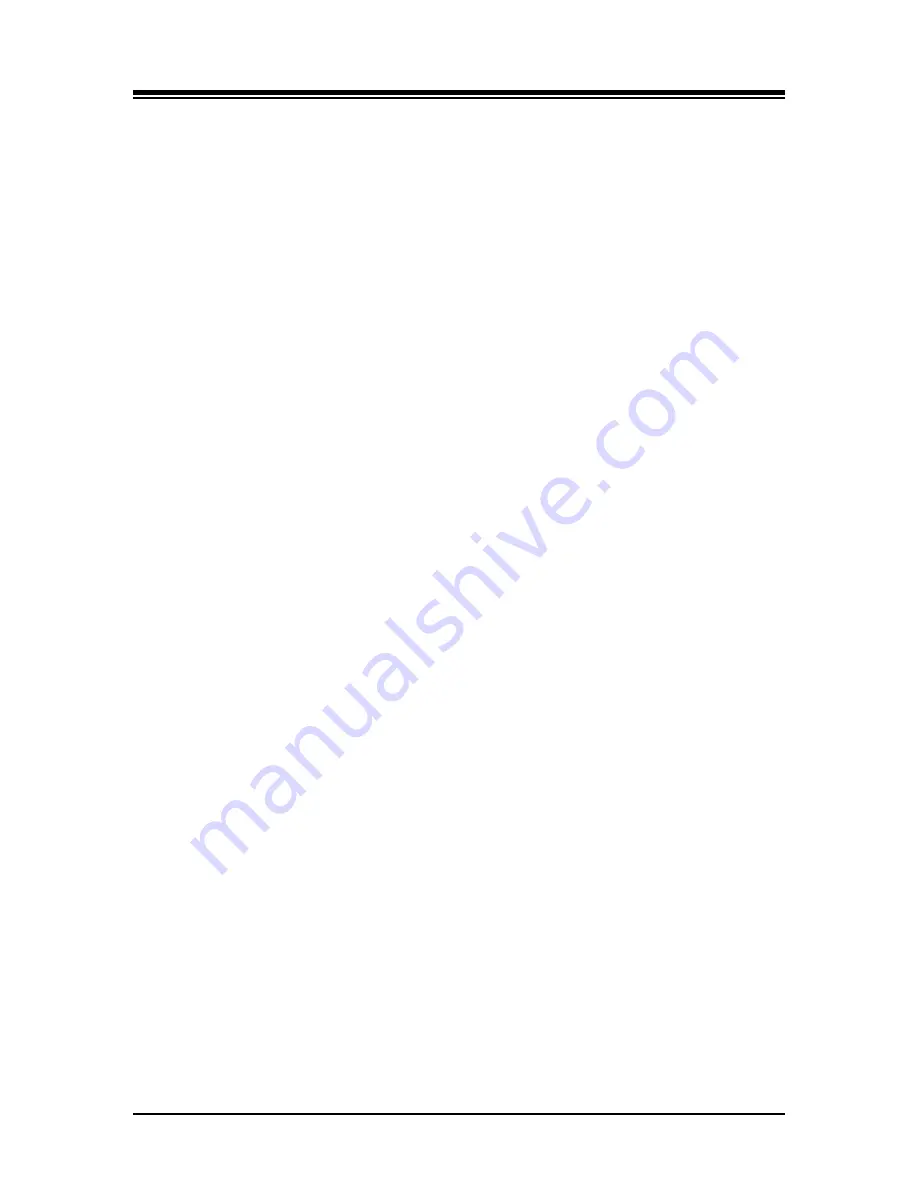
Chapter 1
Turbine Package System Overview
1-16
Demister or Filter/Coalescer (if applicable)
The off-skid demister or filter/coalescer is used to remove liquids and particulates from the gas
fuel.
The gas enters the filter/colaescer at the inlet pipe and passes through a special filter element
into the top chamber, from where it leaves the filter/colaescer in a clean dry condition via the
outlet pipe.
Pipeline Trace Heating (if applicable)
The gas fuel pipelines are trace heated to prevent the formation of condensation in the gas
system.
Fuel Strainer
A 76-micron fuel strainer (XF
94) is located in the fuel pipework downstream of the skid edge to
protect the burner orifices from blockage and contamination.
Block
Valves
The primary (XV7) and secondary (XV6) block valves provide isolation of the on–skid fuel system
from the gas supply. They are controlled by integral actuators, which are operated by instrument
air and spring pressure. The instrument air supply to the actuators is controlled by pilot solenoids
(SOL5 and SOL110).
The block valves are designed to fail in the closed position.
Vent Valve
The vent valve (XV212) provides for venting of the gas fuel pipework between the two block
valves on turbine shutdown. The valve is controlled by an integral actuator operated by
instrument air and spring pressure. The instrument air supply to the actuator is controlled by a
pilot solenoid (SOL470).
The vent valve is designed to fail in the open position.
Fuel Control Valve/Actuator Assemblies
The main and pilot fuel control valves (XV150 and XV149) are of the rotary ball valve type and
operated through a zero backlash coupling by electrically operated rotary actuators (XM26 and
XM27). Each valve/actuator assembly is firmly mounted and connected into the fuel system. The
valves are calibrated and set up to meter the fuel flow to the burners under the control of an
electronic control unit. Integral position transmitters (ZT12 and ZT103) monitor the position of
the control valve actuators.