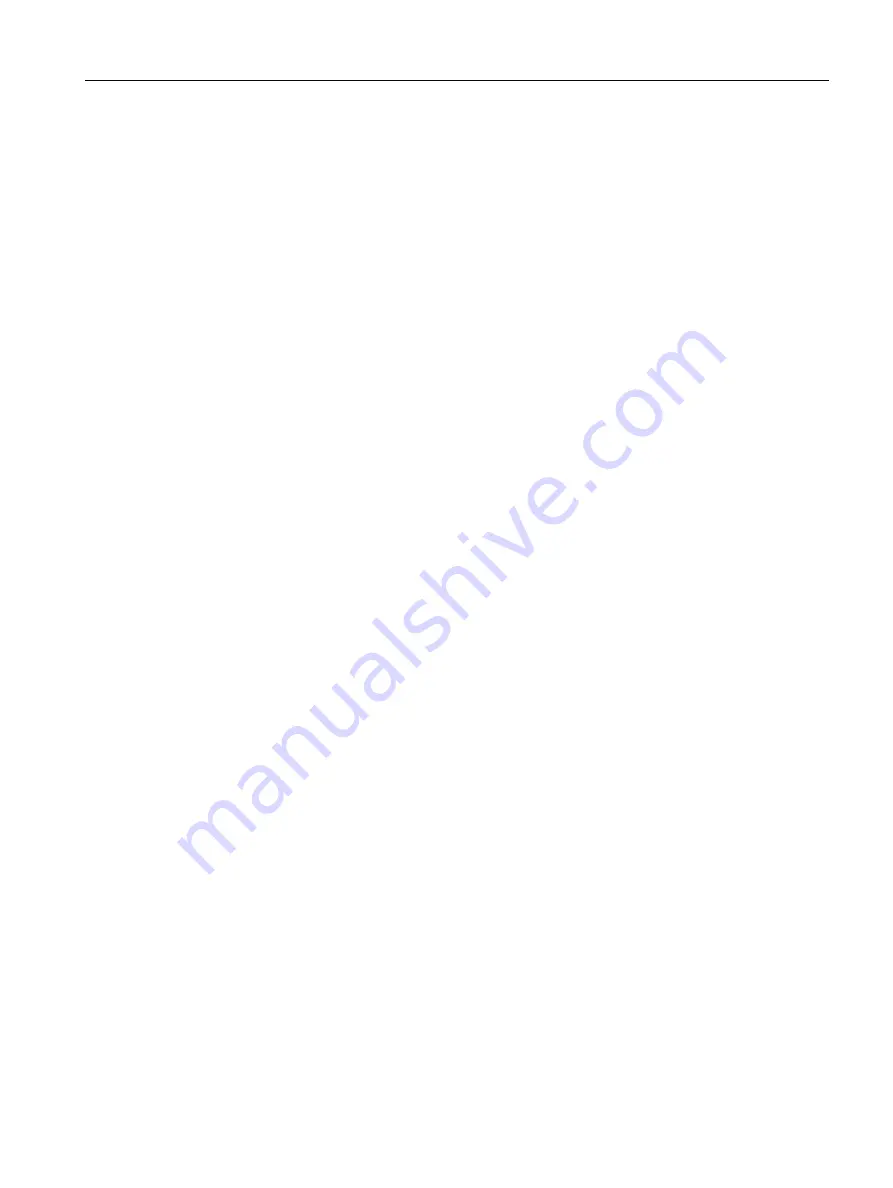
S1: Spindles
16.4 Configurable gear adaptation
Basic Functions
Function Manual, 09/2011, 6FC5397-0BP40-2BA0
1323
Sequence
If a gear stage change is suppressed, if necessary, the interpolator will limit the programmed spindle speed to the
permissible speed range of the active gear stage.
NC/PLC interface signals DB31, ... DBX83.2 (setpoint speed increased) and DB31, ... DBX83.1 (setpoint speed
limited) generated as a result of this limit are suppressed.
Monitoring by the PLC program is not necessary during DryRun and in dry run feedrate.
When the gear stage change is suppressed, no new gear stage setpoint (DB31,... DBX82.0-82.2) is output to the
PLC.
The gear stage change request DB31, ... DBX82.3 (change gear) is also suppressed.
This ensures that no gear stage change information has to be processed by the PLC program.
Determining the last active gear stage
System variable $P_GEAR returns the gear stage programmed in the part program (which may not have been
output to the PLC).
System variable $AC_SGEAR can be used to read the last active gear stage from the part program,
synchronized actions and at the user interface.
Behavior after deselection
The DryRun function can be deselected within a running part program. Once it has been deselected, the correct
gear stage requested by the part program must be identified and selected.
It cannot be assured that the remainder of the part program will run without errors until the correct gear stage has
been activated. Any necessary gear stage change is performed in the system REPOS started on deselection if
the spindle is in speed control mode. A complete gear stage change dialog takes place with the PLC and the last
programmed gear stage is activated.
If, for REPOS, there is a mismatch between the gear stage programmed in the part program and the actual gear
stage supplied via the NC/PLC interface, then no gear stage change takes place.
The same applies to the SERUPRO function.
Further explanations regarding the block search function SERUPRO, see:
References:
Function Manual, Basic Functions; Mode Group, Channel, Program Mode, Reset Response (K1)
Boundary conditions
If the gear stage change is suppressed, the output spindle speed moves within the speed range specified by the
current gear stage.
The following restrictions apply to the subsequent activation of a gear stage change with REPOS:
• The gear stage change is not activated subsequently if the spindle in the deselection or target block is a
command spindle (synchronized action) or PLC spindle (FC18).
• If the gear stage cannot be activated because the spindle is in position or axis mode or a link is active, alarm
22011"Channel%1 block%3 spindle2% Change to programmed gear stage not possible" is signaled.
Содержание SINUMERIK 828D Turning
Страница 34: ...Basic Functions 34 Function Manual 09 2011 6FC5397 0BP40 2BA0 ...
Страница 146: ...A3 Axis Monitoring Protection Zones 2 6 Data lists Basic Functions 146 Function Manual 09 2011 6FC5397 0BP40 2BA0 ...
Страница 328: ...F1 Travel to fixed stop 6 5 Data lists Basic Functions 328 Function Manual 09 2011 6FC5397 0BP40 2BA0 ...
Страница 816: ...K2 Axis Types Coordinate Systems Frames 10 9 Data lists Basic Functions 816 Function Manual 09 2011 6FC5397 0BP40 2BA0 ...
Страница 1198: ...P4 PLC for SINUMERIK 828D 14 6 Function interface Basic Functions 1198 Function Manual 09 2011 6FC5397 0BP40 2BA0 ...
Страница 1752: ...Appendix 20 2 Overview Basic Functions 1752 Function Manual 09 2011 6FC5397 0BP40 2BA0 ...
Страница 1774: ...Glossary Basic Functions 1774 Function Manual 09 2011 6FC5397 0BP40 2BA0 ...