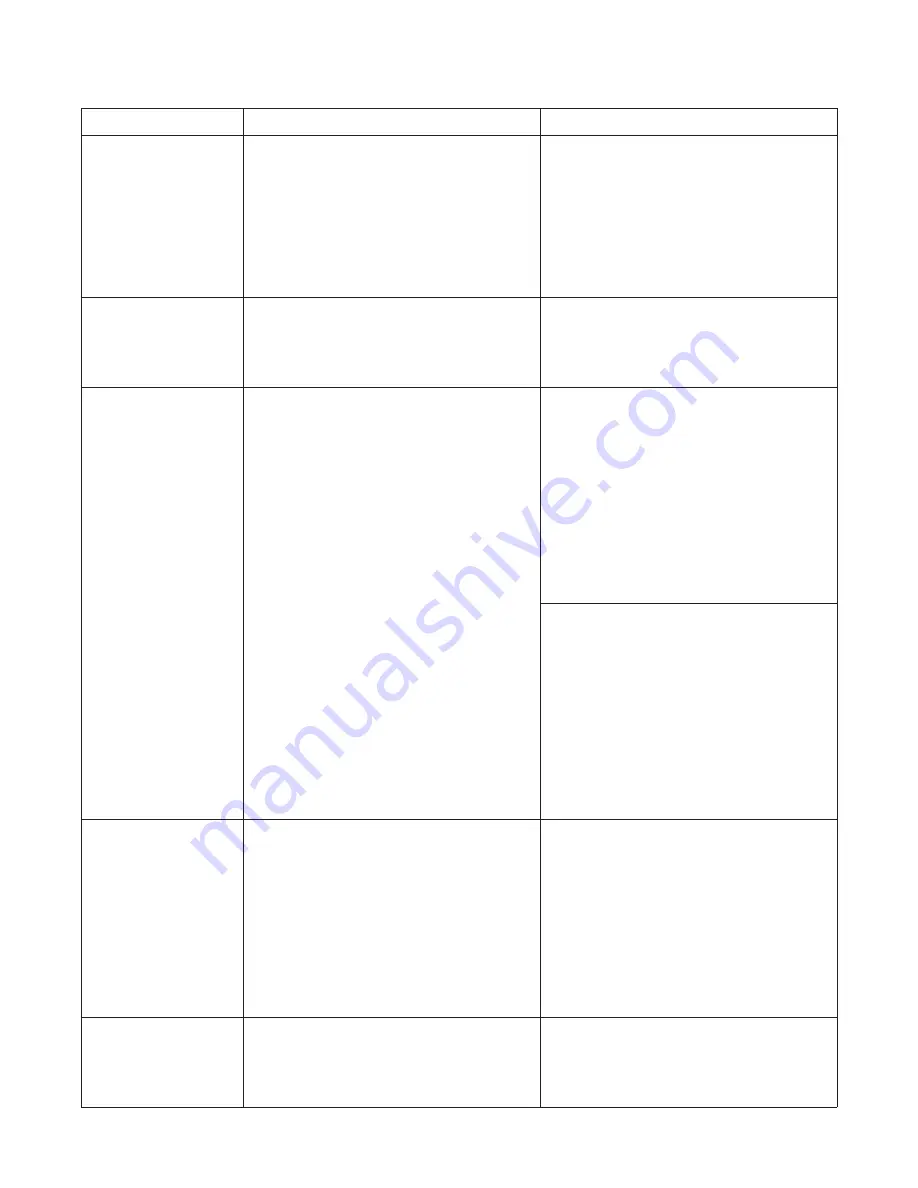
GT INSTALLATION AND OPERATION INSTRUCTIONS
Page 35
Problem
Detected
Problem
Solution
This device protects the integrity of the
plastic venting material.
If the temperature of the fl ue gases
exceeds
225°F
,
107°C
, the limit will cut
power to the control. Blocked internal
tubes can increase the stack temperature
to an unacceptable level. Flush out the
boiler.
If the combustion sequence is normal,
and there is no fl ame prior to ignition, the
Fenwal control is defective, and must be
replaced.
If the condensate drain gets blocked,
the boiler will become fl ooded, and
terminate operation, as the fl ame rod
becomes immersed. This will damage
the fl ame probe. To correct, free the drain
blockage, and permanently prevent it from
reoccurring. Remove and dry off the probe.
Reinstall the probe and try for ignition, if
it fails to ignite, leave the fan run for up to
three hours to dry out the insulation and
probe.
Reset Boiler so it will attempt to ignite.
Check for proper operation of ignition
components. Make sure igniter glows and
gas valve opens.
Check for proper line pressure at gas
valve when it opens.
If boiler lights check for fl ame signal
between FC1 And FC2 on Fenwal control.
If lower then 1.2 micro amps see Boiler
will not stay lit below.
Check combustion properties.
If the Burner light on the Sentry is going
out, go to “Burner shutting off”.
Check condensate drain for blockage and
check the inlet piping for ingested snow
or water (if the fl ame rod gets wet, it may
need to be replaced). Check for resistance
from fl ame rod to ground, must be an
open circuit (O.L).
Check for proper polarity of line and
neutral wiring to the boiler.
Ensure the plumbing is as shown in
manual. Check to see if pumps are faulty
or end switches are stuck. This problem
can lead to boiler overheating!
Stack Safety Limit Trips (Automatic Reset)
Located on the front of the fl ue box.
The Fenwal controller thinks that there is a
fl ame prior to ignition.
Indicates Ignition Lockout.
Indicates lack of a good fl ame signal. In
order to stay running the fl ame signal must
be at least 0.7 micro Amps.
Bangs or sounds like a kettle while burner
is running indicating insuffi cient fl ow.
Ignition Sequence
not activated when
burner light is on
(Fan is on and
Fenwal not fl ashing)
continued
Two Flashes on
Fenwal
Three Flashes on
Fenwal
Boiler will not stay
lit.
Boiler bangs or
hisses
Содержание GT-150
Страница 19: ...GT INSTALLATION AND OPERATION INSTRUCTIONS Page 19 Figure 30 Multiple 4 Wire Zone Valves...
Страница 22: ...GT INSTALLATION AND OPERATION INSTRUCTIONS Page 22 Figure 33 Boiler Ladder Diagram...
Страница 23: ...GT INSTALLATION AND OPERATION INSTRUCTIONS Page 23 Figure 34 Boiler Connection Diagram...
Страница 38: ...GT INSTALLATION AND OPERATION INSTRUCTIONS Page 38 Figure 48 Replacement Parts Exploded View SIOM 36...
Страница 40: ...WESTCAST INC 260 NORTH ELM STREET WESTFIELD MA 01085 TEL 413 562 9631 FAX 413 562 3799...