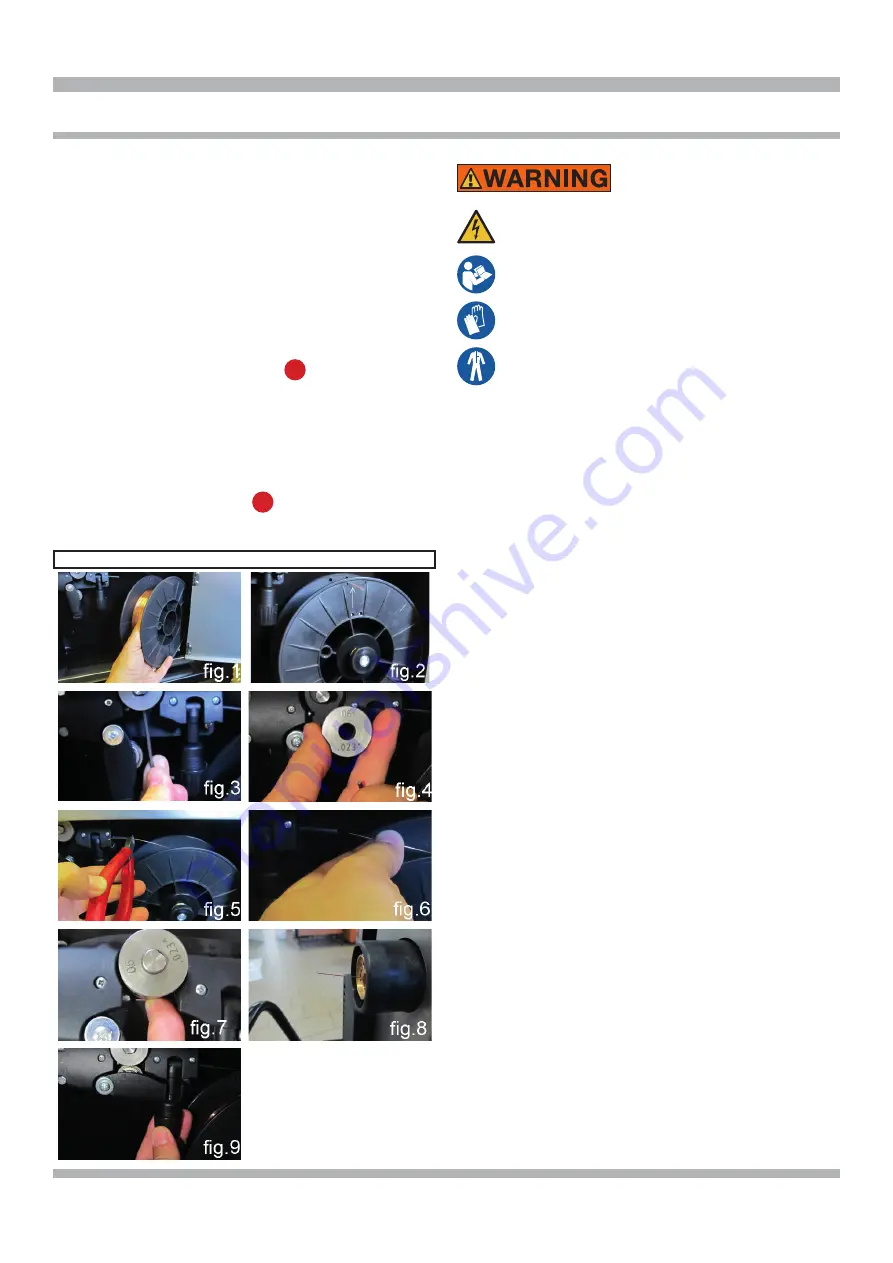
7
ASSEMBLING THE UNIT
Position the welding machine so as to allow the free circulation
of air inside and, as much as possible, prevent metal or other
dusts from penetrating.
• The machine must be installed by professional personnel.
• All the connections must be performed in compliance
with applicable standards (IEC/CEI EN 60974-9) and with
accident-prevention laws.
• Make sure the power supply voltage corresponds to the
welding machine rating.
• The protection fuses must be sized according to the details
shown on the technical data plate.
Make sure the ground wire
D
, inside the reel
compartment, is connected to the negative pole
coming out of the dividing wall.
The polarity is stamped alongside the two terminals, the
polarity is stamped on. The positive pole + is that at the
top, nearest to the wire feed motor. The negative pole – is
the one lower down, nearest to the ground lead exit.
Connect the ground lead clamp
D
to the piece to be welded.
Open the side door. Install the wire reel according to the
instructions provided below.
REEL FITTING SEQUENCE
Electrical shock can result when contacting live
electrode or internal components
Electrical shock can result from absence of
grounding lug.
Welding machine must be connected to
power source in accordance with applicable
electrical codes.
Please refer to the troubleshooting tip section
located at our web site (www.800ABCWELD.
com) for information on wiring the 220 V plug
if needed.
Do not touch electrode or internal compo-
nents without protection.
Disconnect power before servicing.
Do not remove the grounding lug in any elec-
trical plug.
Electrical shock can cause injury.
During wire installation, the welder must be switched
off and unplugged to prevent the moving motor roller to
move presenting a risk for the operator.
• Install the reel on the support inside the compartment
as shown in fig. 1.
• The reel must be installed on the support so the
wire unwinds in an counter-clockwise direction. It is
important for the wire to be stopped on the reel on the
side closest to you, see fig. 2. Install the reel on the
support, as shown in the illustration.
• Make sure the drive roller is correctly positioned
according to the diameter and type of wire used. To
remove the roller, align the flat part of the roller-bearing
pin at the bottom, so the key can be fitted inside the
retention screw. Loosen the screw, remove the roller,
install the roller back on so the race corresponds to the
wire used, see figures 3 and 4.
• Cut the wire with a Snap-on cutting pliers 87ACF or
equivalent, keeping it between your fingers so that it
cannot unwind, insert it inside the plastic tube exiting
from the gear motor and, with the aid of a finger, also
insert it inside the steel tube until it comes out of the
brass adapter, see figures 5-6-7-8.
• Close the drive arm, being careful of the wire, which
must be aligned with the roller race, see fig. 9.
• Install the welding torch.
After installing the reel and torch, switch on the machine,
select the suitable synergic curve, following the
instructions given in the service functions (
PROCESS
PARAMS
) paragraph. Remove the gas nozzle and
unscrew the current nozzle of the torch. Press the torch
button until the wire comes out.
Содержание MIG160i
Страница 14: ...14 REPLACEMENT PARTS PARTS LIST ...
Страница 16: ...16 WIRING DIAGRAM ...