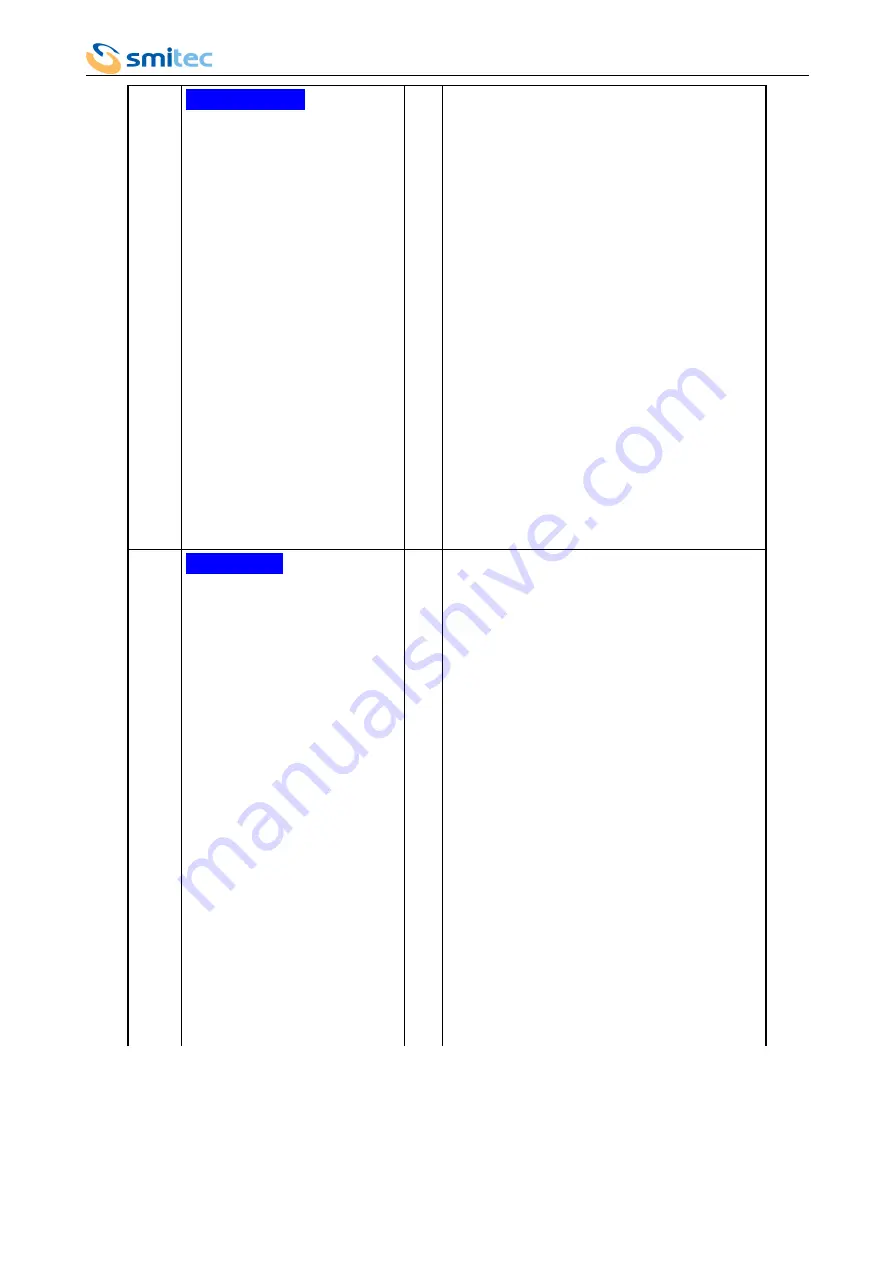
COSMOS DRIVER SERIES 3000 - USE AND MAINTENANCE MANUAL
1.3.6
KPV [A/rpm]
2
Speed proportional gain.
The driver continuously detects the rotor speed and
compares it to the reference speed rate. The
difference between the two values is multiplied by
the proportional gain, in order to determine the
proportional current.
This value of the current is summed up to the
current due to the integrative gain. These two
values determine the motor current.
The higher the difference of speed is, the more the
current in the motor is. Through this process, if it is
continuous, the motor tends to assume the
reference speed, even when the load conditions
applied to the motor change.
The proportional gain must be usually determined
for each specific case, according to the motor
application. This value is strongly influenced by the
inertial mass applied to the motor shaft. The more
the mass is, the lower the gain will be.
In the practical tests, it is necessary to find out the
gain empirically, by progressively increasing the
value, until the motor begins to be unsteady,
depending on the motor noise and vibrations. Once
you reached the limit, decrease the gain by 10–
20%, as a safety margin.
Larger size motors usually show higher values than
smaller size motors.
Min=0.000A/rpm, Max=+3.430A/rpm
1.3.7
KIV [A/G]
2
Speed integrative gain.
The angular difference between the reference and
the rotor is integrated and multiplied by this factor,
in order to determine the integrative current. This
current value is summed up to the current due to
the proportional gain. They altogether determine the
motor current.
If you integrate the angular speed within the time,
you will obtain an angle; as a consequence, it is
possible to express this factor in Ampere per degree;
in fact, if you set a speed rate of 1000 rpm and you
set this value at 1, the current in the motor will
increase by 1 ampere when the rotor slows down
and loses 1 degree.
Thanks to this datum, it is possible to adjust the
rotor speed in a very precise way, with consequent
great advantages, especially for the applications
requiring high stability while running.
Please note that this value is directly proportional to
the proportional gain; therefore, it is not possible to
set an integrative gain without a proportional gain.
This parameter has one negative effect on the
motion, especially at low speed rates: hunting. It is
necessary to find the correct value of integrative
gain, after determining the proportional gain, by
progressively increasing it until the hunting begins.
Once you reached the limit, decrease the gain value
by 10–20%, as a safety margin, as you did for the
proportional gain.
Min=0.0A/Gr, Max=+540.4A/Gr
Ver. 1.07
Pag. 63