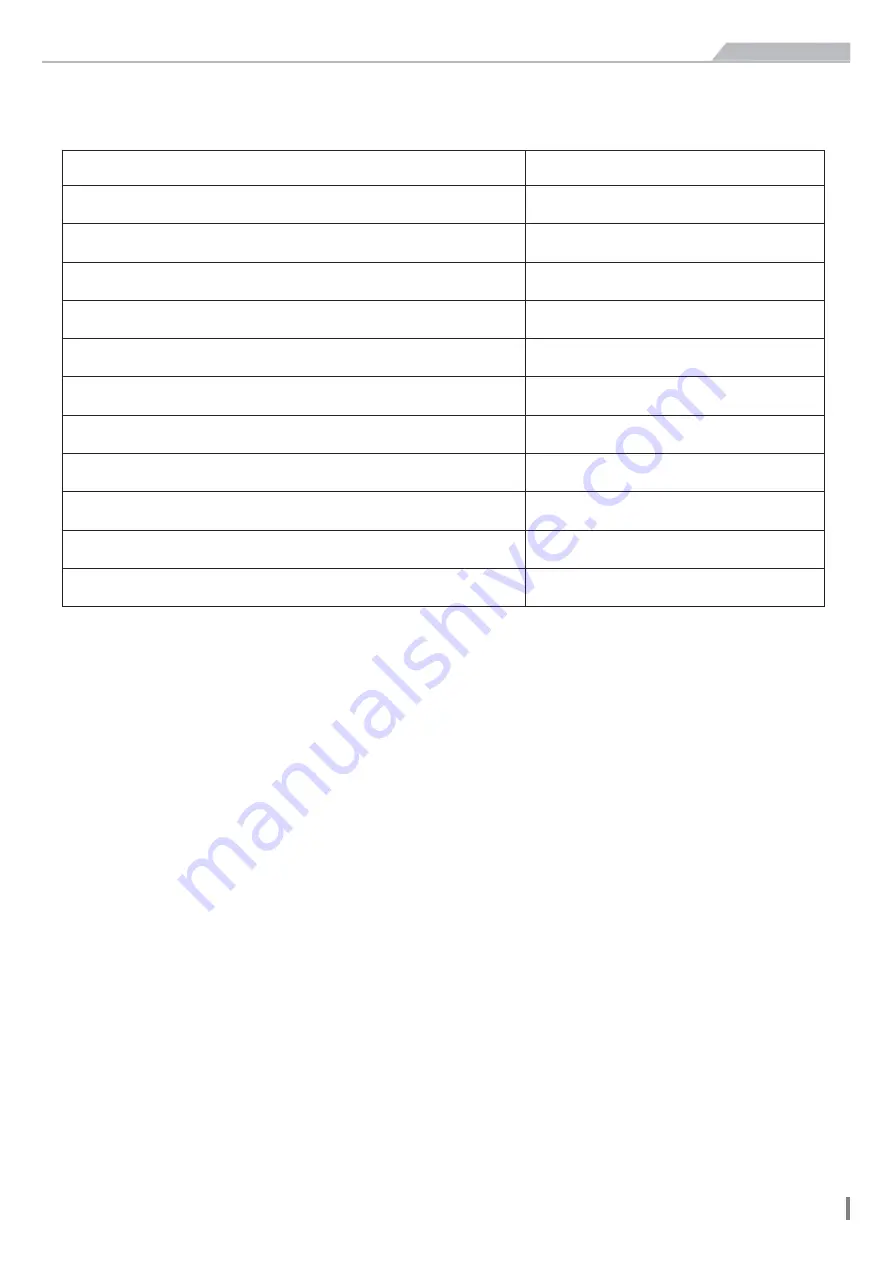
31
Installation Manual
Installation Manual
6.3 Check after installation
Check according to the following requirement after
fi
nishing installation.
Items to be checked
Possible malfunction
Has the unit been installed
fi
rmly?
The unit may drop, shake or emit noise
Have you done the refrigerant leakage test?
It may cause in suf
fi
cient cooling(heating)
capacity.
Is heat insulation of pipeline suf
fi
cient?
It may cause condensation and water dripping.
Is water drained well?
It may cause condensation and water dripping.
Is the voltage of power supply according to the voltage marked on the
nameplate?
It may cause malfunction or damaging the parts.
Is electric wiring and pipeline installed correctly?
It may cause malfunction or damaging the parts.
Is the unit grounded securely?
It may cause electric leakage
Does the power cord follow the speci
fi
cation?
It may cause malfunction or damaging the parts.
Is there any obstruction in the air inlet and outlet?
It may cause in sufficient cooling(heating)
capacity.
The dust and sundries caused during installation are removed?
It may cause malfunction or damaging the parts.
The gas valve and liquid valve of connection pipe are open completely?
It may cause in sufficient cooling(heating)
capacity.
6.4 Test operation
1. Preparation of test operation
●
The client approves the air conditioner.
●
Specify the important notes for air conditioner to the client.
2. Method of test operation
●
Put through the power, press ON/OFF button on the remote controller to start operation.
●
Press MODE button to select AUTO, COOL, DRY, FAN and HEATto check whether the operation is normal or not.
●
If the ambient temperature is lower than 16
℃
, the air conditioner can’t start cooling.
Содержание SUV2-H18/3CFA-N
Страница 3: ...Summary and Features Outdoor Unit 18K 24K 28K ...
Страница 4: ...36K 42K ...
Страница 20: ...16 Construction Views Construction Views 24K 28K Unit mm 920 990 790 394 370 426 610 ...
Страница 21: ...17 Construction Views Construction Views 36K 42K Unit mm 950 1020 997 368 340 396 590 ...
Страница 23: ...19 Schematic Diagram Schematic Diagram SUV2 H18 1CFA N 24K ...
Страница 42: ...38 Troubleshooting Troubleshooting Model 28K ...
Страница 44: ...40 Troubleshooting Troubleshooting Model 36K ...
Страница 47: ...43 Troubleshooting Troubleshooting Model 42K ...