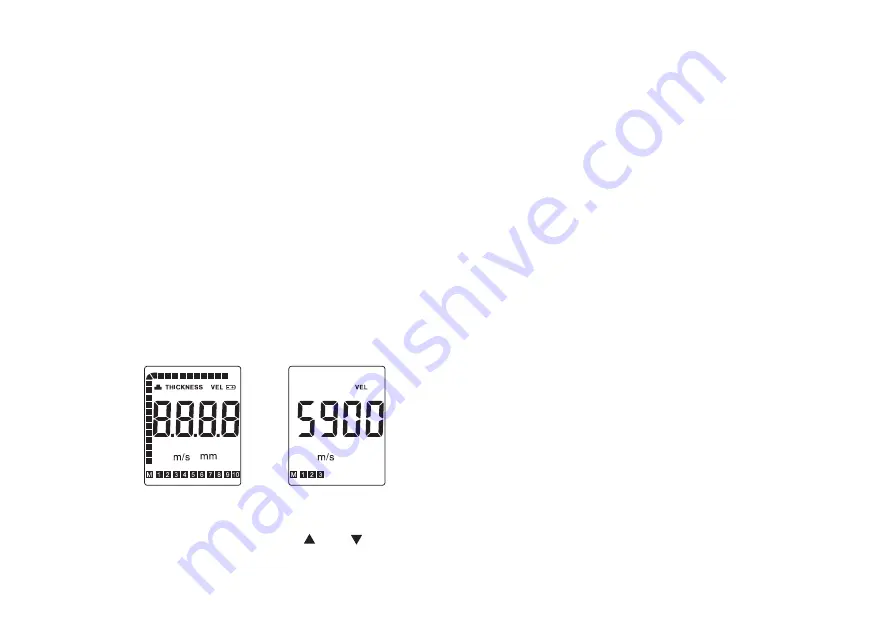
-05-
-10-
2.4 Working temperature condition
Material thickness and sound velocity will change along with tempera-
ture. In normal measurement, environment temperature impact can be
ignored.
The transducer is made of propylene material, considering the protec-
tion of the transducer and its precision we recommend that the surface
temperature of the hardware/workpiece should not over 60
℃
, otherwise
the transducer can not put into use.
Operation temperature: 0~40
℃
Relative humidity: <90%RH
Hardware/workpiece/material temperature: <60
℃
Do not apply in violent vibration / erosive material.
Avoid impact and humidity.
3. Operation procedure:
3.1 Before measurement
(1) Connect the transducer with the main unit, press ON/OFF to turn on,
LCD display full screen for 0.5 second with backlight,then vertical bar
is displayed twice circularly, meanwhile the main display area show
0000 to 9999 progressively.After that, LCD display the last applied
sound velocity with registered memory unit, indicating the gauge is
ready for use.
(2) Sound velocity selected & adjustment
Press “VEL” to enter sound velocity interface, press “VEL” again, you
can select reserved velocity data by pressing “ ” or “ ” with the
word “VEL” blinking on LCD ; If you need to adjust sound velocity data,
Full screen
Last applied sound velocity
& registered unit
The standard of selecting the angle between the crosstalk segregating
board of the transducer and axis of the measured part is up to material
curvature. For bigger pipe diameters, choose vertical orientation between
the crosstalk segregating board of the transducer and axis of the measured
pipe, and for the smaller ones, two measurement should be performed, one
with the axis of pipe perpendicular, another is parallel, and the smaller of
two displayed values should then be taken as the thickness at that point.
4.5 Complex shape material
For complex shape material measurement, please refer to the 4.4,
the smaller of the two reading should then be taken as the thickness.
4.6 Non-parallel surface
To get a satisfying ultrasonic response, the surface must have its one
measuring side parallel with another, otherwise will obtain wrong result.
4.7 Influence of the material temperature
The size & sound velocity of material will change with the temperature,
when the precision is critical, please make measurement in 2 samples
of the material under the same temperature to determine the proper
reading resulting from the temperature. When taking measurement
for steel parts in high temperature, this method may be adopted to
obtain the correct reading.
4.8 High acoustic reduction material
For materials in fiber, poriferous or big granular, acoustic dispersion
will cause the energy attenuation that may result in abnormal readings
(practically the reading less than the actual thickness), in this case, the
material is not suitable for the gauge.
4.9 Reference sample block
For calibration for the gauge, a given thickness or sound velocity of
the material is very import. Calibration needs at lest one referring stan-
dard sample block. This gauge is provided with a 4.0mm sample block
on the front cabinet, please see for calibration operations.
In different material & situation, only one sample block may not
satisfy every calibration. The more similar sample block, the more exact
reading obtained. Ideally, referring block is a group of different thickness
and same material, by calibrating to the referring block, the effect of var-
iation of sound velocity will be minimized. To get the most exact measure,
a set of referring block is very important.
Содержание Model AS850
Страница 1: ...Ultrasonic Thickness Gauge Instruction Manual Model AS850 ...
Страница 2: ......