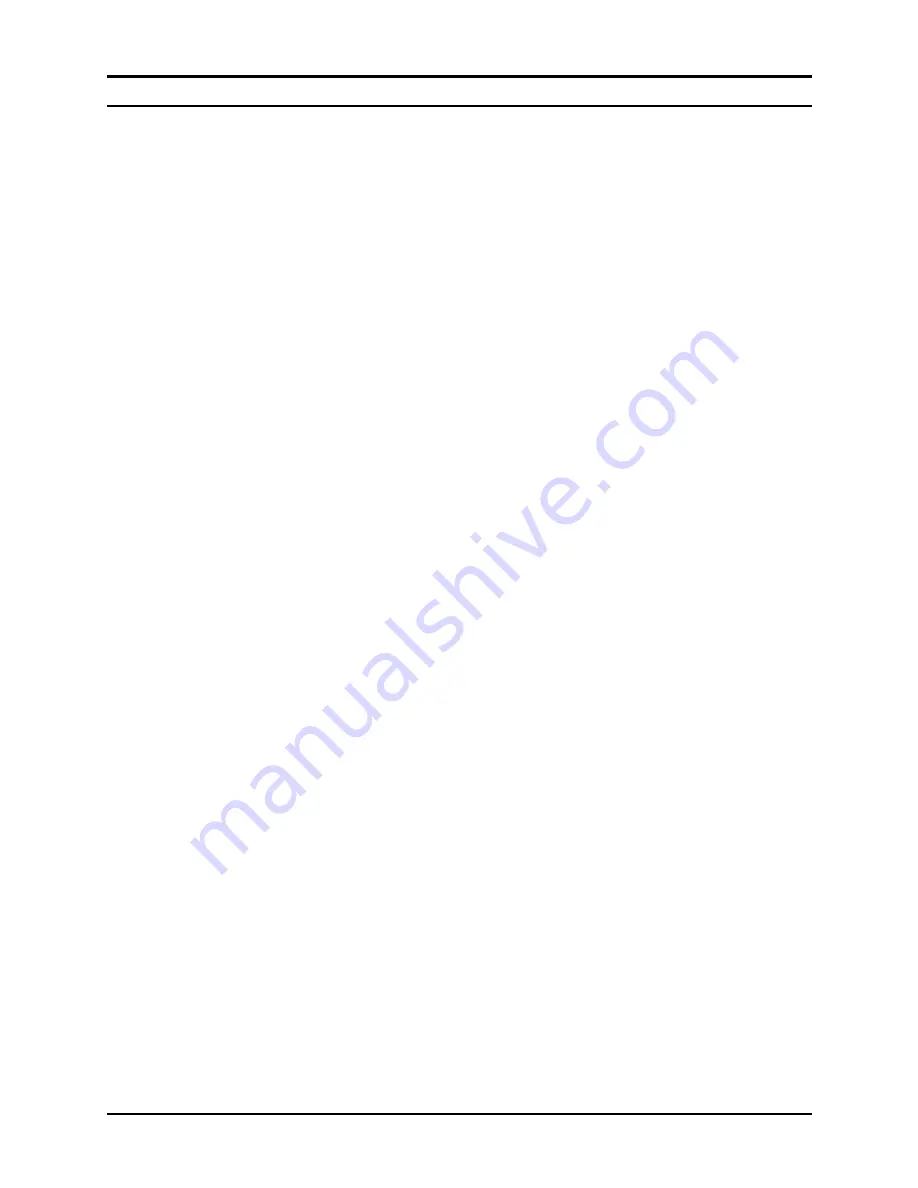
Series 820 Instruction Manual
Table of Contents
IM-82-C
0-3
Table of Contents
Chapter 1 Introduction
Introduction.............................................................1-1
Using this Manual .................................................1-1
Safety Information.................................................1-2
Receipt of System Components..................................1-2
Technical Assistance ..............................................1-2
Top Trak Features......................................................1-3
The 820 Series Flow Sensing Principle .............................1-4
Chapter 2 Installation
Installation Overview ..................................................2-1
Installing the Transducer ..............................................2-2
Compression Fittings .............................................2-2
VCO Fittings .......................................................2-2
VCR Fittings .......................................................2-3
All 1/2-inch Size Connections....................................2-3
Wiring the Transducer.................................................2-4
Standard 0-5 VDC Output Signal Wiring.......................2-5
Optional 4-20 mA Output Signal Wiring........................2-5
Remote Display Installation...........................................2-6
Chapter 3 Operation
Transducer Operation..................................................3-1
Transducer Accuracy..............................................3-1
Referencing the Transducer to Non-Standard Conditions . . . .3-2
Transducer Over-Ranging ........................................3-2
Zero and Span Adjustments ......................................3-3
Chapter 4 Maintenance and Repair
Transducer Cleaning...................................................4-1
Flow Path Cleaning Model 822/824 .................................4-2
Inlet and Outlet Screens...........................................4-2
Laminar Flow Element............................................4-3
Flow Path Cleaning Model 826/827 .................................4-4
Laminar Flow Element............................................4-4
Flow Path Cleaning Model 822-S/824-S............................4-5
Laminar Flow Element............................................4-5
Sensor Cleaning and Inspection .................................4-8
Transducer Calibration ................................................4-9
Transducer Troubleshooting.................. ...................... 4-11
Returning Equipment to the Factory ............................... 4-12
Содержание Top-Trak 820 Series
Страница 6: ...Table of Contents Series 820 Instruction Manual 0 6 IM 82 C ...
Страница 20: ...Chapter 3 Operation Series 820 Instruction Manual 3 4 IM 82 C ...
Страница 44: ...Series 820 Instruction Manual Appendix B Specifications IM 82 C B 3 ...
Страница 45: ...Appendix B Specifications Series 820 Instruction Manual B 4 IM 82 C ...