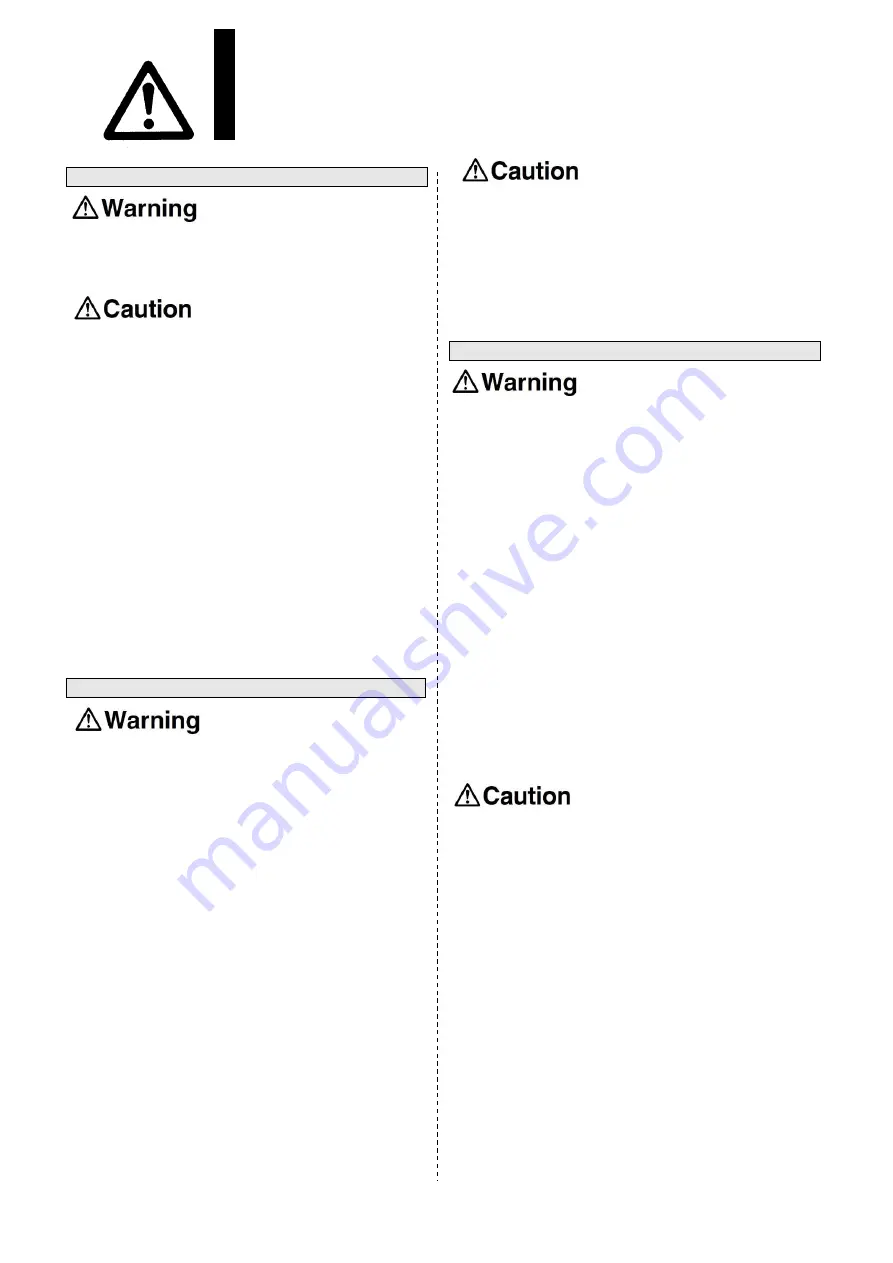
- 6 -
No.VP500-OMZ0005
Air Supply
4. Use clean air.
Do not use compressed air that contains chemicals, synthetic
oils that include organic solvents, salt, corrosive gases, etc., as it
can cause damage or malfunction.
1. When extremely dry air is used as the fluid,
degradation of the lubrication properties inside
the equipment may occur, resulting in reduced
reliability (or reduced service life) of the equipment.
Please consult with SMC.
2. Install an air filter.
Install an air filter upstream near the valve. Select an air filter
with a filtration si
ze of 5 μm or smaller.
3. Take measures to ensure air quality, such as by
installing an aftercooler, air dryer, or water separator.
Compressed air that contains a large amount of drainage can
cause the malfunction of pneumatic equipment, such as valves.
Therefore, take appropriate measures to ensure air quality, such
as by providing an aftercooler, air dryer, or water separator.
4. If an excessive amount of carbon powder is present,
install a mist separator on the upstream side of the
valve.
If excessive carbon dust is generated by the compressor, it may
adhere to the inside of a valve and cause it to malfunction.
For compressed air quality, refer to the SMC Best Pneumatics
catalog.
Operating Environment
1. Do not use in an atmosphere containing corrosive gases,
chemicals, sea water, water, water steam, or where there
is direct contact with any of these.
2. Products with IP65 enclosures (based on IEC60529) are
protected against dust and water.
However, these products cannot be used in water.
3. Products compliant with IP65 satisfy the product
specifications when mounted properly.
Be sure to read the precautions for each product.
4. Do not use in an environment where flammable gas or
explosive gas exists. Usage may cause a fire or
explosion. The products do not have an explosion proof
construction.
5. Do not use in a place subject to heavy vibration and/or
shock.
6. The valve should not be exposed to prolonged sunlight.
Use a protective cover.
7. Remove any sources of excessive heat.
8. If it is used in an environment where there is possible
contact with oil, weld spatter, etc., exercise preventive
measures.
9. When the valve is mounted in a control panel, make sure
the ambient temperature is within the specifications of
the valve.
1. Temperature of ambient environment
Use the valve within the range of the ambient temperature specification
of each valve. In addition, pay attention when using the valve in
environments where the temperature changes drastically.
2. Humidity of ambient environment
•
When using the valve in environments with low humidity, take
measures to prevent static.
•
If the humidity rises, take measures to prevent the adhesion of
water droplets on the valve.
Maintenance
1. Perform maintenance and inspection according to
the procedures indicated in the operation manual.
If handled improperly, human injury and/or malfunction or damage of
machinery and equipment may occur.
2. Removal of equipment, and supply/exhaust of
compressed air
Before components are removed, first confirm that measures are in
place to prevent workpieces from dropping, run-away equipment, etc.
Then, cut off the supply air and electric power, and exhaust all air
pressure from the system using the residual pressure release function.
When the equipment is operated after remounting or replacement, first
confirm that measures are in place to prevent the lurching of actuators,
etc. Then, confirm that the equipment is operating normally.
3. Low-frequency operation
Valves should be operated at least once every 30 days to prevent
malfunction. (Use caution regarding the air supply.)
4. Manual override
When a manual override is operated, connected equipment will
be actuated.
Operate only after safety is confirmed.
5. If the volume of air leakage increases or the valve
does not operate normally, do not use the valve.
Perform periodic maintenance on the valve to confirm
the operating condition and check for any air leakage.
1. Drain flushing
Remove drainage from the air filters regularly.
2. Lubrication
Once lubrication has been started, it must be continued.
Use class 1 turbine oil (with no additives), VG32. If other
lubricant oil is used, it may cause a malfunction. Please contact
SMC for information on the suggested class 2 turbine oil (with
additives), VG32.
3/4/5-Port Solenoid Valves
Precautions 3
Be sure to read this before handling products.