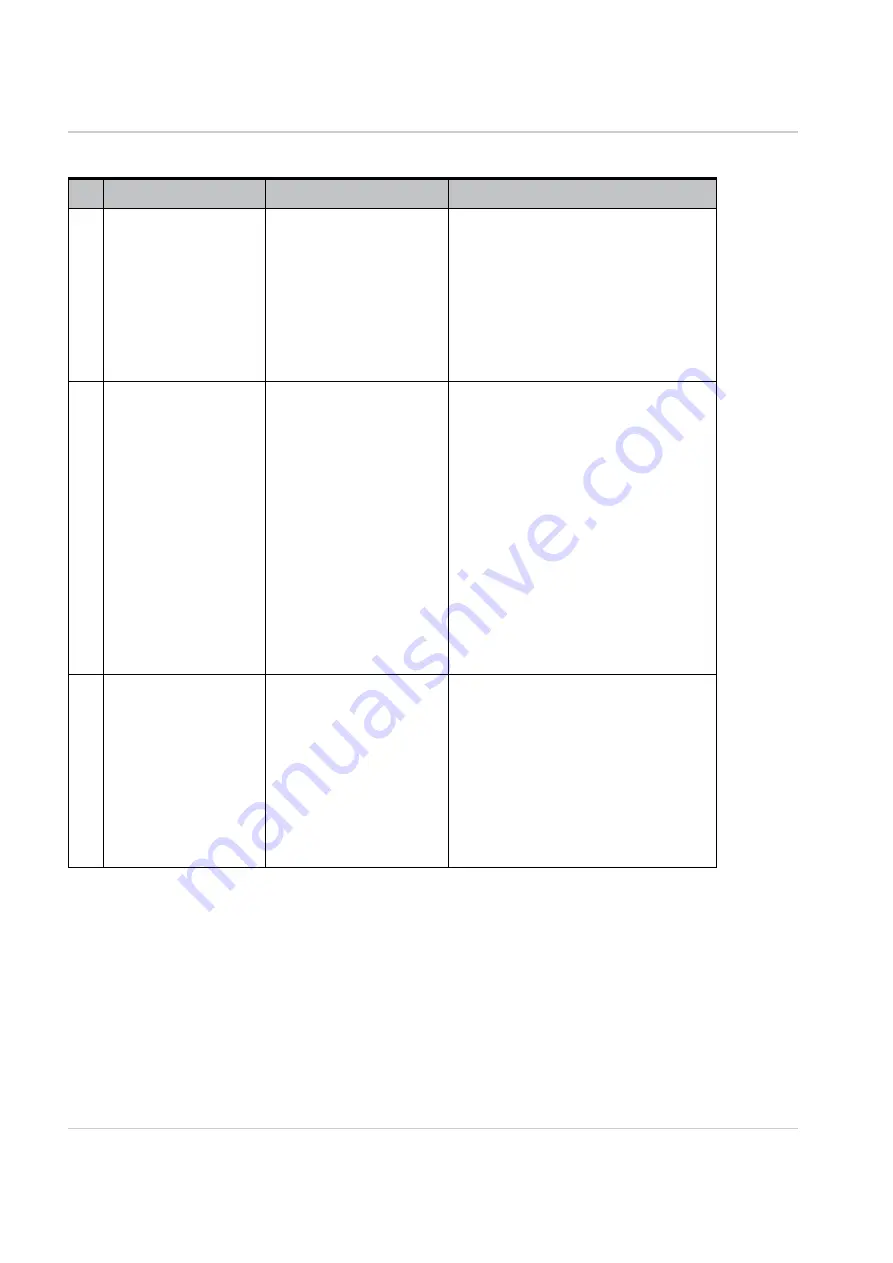
Hardware Design Guide
Rev 3.0 Aug.19
34
41111116
5
Before handling the
PCBA, they must be
cooled to 35°C or below
after they have
undergone a reflow-
soldering process, in
order to prevent a
positional shift which
may occur when the
module is still hot.
1. You may use an electric
fan behind the reflow
machine to cool them down.
2. Cooling the PCBA can
prevent the module from
shifting due to fluid effect.
It is very easy to cause a positional offset
to the module and its patch antenna when
handling the PCBA under high
temperatures.
6
1. When separating the
PCBA panel into
individual pieces using
the V-Cut process,
special attention is
needed to ensure that
there are sufficient gaps
between patch antennas.
2. If the V-Cut process is
not available and the
pieces must be
separated manually,
please make sure the
operators are not using
excess force which may
cause a rotational offset
to the patch antennas.
1. The blade and the patch
antenna must have a gap
greater than 0.6mm.
2. Do not use the patch
antenna as the leverage
point when separating the
panels by hand.
1. Tests must first be performed to
determine if the V-Cut process is going to
be used. Ensure that there is enough
space between the blade and patch
antenna so that they do not touch one
another.
2. An uneven amount of manual force
applied to the separation will likely to cause
a positional shift in the patch antenna and
module.
7
When separating the
panel into individual
pieces during latter half
of the production
process, special
attention is needed to
ensure the patch
antennas do not come in
contact with one another
in order to prevent
chipped corners or
positional shifts.
Use a tray to separate the
individual pieces.
It is possible to chip a corner and/or cause
a shift in position if the patch antennas
come into contact with each other.
Table F-1: Precautions
Details
Suggestions
Notes