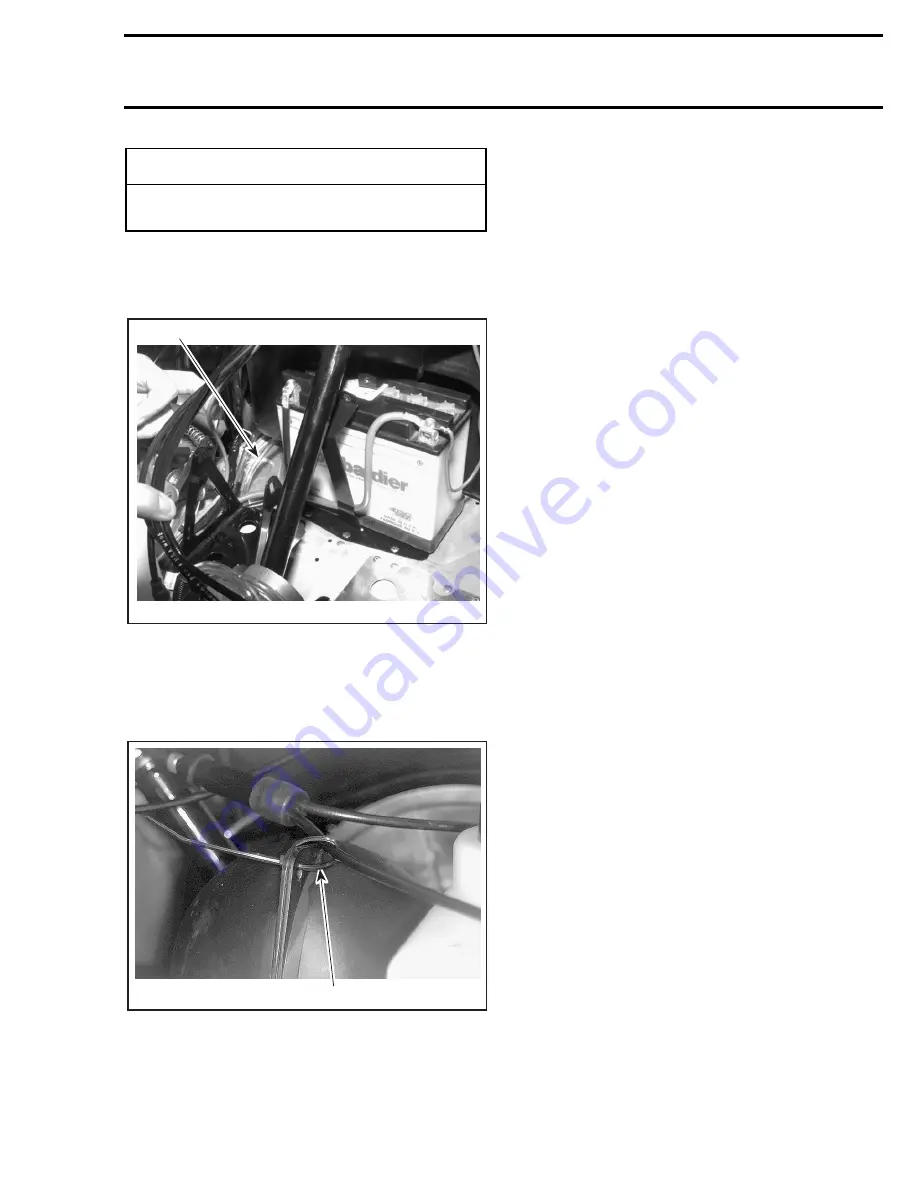
Section 05
ELECTRICAL
Sub-Section 05
(BATTERY)
05-05-9
Apply silicone dielectric grease (P/N 413 7017 00)
on battery posts and connectors.
S-Series
BATTERY CONNECTION — S-SERIES
1. Vent tube on fitting
Skandic WT/SWT/WT LC
See photos in removal procedures for proper bat-
tery installation.
AIR SILENCER INSTALLATION — SKANDIC WT
1. Locking tie
All Models
Ensure that vent tube is not kinked or blocked
then install protective boot over battery.
Close and fasten retaining strips.
Reinstall air silencer.
Fasten spark plug cables to fan housing.
Reinstall throttle cable to air silencer. See removal
illustration.
-
CAUTION
Negative battery terminal should always be
disconnected FIRST and reconnected LAST.
A03H1SA
1
A22C0BA
1
Содержание FORMULA S 1997
Страница 1: ......
Страница 284: ...TUNDRA II LT ANNEX 1 mmr9737a fm5 Page 2 Thursday May 8 1997 4 37 PM...
Страница 285: ......
Страница 286: ......
Страница 287: ...FORMULA S SL SKANDIC 380 500 ANNEX 2 mmr9737a fm5 Page 4 Thursday May 8 1997 4 37 PM...
Страница 288: ......
Страница 289: ......
Страница 290: ...TOURING E E LT TOURING LE SLE ANNEX 3 mmr9737a fm5 Page 6 Thursday May 8 1997 4 37 PM...
Страница 291: ......
Страница 292: ......
Страница 293: ......
Страница 428: ...Section 03 ENGINE Sub Section 11 CARBURETOR AND FUEL PUMP 03 11 9 HAC SYSTEM A03I0BS To magneto housing FLAT RATE PARTS...
Страница 560: ...Section 06 REAR SUSPENSION Sub Section 04 DRIVE AXLE 06 04 2 Skandic WT A22D14S 13 6 9 3 2 5 4 FLAT RATE PARTS...
Страница 585: ...Section 07 STEERING FRONT SUSPENSION Sub Section 03 SUSPENSION AND SKI SYSTEM 07 03 4 WRONG POSITION A06G0XA...
Страница 615: ......
Страница 616: ......
Страница 619: ......
Страница 620: ......
Страница 623: ......
Страница 624: ......
Страница 627: ......
Страница 628: ......
Страница 631: ......
Страница 632: ......
Страница 635: ......
Страница 636: ......
Страница 639: ...ANNEX 7...
Страница 640: ...ANNEX 7...
Страница 641: ...SKANDIC WT LC ANNEX 8...
Страница 644: ......
Страница 645: ...I 1997 Shop Manual VOLUME 3 FORMULA III III LT MACH 1 Z Z LT...
Страница 748: ...Section 03 ENGINE Sub Section 08 CARBURETOR AND FUEL PUMP 03 08 14 FUEL PUMP All Models A06C3SS...
Страница 859: ......
Страница 860: ......
Страница 861: ......
Страница 862: ......
Страница 863: ...I 7 1997 Shop Manual Supplement GRAND TOURING SE...
Страница 896: ...08 2 Section 08 WIRING DIAGRAM GAUGES A06H2YA...
Страница 900: ......
Страница 901: ......
Страница 902: ......
Страница 903: ......
Страница 904: ......
Страница 905: ......
Страница 906: ......
Страница 910: ...SHOP MANUAL SUPPLEMENT MX Zx 440 LC PAGE 5 OF 18 LIQUID COOLING SYSTEM A15C2IS 1 2 PARTS...
Страница 924: ...MX Zx 440 LC ANNEX 1...
Страница 925: ......
Страница 926: ......