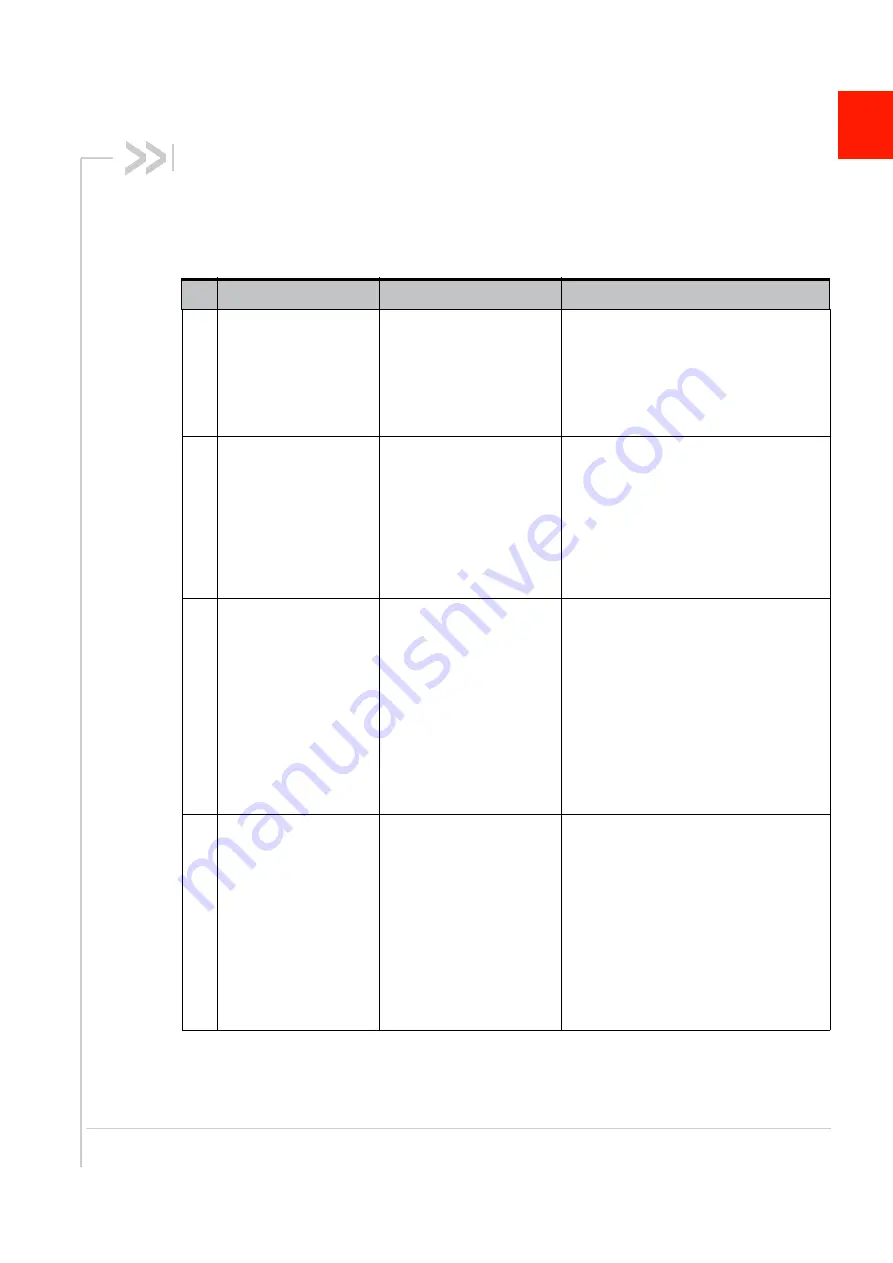
Rev 3.0 Aug.19
33
41111116
F
Appendix F: Reflow Soldering
Precautions
Table F-1: Precautions
Details
Suggestions
Notes
1
Before proceeding with
the reflow-soldering
process, the GPS
module must be pre-
baked.
Pre-bake Time:
6 Hours @ 60°±5°C or
4 Hours @ 70°±5°C
The maximum tolerated temperature for
the tray is 100°C.
After the pre-baking process, please make
sure the temperature is sufficiently cooled
down to 35°C or below in order to prevent
any tape and reel deformation.
2
Because PCBA (along
with the patch antenna)
is highly endothermic
during the reflow-
soldering process, extra
care must be taken with
the GPS module's solder
joint for any signs of cold
welding or false welding.
The parameters of the
reflow temperature must be
set accordingly to module’s
reflow-soldering
temperature profile.
Double check to see if the surrounding
components around the GPS module are
displaying symptoms of cold welding or
false welding.
3
Special attention is
needed for the PCBA
board during reflow-
soldering to see if there
are any symptoms of
bending or deformation
to the PCBA board,
possibly due to the
weight of the module. If
so, this will cause
concerns at the latter half
of the production
process.
A loading carrier fixture must
be used with PCBA if the
reflow soldering process is
using rail conveyors for the
production.
If there is any bending or deformation to
the PCBA boards, this might cause them to
collide into one another during the
unloading process.
4
Before the PCBA
undergoes a reflow-
soldering process, the
production operators
must visually check to
see if there are positional
offsets to the module,
because it will be difficult
to readjust after the
module has gone
through the reflow-
soldering process.
The operators must visually
check and readjust the
position before the reflow-
soldering process.
If the operator is planning to readjust the
module position, please do not touch the
patch antenna while the module is hot in
order to prevent a rotational offset between
the patch antenna and module.