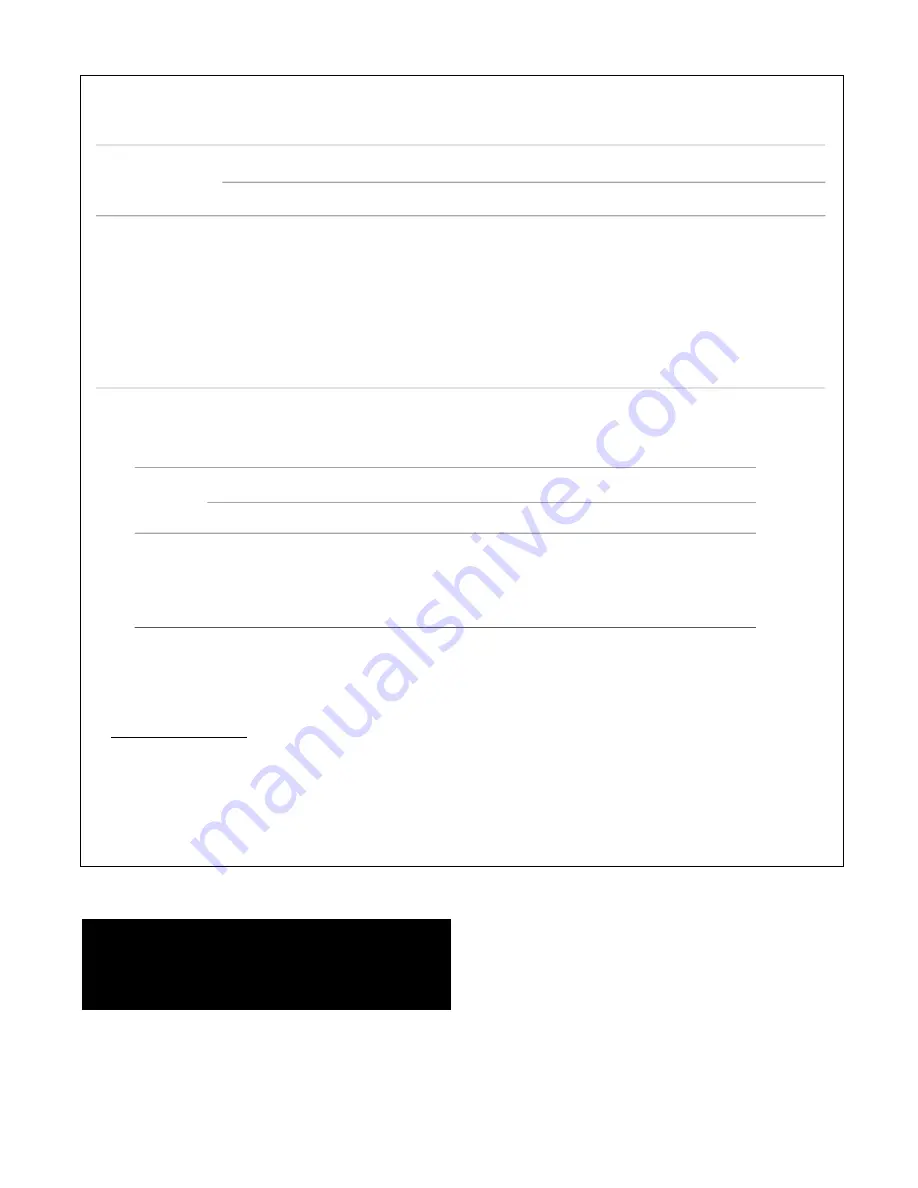
Maximum Capacity of Pipe in Cubic Feet of Natural Gas per Hour for Gas Pressures of
0.5 Psig or Less and a Pressure Drop of 0.3 Inch Water Column
(Based on a 0.60 Specific Gravity Gas)
Nominal
Iron Pipe
Size,
Inches
Internal
Diameter,
Inches
Length of Pipe, Feet
10
32
72
132
278
520
1,050
1,600
3,050
4,800
8,500
17,500
20
22
49
92
190
350
730
1,100
2,100
3,300
5,900
12,000
30
18
40
73
152
285
590
890
1,650
2,700
4,700
9,700
40
15
34
63
130
245
500
760
1,450
2,300
4,100
8,300
50
14
30
56
115
215
440
670
1,270
2,000
3,600
7,400
60
12
27
50
105
195
400
600
1,150
1,850
3,250
6,800
70
11
25
46
96
180
370
560
1,500
1,700
3,000
6,200
80
11
23
43
90
170
350
530
990
1,600
2,800
5,800
90
10
22
40
84
160
320
490
930
1,500
2,600
5,400
100
9
21
38
79
150
305
460
870
1,400
2,500
5,100
125
8
18
34
72
130
275
410
780
1,250
2,200
4,500
150
8
17
31
64
120
250
380
710
1,130
2,000
4,100
175
7
15
28
59
110
225
350
650
1,050
1,850
3,800
200
6
14
26
55
100
210
320
610
980
1,700
3,500
1/4"
3/8"
1/2"
3/4"
1"
1-1/4"
1-1/2"
2"
2-1/2"
3"
4"
.326
.493
.622
.824
1.049
1.380
1.610
2.067
2.469
3.026
4.026
Maximum Capacity of Pipe in Thousands of Btu per Hour of Undiluted Liquefied
Petroleum Gases (at 11 Inches Water Column Inlet Pressure)
(Based on a Pressure Drop of 0.5 Inch Water Column)
Nominal
Iron Pipe
Size,
Inches
Length of Pipe, Feet
10
275
567
1071
2205
3307
6221
20
189
393
732
1496
2299
4331
30
152
315
590
1212
1858
3465
40
129
267
504
1039
1559
2992
50
114
237
448
937
1417
2646
60
103
217
409
834
1275
2394
70
96
196
378
771
1180
2205
80
89
185
346
724
1086
2047
90
83
173
322
677
1023
1921
100
78
162
307
630
967
1811
125
69
146
275
567
866
1606
150
63
132
252
511
