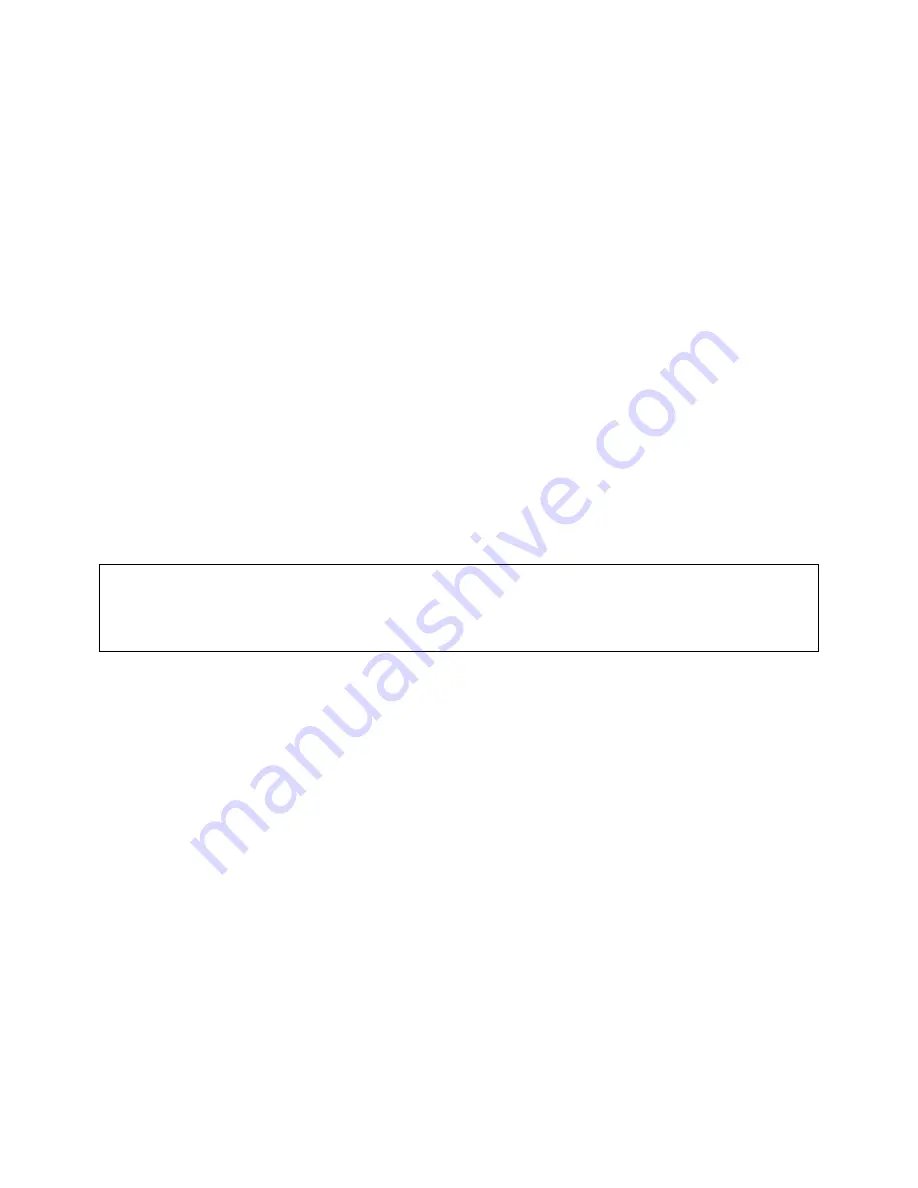
6 of 11
Raising the Jack Beam
1.
Press the up button and hold until jacking beam is at full working height and the automatic
safety is in place. Lower the jack beam onto the safety (Note: there are two safety stops to
allow multiple working heights).
NOTE: NEVER WORK ON A VEHICLE UNLESS THE SAFETY LOCK IS
ENGAGED AND THE JACKING BEAM CANNOT BE LOWERED.
Lowering the Jack Beam
1.
To lower the jacking beam, first raise the jack up off the mechanical safety lock and release
the safety lock using the safety release lever.
NOTE:
THE SAFETY LEVER MUST BE MANUALLY HELD IN THE RELEASED
POSITION.
2.
Press the control handle to release pressure allowing the jacking beam to lower to its full
down position.
3.
Never operate a jacking beam that is not in proper working order or in a manner not
recommended by the vehicle or jacking beam manufacturer.
ALWAYS ENSURE THAT THE MECHANICAL SAFETY IS ENGAGED WHENEVER
A VEHICLE IS SUPPORTED BY THE JACKING BEAM.
Recommended Maintenance
1.
Inspect the jacking beam on a daily basis to ensure the jacking beam is in proper working
condition.
2.
Make certain that the automatic safety drops into place when the jacking beam is raised and
that it will release when held in the down position during lowering.
3.
Check the hydraulic fluid when jacking beam is in the lowered position by removing the
filler breather cap.
4.
Keep the air source clean and make certain that an air filter is used to keep dirt out of the air
motor.
5.
Keep the entire jacking beam as clean as possible at all times.
6.
To maintain a clean shop air supply, (oil, lube, filter and regulator) should always be in good
working order in conjunction with the use of an oiler/separator.