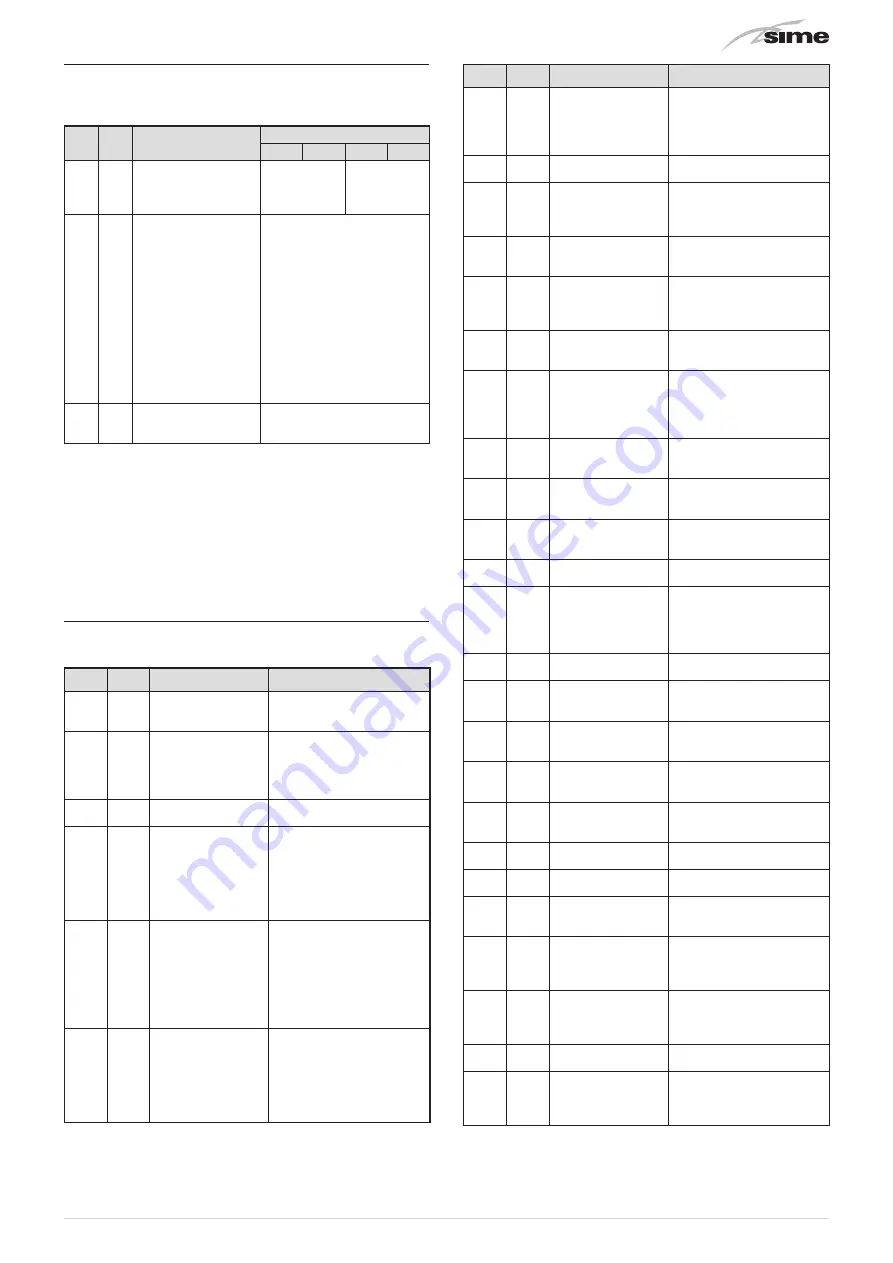
39
10.5 Unscheduled maintenance
If replacing the
electronic board
, the user MUST set the
parameters as indicated in the table.
Type No. Description
Setting for
Brava Slim HE R
20 R i 20 R e 40 R i 40 R e
PAR
01
Index showing boiler
power in kW
1 = 20; 2 = 30; 3 = 35;
4 = 40
1
4
PAR
02
Hydraulic
configuration
0 = rapid
1 = storage tank with
thermostat or heating
only
2 = hot water tank with
sensor
3 = bithermic
4=instant with solar
power input
5 = open vent
6 = boiler with heat
pump
1
PAR
03
Gas Type Configuration
0 = NATURAL GAS; 1 =
UNIVERSAL LPG
0 or 1
To enter "
"refer to the indications
provided in the specific section.
Once the parameters in the table have been set, you must carry
out the entire phase of "
" described
in the specific section.
