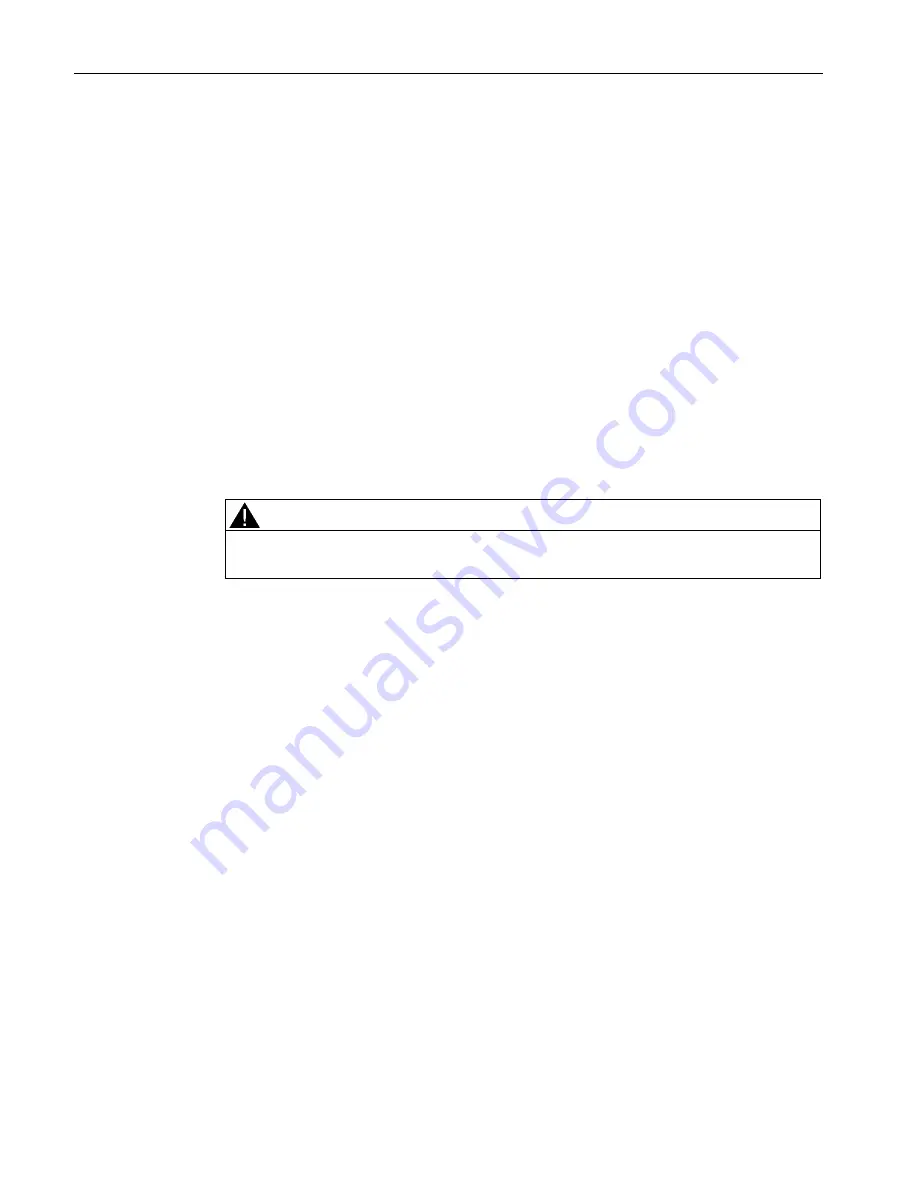
Electric adjustment and commissioning
Elevator door drive AT12
24
Manual, 02/2012, A2B00086683A-04
6.
Keep the learn run button
(S501) pressed until the door moves (learn run has started).
During the learn run, the door is opened about 10 cm, and closed once or twice at creep
speed.
The friction of the door system is then determined by opening and closing the door once
through a range of 25 cm at creep speed.
The door then opens and closes through its complete range of movement at reduced
speed.
After the door has opened about 10 cm, it passes through a short acceleration ramp to
determine the weight of the door.
In the "CLOSED" position, the door parameters and the determined door width are saved.
During the learn run and while the parameters are being saved, LED H501 flashes green.
When saving has finished, the LED shows a steady green light.
7.
The door can now be completely opened by briefly pressing the learn run button.
Pressing the button again, when the door is in the end position "Open", closes the door
completely.
8.
Switch off mains supply
9.
Connect the control signals to the X101 connector as shown in the terminal circuit
diagram (see Appendix Terminal circuit diagram of control inputs (Page 43)).
CAUTION
The controller will be operative after the next switch-on. If a control signal is present, the
door will move in the set direction.
10.
Switch on the controller (plug in the mains plug or connector X101).
LED H501 lights red for about two seconds, and then changes to a steady green after the
application software has started and there are no errors in the controller. If the LED
continues to show red, repeat the learn run once more, as described above. If the LED
lights with a red flash code, one of the errors described below is present:
Flash code:
1: CPU error
2: Brake chopper error
3: Error in the second shutdown route
4: Motor temperature monitoring
5: Unknown motor (X801)
6: Blockage detected in closing direction
7: Incremental encoder error (X801)
8: Parameter learn run ended with error
9: Motor overcurrent
10: Blockage detected in opening direction
11: Overvoltage (motor)
12: Undervoltage (motor)
13: Error at the ammeter
14: Determined door weight too high
15: Output stage faulty
16: Overvoltage 15 V circuit
17: Undervoltage 15 V circuit
11.
If the control signal
"CLOSE" is present, the door moves into the "CLOSED" position at
initial speed. If the control signal
"OPEN" is present, the door moves into the "OPEN"
position at initial speed.
Содержание SIDOOR AT12
Страница 2: ......
Страница 8: ...Introduction Elevator door drive AT12 8 Manual 02 2012 A2B00086683A 04 ...
Страница 10: ...Safety notes 2 1 General safety instructions Elevator door drive AT12 10 Manual 02 2012 A2B00086683A 04 ...
Страница 12: ...Definitions Elevator door drive AT12 12 Manual 02 2012 A2B00086683A 04 ...
Страница 14: ...Overview of controls Elevator door drive AT12 14 Manual 02 2012 A2B00086683A 04 ...
Страница 22: ...Mechanical installation and setting Elevator door drive AT12 22 Manual 02 2012 A2B00086683A 04 ...
Страница 28: ...The relay contacts Elevator door drive AT12 28 Manual 02 2012 A2B00086683A 04 ...
Страница 30: ...CAN Elevator door drive AT12 30 Manual 02 2012 A2B00086683A 04 ...
Страница 32: ...Travel curve Elevator door drive AT12 32 Manual 02 2012 A2B00086683A 04 ...
Страница 36: ...Technical data 12 3 Regulations and standards Elevator door drive AT12 36 Manual 02 2012 A2B00086683A 04 ...
Страница 46: ...Appendix A 9 Settings record Elevator door drive AT12 46 Manual 02 2012 A2B00086683A 04 ...
Страница 47: ......