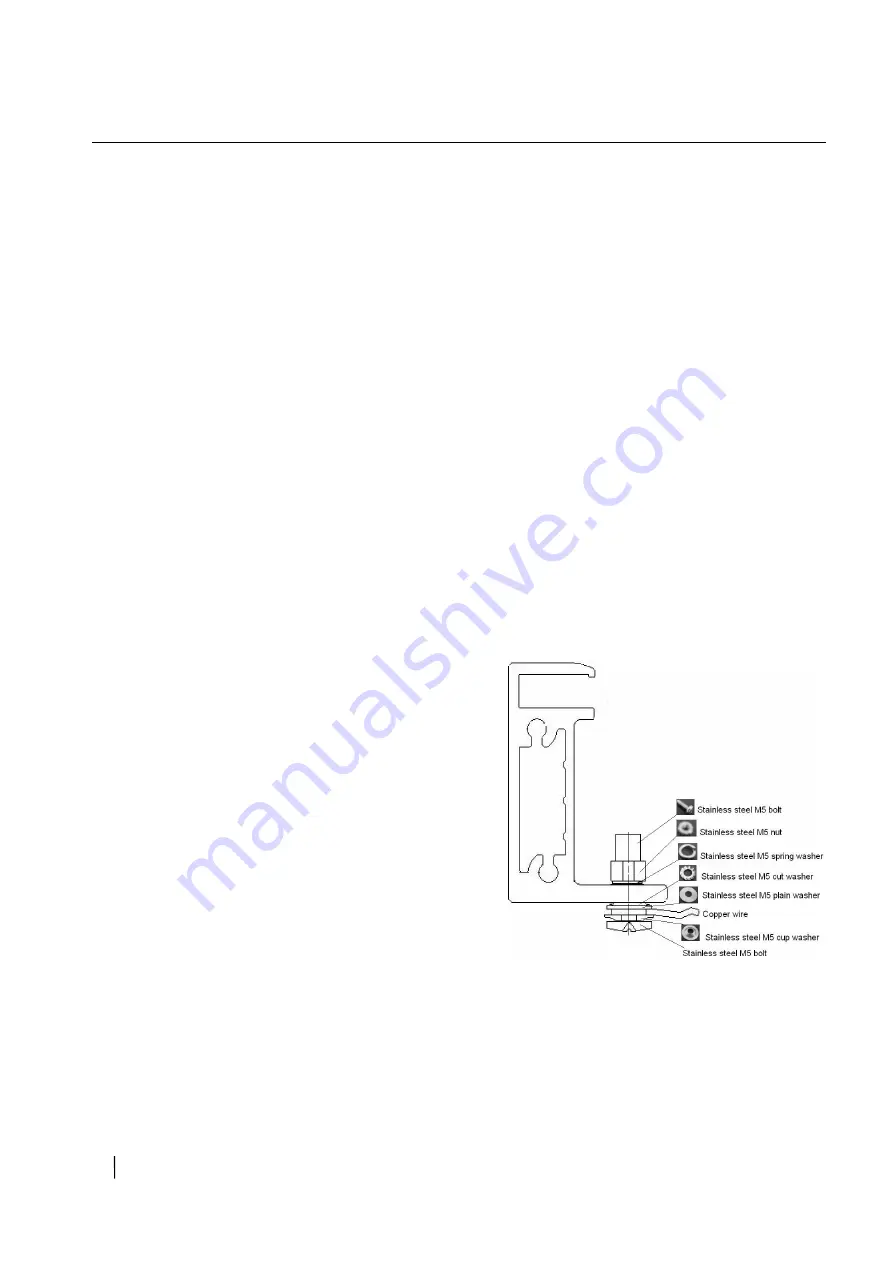
15
PV modules with different electrical performance
models cannot be connected in one string.
The system shall use special cables and connectors
for PV system and ensure that all connections are
securely fastened. The cable must be 4mm
2
(i.e. 12
AWG) and withstand the maximum possible open-
circuit voltage of the PV system.
When fixing the cable to the rack, it is necessary to
avoid mechanical damage to the cable or to the PV
module. Do not press the cable hard. To secure the
cable to the rack in the proper way, specially
designed UV-resistant coils and cable clips must be
used. Avoid direct sunlight and water soaking to the
cable.
Keep the connectors dry and clean and make sure
that the nuts on the connectors are tightened before
connecting them. Do not connect the connectors
when they are damp, contaminated or in other bad
conditions. Avoid exposing connectors to direct
sunlight and soaking in water. Avoid the
connectors falling on the ground or the roof. Do
not plug or unplug the connectors when the PV
module is in
live state. When it is necessary to
remove the connectors, ensure that the PV
module is not in working condition and that
professional unlocking tools and safety
measures are used. Direct dragging and pulling
is forbidden.
The junction box of the PV module contains
bypass diodes connected in parallel to the string of
the PV module. The bypass diode in the junction
box prevents module degradation due to shading or
covering. Refer to the junction box diode
specification provided in the relevant product
datasheet for more details. I When the localized hot
spot phenomenon occurs in the PV module due to
partial shading or coverage, the diode in the junction
box will start to work, so that the module current will
no longer flow through the hot spot cell, to limit the
heat and loss of the PV module. When a diode failure
is suspected or found, please contact Solahart team
and do not attempt to open the junction box cover.
6.3
Grounding
The PV modules are designed with an anodised,
corrosion-resistant aluminum alloy frame as a rigid
support. To ensure safety and to avoid lightning strikes
and electrostatic damage to the PV modules, the PV
module frame must be earthed. The earthing device
must be in full contact with the interior of the aluminum
alloy of the frame, penetrating the surface oxide film.
The following is the specific grounding method, as
shown in Fig. 15.
Fig. 15
Grounding the aluminum frame with copper wire
The grounding requirements must be checked in
accordance with the applicable regulations and
standards before work is started.
Use the marked 5.5 mm grounding holes to ground the
anodized frame. Use one M5 nut, two M5 cut washers,
one M5 plain washer, one M5 spring washer, and one