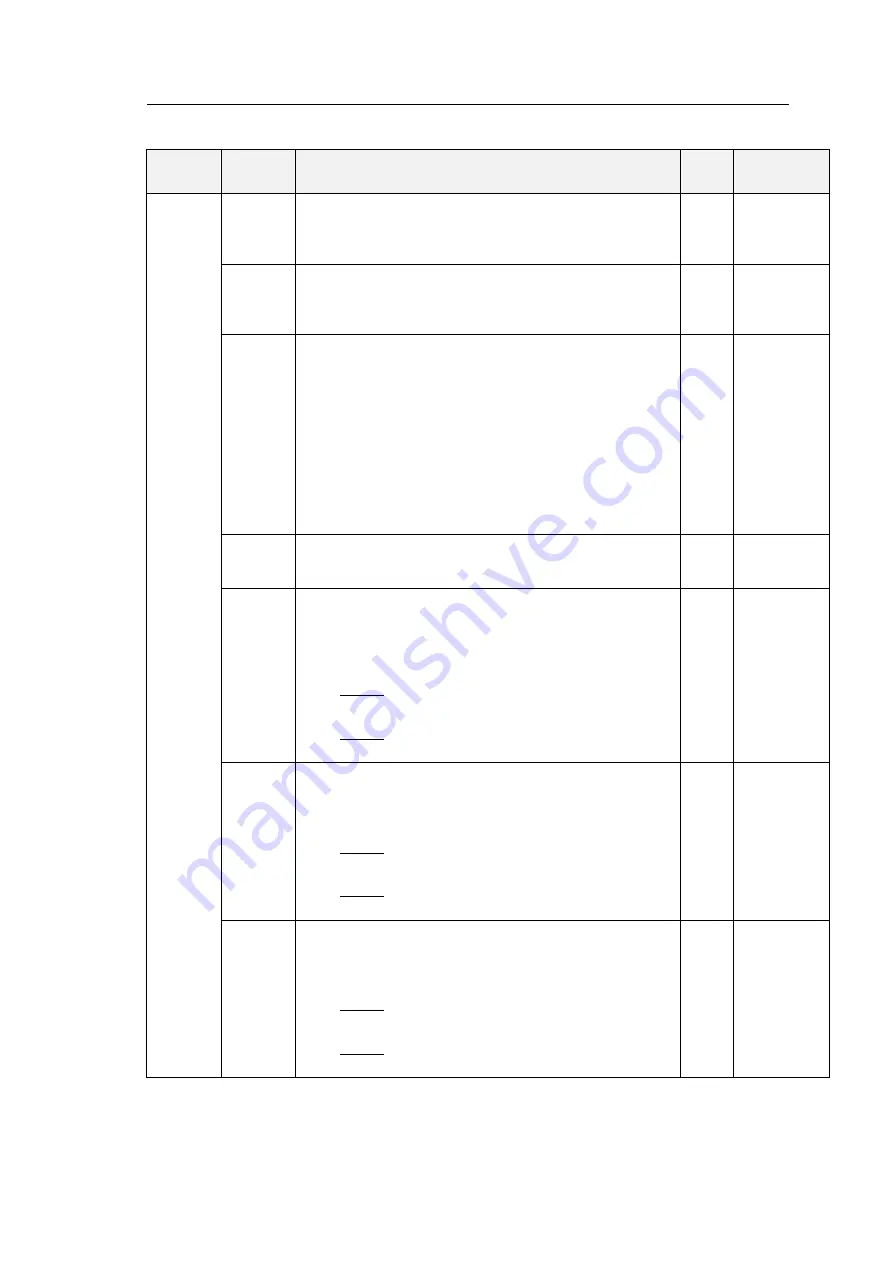
Simrad GC80/GC85 Compact Gyro Compass
60
20221511 / D
Main
Category
Sub
Category
Parameter/description
Default
value
Range
A-1 cont.
1.5.L (
φ
) Phi offset (°)
Offset value (°) around the vertical axis of gyro sphere
(rotor axis) and the sensitive element.
0.00
-3.00 – 3.00
1.6.t (
θ
) Theta offset (°)
Offset value (°) around the horizontal axis of gyro
sphere (rotor axis) and the sensitive element.
0.00
-3.00 – 3.00
1.7.G
X signal pickup gain (v/°)
Distance of the sensitive element share and the rotor
axis direction. Inclination angle around horizontal axis
is obtained equivalently by monitoring this signal. For
example, when north side of the rotor axis rises, the
sensitive element follows to rise its north side, then
gyro sphere suspended by the suspension wire moves to
south side. X signal represents this amount of
movement (v/°).
This parameter is only used for GC85.
2.32
0.00 – 5.00
1.8.c Ks/H
Suspension wire twist torque. Fixed value.
1.477 1.000 – 2.000
1.9.r
Maximum rate of turn (°/sec)
Maximum rate of turn in the turn rates which the
bearing servo system followed up to this moment
(°/sec).
NOTE: The maximum is measured after 3 hours from
system start.
NOTE: Reset this data certainly after completion of
installation!
0.00 -
1.A.F
Maximum deviation of bearing servo (°)
Maximum deviation value in the bearing servo loop that
occurred up to this moment (°).
NOTE: The maximum is measured after 3 hours from
system start.
NOTE: Reset this data certainly after completion of
installation!
0.00 -
1.b.S
Maximum deviation of horizontal servo (°)
Maximum deviation value in the horizontal servo loop
that occurred up to this moment (°).
NOTE: The maximum is measured after 3 hours from
system start.
NOTE: Reset this data certainly after completion of
installation!
0.00 -
Содержание 000-15567-001
Страница 1: ...INSTRUCTION MANUAL SIMRAD GC80 85 COMPACT Gyro Compass 20221511D English ...
Страница 16: ...Simrad GC80 GC85 Compact Gyro Compass 8 20221511 D THIS PAGE INTENTIONALLY LEFT BLANK ...
Страница 30: ...Simrad GC80 GC85 Compact Gyro Compass 22 20221511 D THIS PAGE INTENTIONALLY LEFT BLANK ...
Страница 64: ...Simrad GC80 GC85 Compact Gyro Compass 56 20221511 D THIS PAGE INTENTIONALLY LEFT BLANK ...
Страница 72: ...Simrad GC80 GC85 Compact Gyro Compass 64 20221511 D THIS PAGE INTENTIONALLY LEFT BLANK ...
Страница 84: ...Simrad GC80 GC85 Compact Gyro Compass 76 20221511 D ...
Страница 90: ...Simrad GC80 GC85 Compact Gyro Compass 82 20221511 D THIS PAGE INTENTIONALLY LEFT BLANK ...
Страница 96: ...Simrad GC80 GC85 Compact Gyro Compass 88 20221511 D THIS PAGE INTENTIONALLY LEFT BLANK ...