If the
gas valve
and/or the
ignition/detection electrode
, and/or the
burner
, and/or the
fan
are replaced, the user must still carry out
the entire phase of "
" described in
the specific section.
10.6 Possible faults and solutions
LIST OF MALFUNCTION/FAULT ALARMS
Type
No.
Fault
Solution
ALL
02
Low water pressure
in system
- Restore pressure
- Check for any leaks in the
system
ALL
03
High water pressure
in system
- Empty the system via the
drain valve on the hydraulic
assembly and bring the
pressure to approximately
1.2 bar (120 kPa)
ALL
05
Delivery sensor fault - Check connections
- Replace the sensor
ALL
06
No flame detection
- Check the integrity of the
electrode and check that it
is not grounded
- Check gas availability and
pressure
- Check the integrity of the
gas valve and the card
ALL
07
Sensor or safety
thermostat
intervenes
- Check the sensor or
thermostat connections
- Deaerate the system
- Check the bleed valve
- Replace the sensor or the
thermostat
- Check that the pump
impeller is not blocked
ALL
08
Fault in the flame
detection circuit
- Check the integrity of the
electrode and check that it
is not grounded
- Check gas availability and
pressure
- Check the integrity of the
gas valve and the card
Type
No.
Fault
Solution
ALL
09
No water circulating
in the system
- Check the rotation of the
pump rotor
- Check the electrical
connections
- Replace the pump
ALL
11
Gas valve modulator
disconnected
- Check the electrical
connection
ALL
12
Incorrect
configuration of
the open /sealed
chamber
- Set the parameter PAR 04
(Combustion configuration)
to 0
ALL
13
Smoke probe
intervention
- Replace the smoke probe
- Contact the Technical
Assistance Centre
ALL
14
Smoke probe fault
- Replace the smoke probe
- Check the electrical
connection of the smoke
probe
ALL
15
Fan check cable
disconnected
- Check the connection cable
between the fan and the
board
ALL
18
Condensate level
fault
- Check for any clogging in
the pipe which takes the
condensate to the siphon
- Check that the siphon is not
clogged
ALL
28
Maximum number of
consecutive resets
reached
- Contact the Technical
Assistance Centre
ALL
30
Return sensor (SR)
fault
- Replace the return probe
- Contact the Technical
Assistance Centre
ALL
37
Fault due to low
network voltage.
- Check with tester
- Contact network provider
(ENEL)
ALL
40
Incorrect network
frequency detected
- Contact network provider
(ENEL)
ALL
41
Flame loss more
than 6 consecutive
times
- Check the detection
electrode
- Check the gas supply (open
valve)
- Check mains gas pressure
ALL
42
Button fault
- Check that buttons are
working
ALL
43
Open Therm
communication fault
- Check the electrical
connection of the remote
control
ALL
62
Self-calibrating
procedure is required
- Carry out the self-
calibrating procedure (see
the specific section)
ALL
72
Incorrect positioning
of the delivery sensor
- Check that the delivery
sensor is attached to the
delivery pipe
ALL
77
EV2 SGV current
max/min absolute
limits error
- Contact the Technical
Assistance Centre
ALL
78
EV2 SGV current
upper limit error
- Contact the Technical
Assistance Centre
ALL
79
EV2 SGV current
lower limit error
- Contact the Technical
Assistance Centre
ALL
80
Fault on the valve
control logic line/
valve cable damaged
- Check the valve cable
- Contact the Technical
Assistance Centre
ALL
81
Block due to
combustion during
start-up
- Check for blockage in
chimney
- Bleed the air from the gas
circuit
ALL
82
Block due to
numerous
combustion control
failures
- Check electrode
- Check outlets
ALL
83
Irregular combustion
(temporary error)
- Check for blockage in
chimney
ALL
84
Flow rate reduced
for (presumed) low
pressure on mains
gas
- Check gas flow rate
Содержание Brava Slim HE 20 R i
Страница 4: ...4 ...
Страница 42: ...42 12 EXPLODED VIEWS Brava Slim HE 20 R i Brava Slim HE 40 R i ...
Страница 43: ...43 Brava Slim HE 20 R e Brava Slim HE 40 R e ...
Страница 44: ...44 Brava Slim HE 20 R i Brava Slim HE 20 R e Brava Slim HE 40 R i Brava Slim HE 40 R e ...
Страница 45: ...45 Brava Slim HE 20 R i Brava Slim HE 20 R e Brava Slim HE 40 R i Brava Slim HE 40 R e ...
Страница 46: ...46 Brava Slim HE 20 R i Brava Slim HE 20 R e Brava Slim HE 40 R i Brava Slim HE 40 R e ...
Страница 55: ...55 ...