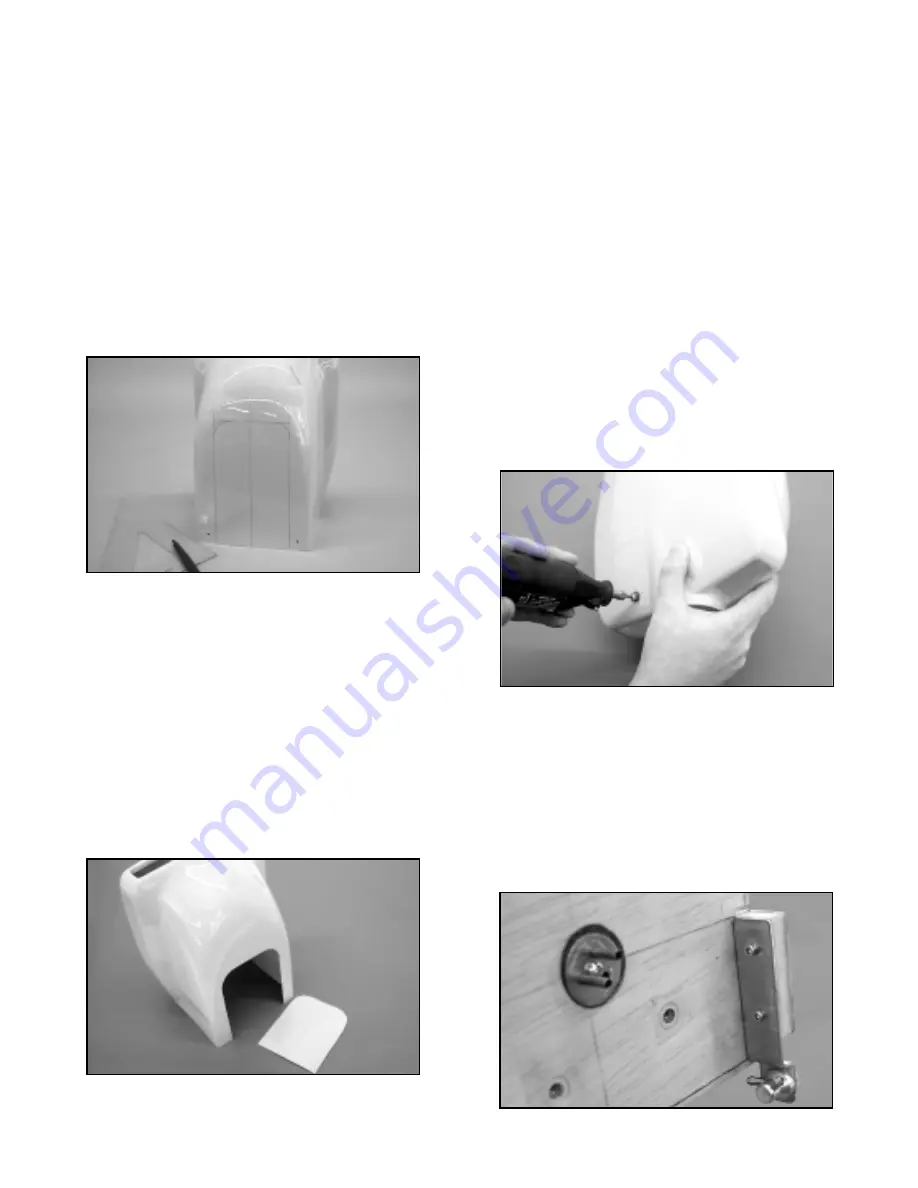
cowl, approximately 3-1/4" in from the outer edge. Stand
the triangle up against the bottom edge of the cowl, aligned
with the mark just made. Use the felt marker to draw a
vertical line up toward the nose about 8" long. Measuring
from this centerline, make a mark at 2-1/16" to the left of the
centerline and another at 2-1/16" to the right of the
centerline.
Again using the triangle and the marks just
made, draw a straight vertical lines on the cowl from the
bottom edge up towards the nose, again about 8" long.
These two outer lines should parallel the centerline.
Measure 7" up from the back edge of the cowl, making
a mark at one of the outer vertical lines.
Repeat this
measurement and mark on the other outer vertical line. Use
a straightedge and marker pen to connect these two marks.
This gives you the area to be cut out from the bottom of the
cowl. To avoid sharp corners and for a better look, we
suggest using a circle guide to round the two upper corners
of this cut out area.
The fiberglass can be cut from the cowl easily, using a
Dremel® Tool and a large cut-off wheel. Before cutting out
the cowl opening be sure to wear safety glasses and a
mask of some kind to avoid inhaling any fiberglass dust.
Carefully cut the fiberglass, using the lines previously
drawn. If you are careful, you will find that you can get
fairly close to the lines with the cut-off wheel. The goal is to
remove most of the material within the lines.
Once the
piece is cut and removed, exchange the cut-off wheel for a
sanding drum bit in your Dremel® Tool.
Use the drum
sander bit to round the upper two corners and to lightly
clean up any jagged edges. Use 220 sandpaper to clean
up the edges of the cutout, without sanding the paint. Make
sure the edges are uniform and free of any loose glass.
Remove all fiberglass dust from the cowl with alcohol and a
clean cloth.
❑
9) Mount the now trimmed cowl back onto the fuselage, over
your engine. In this step you will determine the location for
the hole required for your engine's needle valve to exit the
cowl. This is easiest done using the penlight mentioned
earlier in step #1 and fine line marker pen. First find the
approximate location of where the needle valve will exit by
looking carefully at your engine's carburetor.
Mark that
location onto the cowl.
Now look a little closer and use the penlight to adjust the
mark just made from the outside of the cowl. Reposition the
mark as required to get as close as possible to the actual
exit location.
Use the Dremel® Tool and a small tipped
grinding bit to make a small hole (maybe 1/16" in diameter)
in the cowl, at the exit mark just made. Chances are that
you were quite close to the actual exit point. Stick a piece
of music wire into the hole, down to the needle valve hole in
the carburetor. Carefully observe if the hole needs to be
repositioned to straighten up the wire, as if it were the
needle valve. Make another mark on the cowl and again
use the Dremel® Tool to open the hole just a little towards
the correct position. In this manner, continue checking and
adjusting the exit hole until it aligns perfectly with the
carburetor/needle valve position.
Use the Dremel® Tool
and tapered bit to open the hole enough to insert and install
the needle valve in the carb. Be sure the hole has at least
3/32" clearance around the needle valve to avoid contact.
❑
10) You must be able to fuel and de-fuel your CAP
conveniently.
There are several commercially available
fueling systems that would work with this model. We have
used and highly recommend the Du-Bro #334 Kwik-Fill
Fueling Valve for glow engines. In this optional step, we will
explain how we mounted our fuel valve. All that's required
is to make a simple aluminum bracket, mount it to the
firewall area and make a small hole in the cowl to accept the
fuel probe. We mounted our filler bracket on the inside face
of the left hardwood protrusion on the left edge of the
firewall. In order to meet the cowl as closely as possible but
10
Содержание CAP 231EX
Страница 26: ......