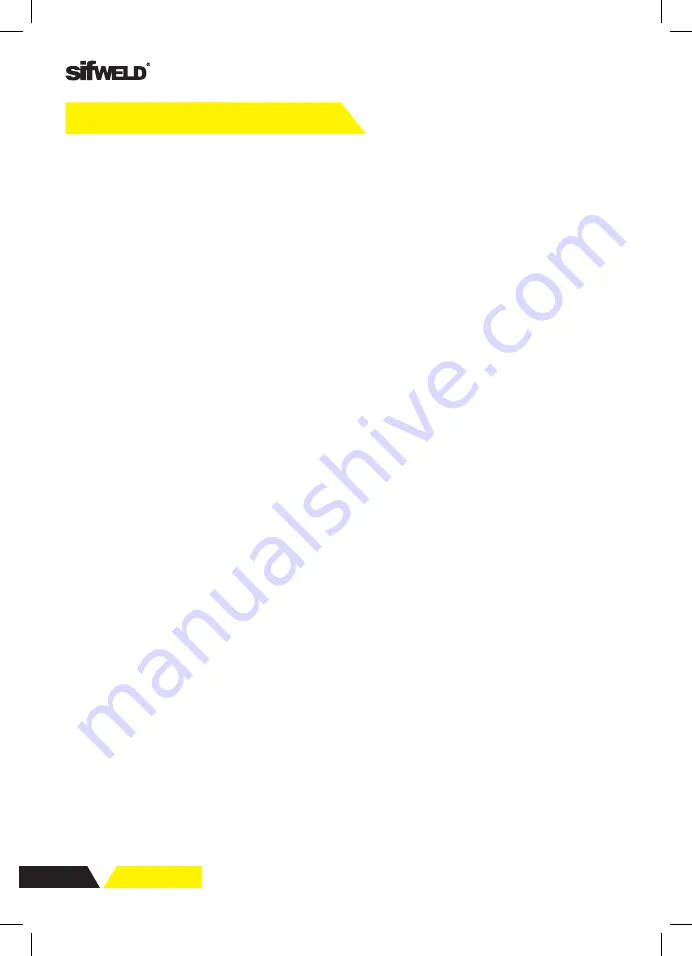
32
3.6 MIG Torch liner Types
MIG Torch Liners
The liner is both one of the simplest and most important components of a MIG gun. Its sole purpose is
to guide the welding wire from the wire feeder, through the gun cable and up to the contact tip.
Steel Liners
Most MIG gun liners are made from coiled steel wire also known as piano wire, which provides the liner
with good rigidity and flexibility and allows it to guide the welding wire smoothly through the welding
cable as it bends and flex during operational use. Steel liners are primarily used for feeding of solid steel
wire, other wires such as Aluminum, Silicon Bronze, Etc. will perform better using a Teflon or Polyamide
line. The internal diameter of the liner is important and relative to the wire diameter being used. The
correct inside diameter and will assist in smooth feeding and prevention of the wire kinking and bird-
nesting at the drive rollers. Also bending the cable too tightly during welding increases the friction
between the liner and the welding wire making it more difficult to push the wire through the liner
resulting in poor wire feeding, premature liner wear and bird-nesting. Dust, grime and metal particles
can accumulate inside the liner over time and cause friction and blockages, it is recommended to
periodically blow out the liner with compressed air. Small diameter welding wires, 0.6mm through
1.0mm have relatively low columnar strength, and if matched with an oversized liner, can cause the wire
to wander or drift within the liner. This in turn leads to poor wire feeding and premature liner failure due
to excessive wear. By contrast, larger diameter welding wires, 1.2mm through 2.4mm have much higher
columnar strength but it is important to make sure the liner has enough internal diameter clearance.
Most manufacturers will produce liners sized to match wire diameters and length of welding torch cable
and most are color coded to suit.
Teflon and Polyamide (PA) Liners
Teflon liners are well suited for feeding soft wires with poor column strength like aluminum wires. The
interiors of these liners are smooth and provide stable feeding, especially on small diameter welding
wire Teflon can be good for higher heat applications that utilize water-cooled torches and brass neck
liners. Teflon has good abrasion resistance characteristics and can be used with a variety of wire types
such as silicon bronze, stainless steel as well as aluminum. A note of caution to carefully inspect the end
of the welding wire prior to feeding it down the liner. Sharp edges and burrs can score the inside of the
liner and lead to blockages and accelerated wear. Polyamide Liners (PA) are made of carbon infused
nylon and are ideal for softer aluminum, copper alloy welding wires and push pull torch applications.
These liners are generally fitted with a floating collet to allow the liner to be inserted all the way to the
feed rollers.
Copper - Brass Neck Liners
For high heat applications fitting brass or copper wound jumper or neck liner on the end of the liner
at the neck end will increase the working temperature of the liner as well as improve the electrical
conductivity of the welding power transfer to the wire. It is recommended for all Aluminum and Silicone
Bronze welding applications.
Содержание Evolution MTS400 SYN
Страница 39: ...39 Notes ...