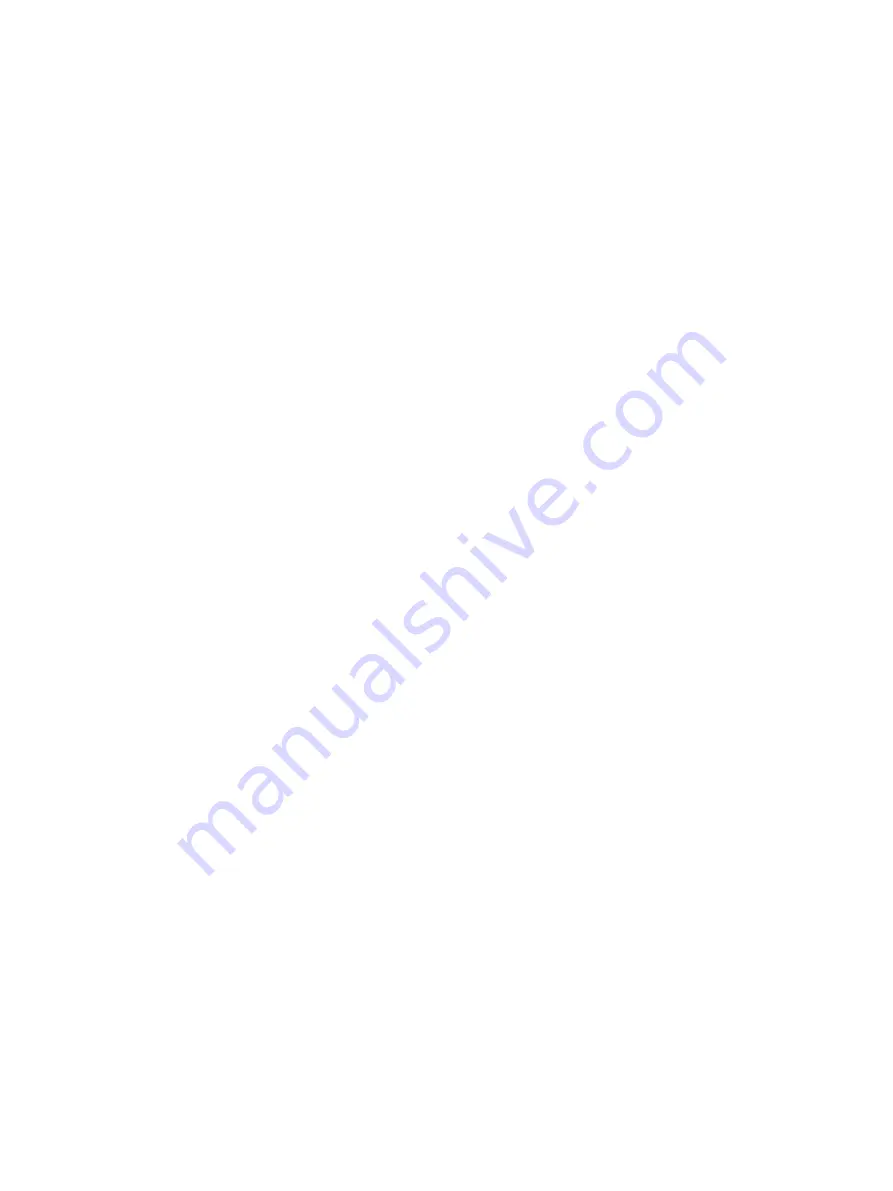
Simulating machining
7
7.1
Overview
During simulation, the current program is calculated in its entirety and the result displayed in
graphic form. The result of programming is verified without traversing the machine axes.
Incorrectly programmed machining steps are detected at an early stage and incorrect
machining on the workpiece prevented.
Graphic display
The simulation uses the correct proportions of the workpiece, tools, chuck, counterspindle and
tailstock for the screen display.
For the spindle chuck and the tailstock, dimensions are used that are entered into the "Spindle
Chuck Data" window.
For non-cylindrical blanks, the chuck closes up to the contour of the cube or polygon.
Depth display
The depth infeed is color-coded. The depth display indicates the actual depth at which
machining is currently taking place. "The deeper, the darker" applies for the depth display.
Definition of a blank
The blank dimensions that are entered in the program editor are used for the workpiece.
The blank is clamped with reference to the coordinate system, which is valid at the time that the
blank was defined. This means that before defining the blank in G code programs, the required
output conditions must be established, e.g. by selecting a suitable zero offset.
Programming a blank (example)
G54 G17 G90
WORKPIECE(,,,"Cylinder",112.0,-50,-80.00,155,100)
T="NC-SPOTDRILL_D16
Machine references
The simulation is implemented as workpiece simulation. This means that it is not assumed that
the zero offset has already been precisely scratched or is known. In spite of this, unavoidable
MCS references are in the programming, such as for example, the tool change point in the
MCS, the park position for the counterspindle in the MCS or the position of the counterspindle
slide. Depending on the actual zero offset - in the worst case - these MCS references can mean
that collisions are shown in the simulation that would not occur for a realistic zero offset - or vice
versa, collisions are not shown, which could occur for a realistic zero offset. This is the reason
why in ShopTurn programs, in the case of a simulation, the program header calculates an
Turning
Operating Manual, 06/2019, A5E44903486B AB
235
Содержание SINUMERIK 840D sl
Страница 8: ...Preface Turning 8 Operating Manual 06 2019 A5E44903486B AB ...
Страница 70: ...Introduction 2 4 User interface Turning 70 Operating Manual 06 2019 A5E44903486B AB ...
Страница 274: ... Creating a G code program 8 8 Selection of the cycles via softkey Turning 274 Operating Manual 06 2019 A5E44903486B AB ...
Страница 275: ... Creating a G code program 8 8 Selection of the cycles via softkey Turning Operating Manual 06 2019 A5E44903486B AB 275 ...
Страница 282: ...Creating a G code program 8 10 Measuring cycle support Turning 282 Operating Manual 06 2019 A5E44903486B AB ...
Страница 344: ...Creating a ShopTurn program 9 19 Example Standard machining Turning 344 Operating Manual 06 2019 A5E44903486B AB ...
Страница 716: ...Collision avoidance 12 2 Set collision avoidance Turning 716 Operating Manual 06 2019 A5E44903486B AB ...
Страница 774: ...Tool management 13 15 Working with multitool Turning 774 Operating Manual 06 2019 A5E44903486B AB ...
Страница 834: ...Managing programs 14 19 RS 232 C Turning 834 Operating Manual 06 2019 A5E44903486B AB ...
Страница 856: ...Alarm error and system messages 15 9 Remote diagnostics Turning 856 Operating Manual 06 2019 A5E44903486B AB ...
Страница 892: ...Working with two tool carriers 18 2 Measure tool Turning 892 Operating Manual 06 2019 A5E44903486B AB ...
Страница 912: ...HT 8 840D sl only 20 5 Calibrating the touch panel Turning 912 Operating Manual 06 2019 A5E44903486B AB ...
Страница 927: ...Appendix A A 1 840D sl 828D documentation overview Turning Operating Manual 06 2019 A5E44903486B AB 927 ...