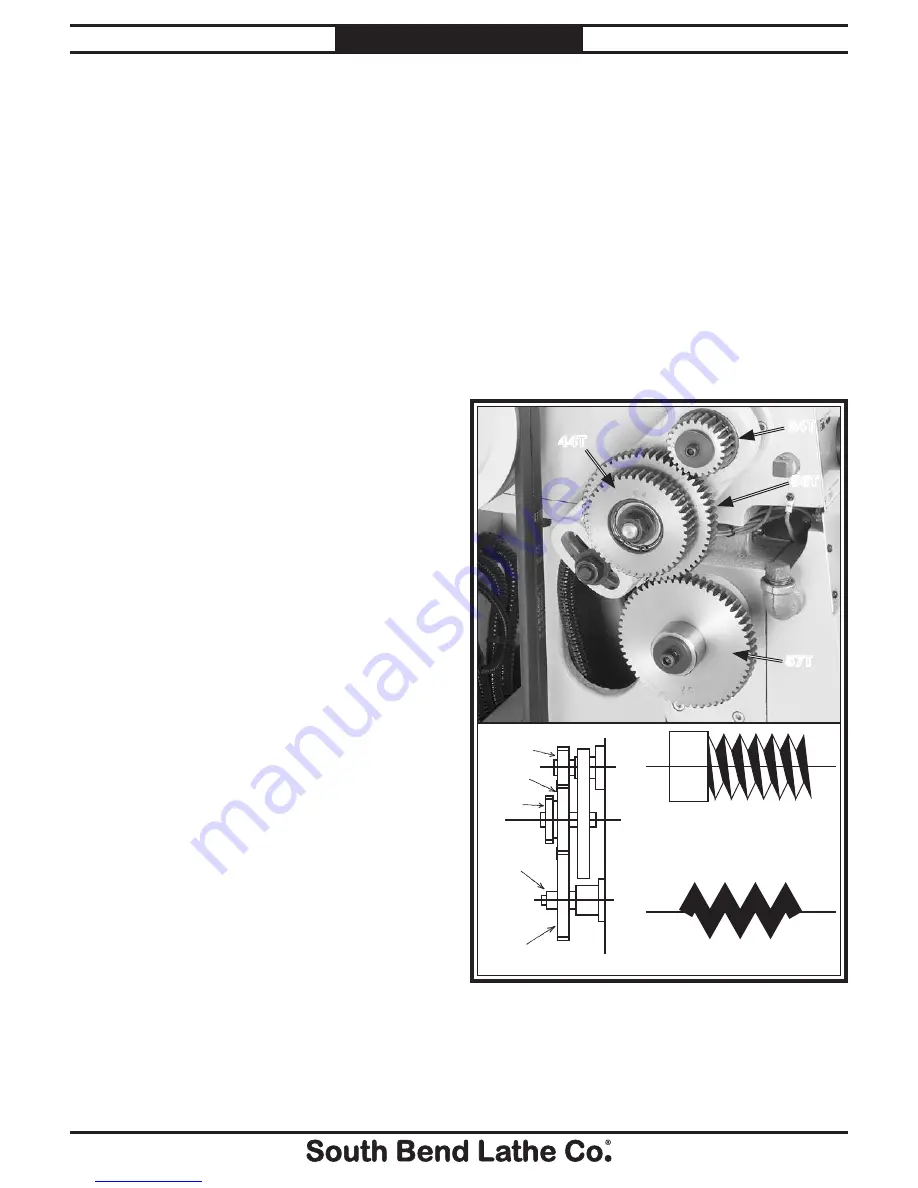
-56-
For Machines Mfg. Since 3/11
16-Speed Gearhead Lathe
O P E R A T I O N
3.
The configuration string of characters to
the right of the selected feed rate (LCS8W)
displays the positions to set the feed controls
for a feed rate of 0.18mm/rev.
4.
Position the controls as indicated in the
following instructions. If needed, use the
chuck key to rock the spindle back-and-
forth to help mesh the gears as you make
adjustments.
a)
Move the feed range lever to the low (L)
position.
b)
Point the left gearbox lever to the "C".
c)
Move the middle gearbox lever to the
"S".
d)
Position the bottom gearbox lever in the
"8" slot.
e)
Point the right gearbox lever to the "W".
The lathe is now set up for a power feed rate of
0.18mm per spindle revolution.
The end gears on the side of the headstock can be
setup for the standard or alternate configuration,
depending upon the type of operation to be
performed. The lathe is shipped with the end
gears in the standard configuration.
To access the end gears, remove the end gear
cover from the left side of the headstock
Standard End Gear Configuration
Use the standard end gear configuration (see
Figure 83
) for inch threading, metric threading,
and all general feed operations.
End Gears
57T
56T
24T
Inch and Metric Pitch
Threading
Inch and Metric Feeding
44T
Spacer
24T
44T
56T
57T
Figure 83. End gears in the standard configuration.
Downloaded from
www.Manualslib.com
manuals search engine