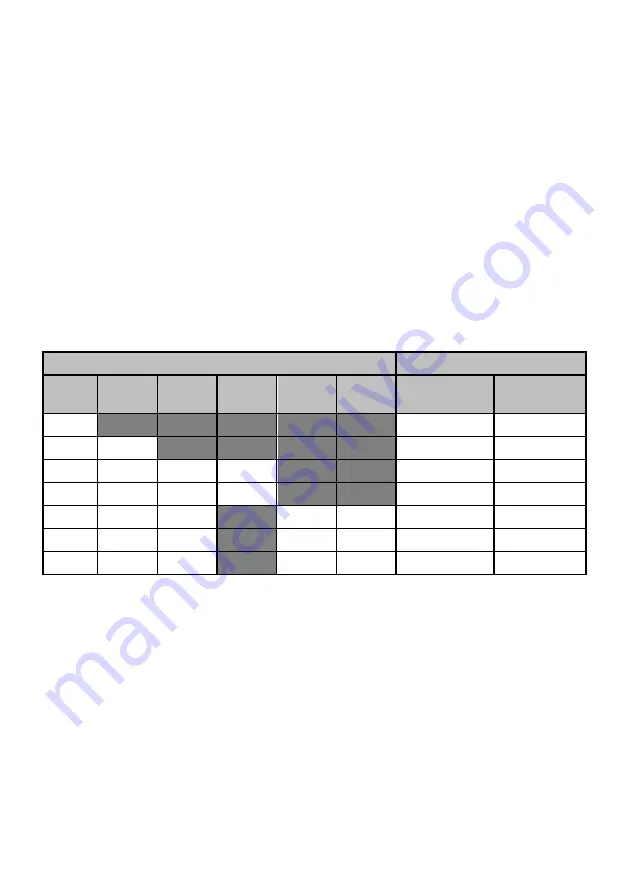
-28-
5.1.1
Switching on
Push the power switch 5 (Fig. 1) forward until it engages. If the milling motor is connected to the mains voltage,
the setting wheel
X
(Fig. 2) lights up in blue (BU) and the milling motor accelerates to the previously set speed
after 0.2 s with a soft start. The duration of the soft start depends on the set speed and is approx. 1.2 s at
maximum speed.
5.1.2
Switching off
Push onto the rear end of the power switch 5 (Fig. 1). The switch audibly jumps back to off position. The lighting
on the setting wheel
X
(Fig. 2) goes out and the motor coasts to a standstill.
5.2
PV design
With the PV design
Y
(Fig. 2) you can control the speed via the PV interface and automatically monitor the
remaining runtime in the event of overload.
To protect the user and the connected systems, the PV interface is electrically isolated from the power supply of
the drive train (safety isolation). All signal and operating voltages refer to the reference potential
“GND”
.
As soon as the supply pin
“U
PV
”
of the PV interface is supplied with voltage in accordance with the specification,
the milling motor switches to “portal mode”.
The bottom status table 3 shows all possible control constellations.
Input
Output
HS / -
U
AC
/ V
U
PV
[V]
PS
S
U
S
[V]
U
0
/ V
Operating
mode
n [rpm]
OFF
N/A
N/A
N/A
N/A
N/A
Out of operation 0
ON
0
N/A
N/A
N/A
N/A
Out of operation 0
ON
198-253
< 6
1
N/A
N/A
Manual mode
4000
ON
198-253
< 6
6
N/A
N/A
Manual mode
25000
ON
198-253
8 - 56
N/A
0
0 - 1
Portal mode
4000
ON
198-253
8 - 56
N/A
10
0 - 1
Portal mode
25000
ON
198-253
8 - 56
N/A
0 - 10
1.5 - 5
Overload mode
4000 - 25000
Table 3: Possible control constellations