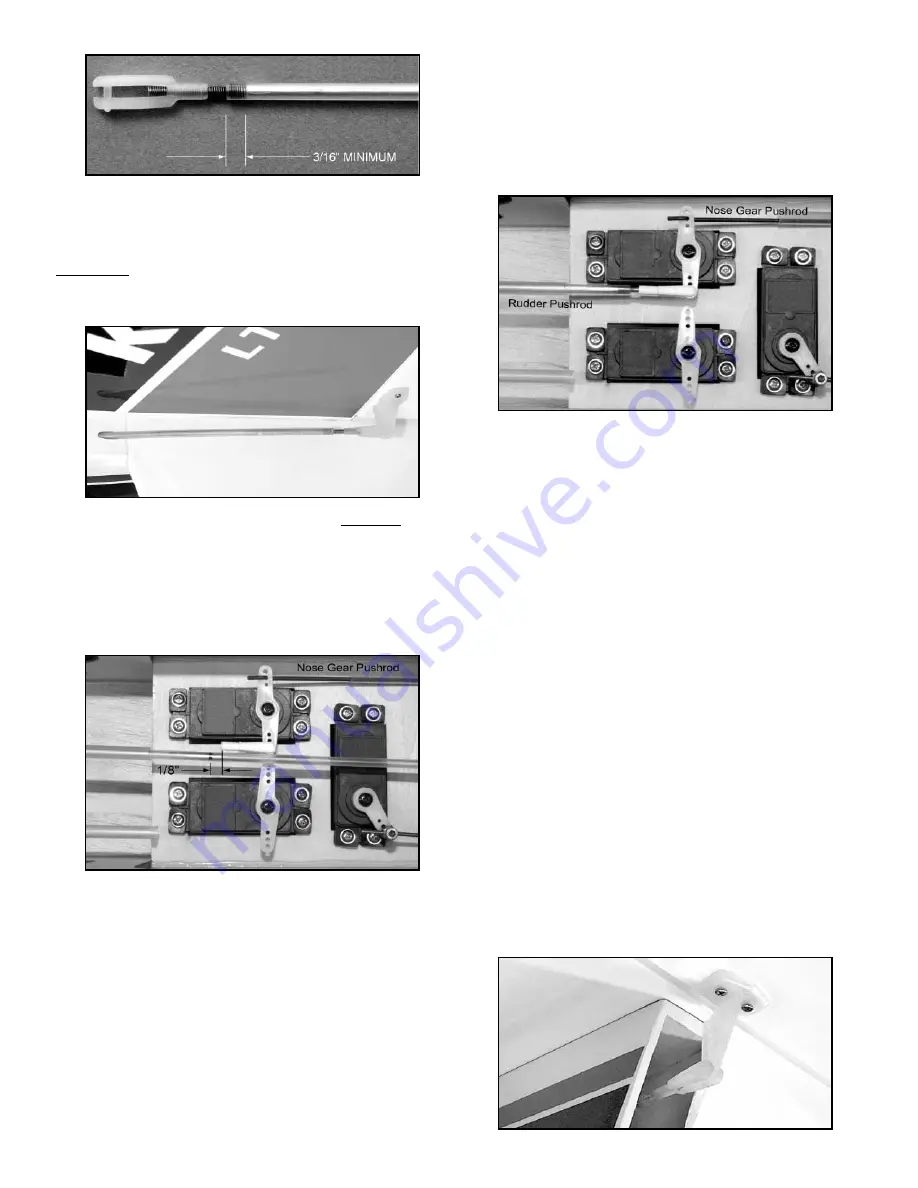
7) From the tail end of the airplane, slide the rudder pushrod
inside the pushrod sleeve that is already in the fuselage. Slide it in
until the nylon R/C Link is even with the rudder control horn. Pry
open the R/C link and clip it into the outermost hole of the rudder
control horn. Now reach into the fuselage and try operating the
rudder from the servo end of the pushrod. It should work smooth
and easy. If not, figure out why and fix it now before proceeding.
8) a) Now clip another R/C Link into the rudder servo arm - on the
side of the servo opposite the nose gear pushrod.
b) Set the rudder in neutral position.
c) Mark the inner pushrod tube exactly 1/8" from the end of the
R/C Link.
d) Unhook the R/C Link from the rudder horn and slide the
pushrod tube back out of the airplane. Cut off the tube at the mark
just made, using a sharp razor blade or modeling knife.
9) Cut a 10" Threaded Steel Rod to 7" overall length. Coat the
plain portion of the 7” rod with a very thin layer of epoxy glue.
Immediately slide the plain end of the rod inside the servo end of
the rudder pushrod tube. Screw at least 3/16" of threads into the
tubing. Wipe off any excess epoxy glue and let dry.
10) Slide the rudder pushrod back inside the sleeve in the fuselage
and clip the rear R/C Link back onto the elevator horn. At the
servor end of the pushrod, screw a nylon R/C link halfway onto the
exposed threads of the steel rod. Then clip that R/C link into the
rudder servo arm.
11) Plug the rudder servo into the receiver and test the operation
of the rudder. If you sense any binding in the rudder movement,
find the cause and fix it now. With full right and left movement of
the transmitter's rudder control stick, the rudder should move
approximately 1" right and 1" left.
NOTE: If you are not getting the correct amount of rudder travel, try
using your transmitter’s “End Point Adjustment” feature to dial in
the proper amount. Also fine tune the overall length of the rudder
pushrod, by screwing one or both of the nylon R/C Links further in
or out, until the rudder is neutral when the transmitter is neutral.
ELEVATOR PUSHROD
Locate the following parts from the kit contents:
❑
(1) Nylon Control Horn
❑
(1) Nylon Control Horn Retainer
❑
(2) M2 x 12mm Bolts, for control horn
❑
(1) 1/8” O.D. x 38” Nylon Pushrod Tube
❑
(2) 2-56 x 10” Threaded Rods
❑
(2) Nylon R/C Links
1) Mount a Nylon Control Horn on the bottom of the Elevator using
two M2 x 12mm Bolts. Make sure the Elevator Horn is in the
center of the tail opening so that the R/C link won't hit the fuse
sides.
2) Cut another 10" Threaded Steel Rod to 7" overall length. Coat
all of the plain portion of the 7” rod with a very thin layer of epoxy
glue, and then proceed immediately to the next step before the
glue dries.
3) Slide the glue coated end of the 7" long threaded rod inside the
1/8” O.D. x 38” Nylon Pushrod Tube, all the way up to the beginning
of the threads. Then screw at least 3/16" of threads inside the
tubing. Wipe off any excess epoxy glue. After the glue dries, screw
a nylon R/C link halfway onto the exposed threads of the steel rod.
4) Slide the elevator pushrod inside the pushrod sleeve that is
already in the fuselage. Slide it in until the nylon R/C Link can be
snapped into the bottom hole of the elevator control horn. Then
reach into the fuselage and try operating the elevator from the
servo end of the pushrod. It should work smooth and easy. If not,
figure out why and fix it now before proceeding.
20