787
1498
1/2"
3/4"
1"
1-1/4"
1-1/2"
2"
8
FIGURE 2.7: GAS PIPE SIZING TABLES & EXAMPLE
Example: Boiler Model GB200-4H is to be installed. The distance from the existing gas meter to the installation site is 30
ft. What pipe size must be used? The local utility indicates the heating value of natural gas being supplied is 1000 Btu per
cu.ft. Determine cubic feet of gas per hour for above boiler model:
135,000 Btu per hour
= 135 cu.ft. per hour
1000 Btu per cu.ft.
1. Find 30 ft. in upper portion of the table for natural gas under "Length of Pipe, Feet" heading.
2. Moving down the column, match required capacity. Higher capacity is acceptable. In our case it is 152 cu.ft.
3. Move to left-hand column "Nominal Iron Pipe Size, Inches," to read required pipe size. In our case it is 3/4".
Minimum pressure required at the gas valve inlet is 5" W.C.
for natural gas and 11" W.C. for propane. Maximum pressure
allowable at the gas valve inlet is 12" W.C. If the gas pres-
sure is above these limits, a pressure regulator must be
installed. If the gas pressure is below these limits, contact the
local utility.
Testing Gas Piping
For any pressure testing in excess of 1/2 psi, the boiler and
its individual shutoff valve must be isolated from the piping
system by disconnecting them and capping the outlet(s). For
any pressure testing equal to or less than 1/2 psi, the boiler
must be isolated from the piping system by closing its manu-
al shutoff valve.
DANGER: Before placing gas piping into service,
carefully test it to assure every joint is gas tight. Bub-
ble test all joints with a soap solution. NEVER TEST
WITH AN OPEN FLAME AS FIRE OR EXPLOSION
WILL RESULT.
Содержание GB200 SERIES
Страница 19: ...19...