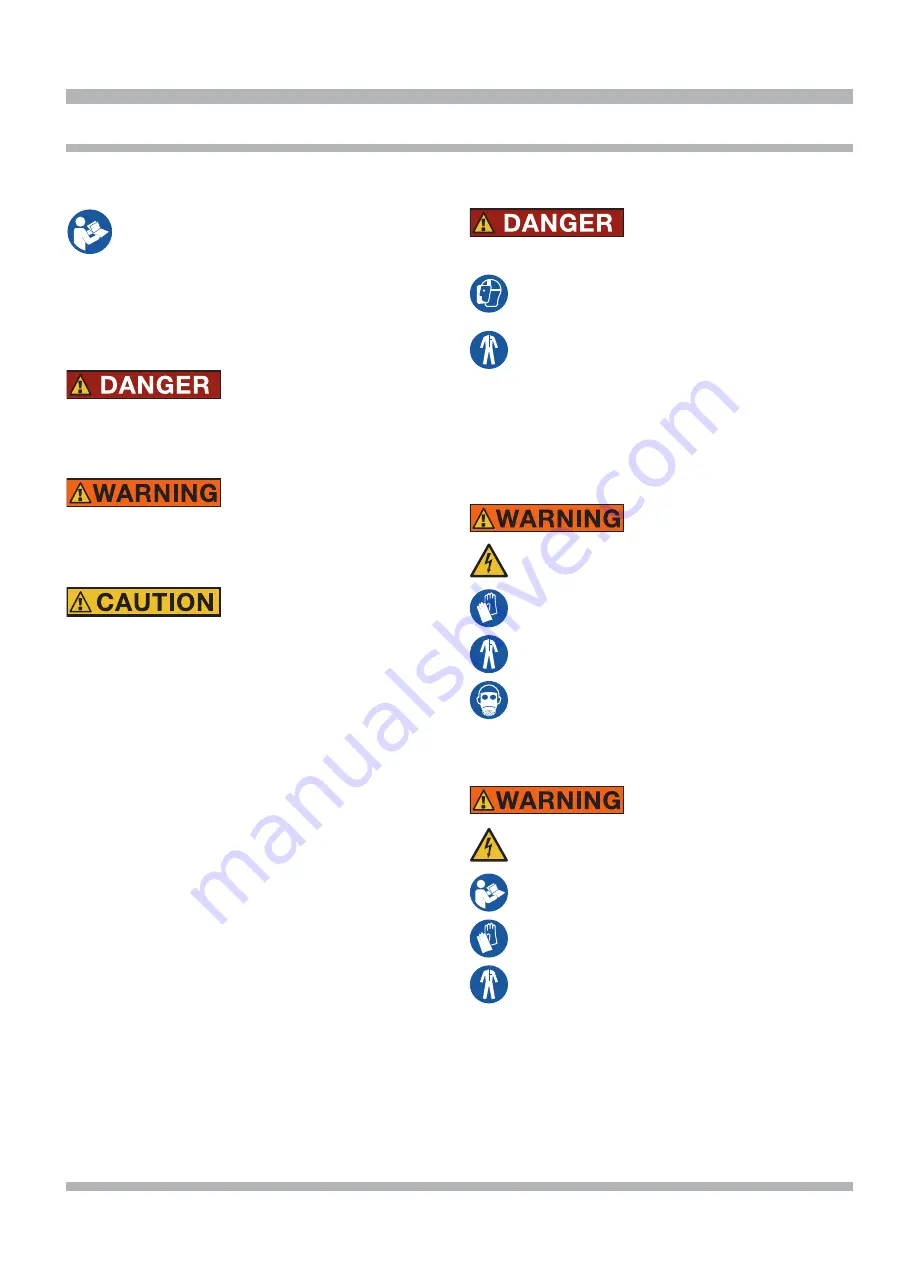
3
SAFETY INFORMATION
MUST READ INSTRUCTIONS BEFORE USE
Read, understand and follow all safety messag-
es and instructions in this manual. Safety mes-
sages in this section of the manual contain a sig-
nal word with a three-part message and, in some
instances, an icon.
The signal word indicates the level of the hazard in a situ-
ation.
Indicates an imminently hazardous situation which, if not
avoided, will result in death or serious injury to the opera-
tor or bystanders.
Indicates a potentially hazardous situation which, if not
avoided, could result in death or serious injury to the op-
erator or bystanders.
Indicates a potentially hazardous situation which, if not
avoided, may result in moderate or minor injury to the
operator or bystanders.
IMPORTANT
Indicates a situation which, if not avoided, may result in
damage to the welding equipment.
Safety messages in this section contain three different
type styles.
• Normal type states the hazard.
•
Bold
type states how to avoid the hazard.
•
Italic
type states the possible consequences of not
avoiding the hazard.
An icon, when present, gives a graphical description of
the potential hazard.
Arc Welding
Electric welding or plasma cutting causes ultra-
violet rays and weld spatter.
Bystanders will be exposed to ultraviolet rays
and weld spatter.
Wear welding helmet with appropriate shade
lens while using electric welders or plasma
cutters.
Do not allow bystanders while welding or
cutting.
Wear safety shield and protective clothing.
Ultraviolet rays will burn eyes; weld spatter can
cause injury.
Welding produces heat, sparks, hazard of elec-
tric shock and/or hazardous vapors
Wear appropriate gloves, helmets or goggles
and other protective clothing.
Follow all instructions and safe practices
while welding or cutting.
Keep bystanders away from immediate area.
Byproducts of welding can cause burns or other
bodily injury.
Risk of Electrical Shock
Electrical shock can result when contacting live
electrode or internal components
Electrical shock can result from absence of
grounding lug.
Welding machine must be connected to
power source in accordance with applicable
electrical codes.
Do not touch electrode or internal compo-
nents without protection.
Disconnect power before servicing.
Do not remove the grounding lug in any elec-
trical plug.
Electrical shock can cause injury.
Содержание MIG200i
Страница 16: ...16 REPLACEMENT PARTS PARTS LIST ...
Страница 19: ...19 WIRING DIAGRAM WIRING DIAGRAM ...