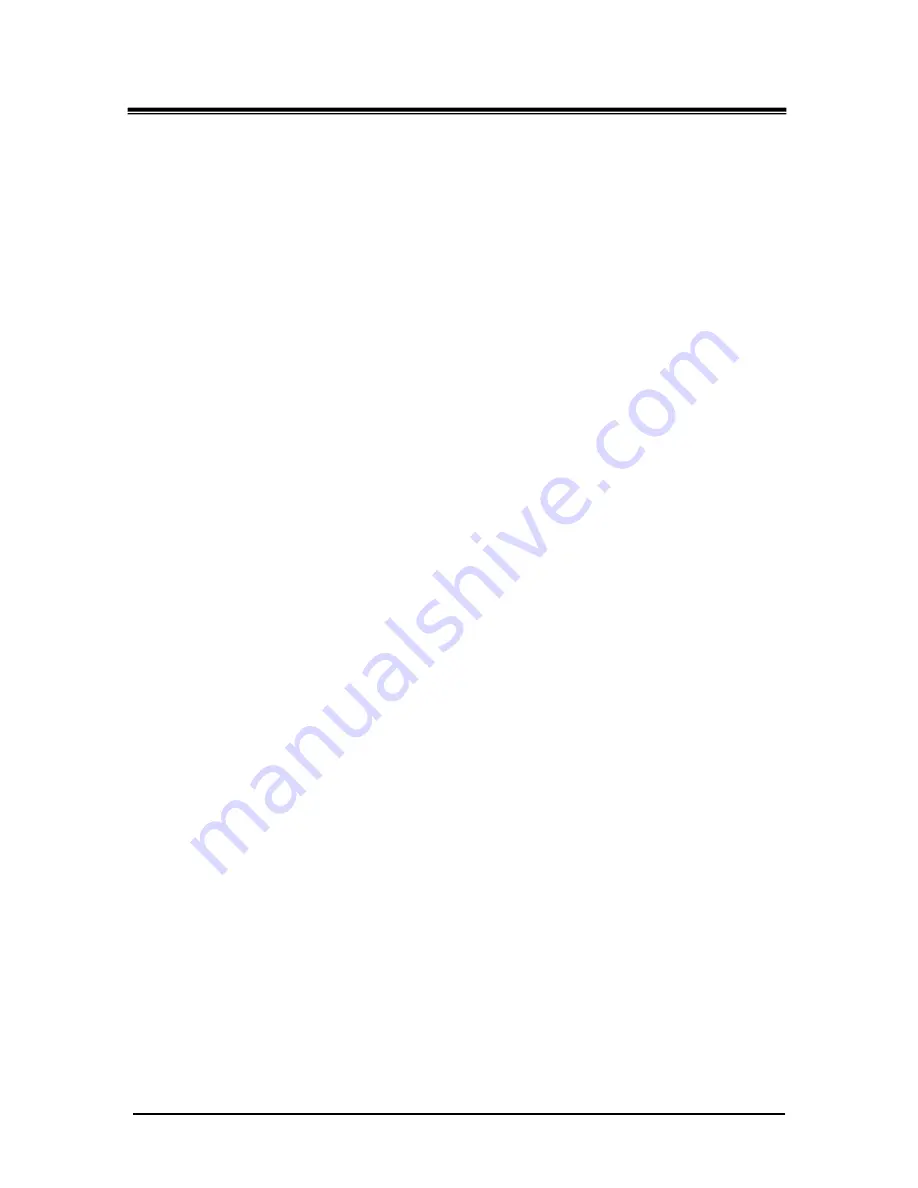
Turbine Package Operators Manual
Chapter 1
Turbine Package System Overview
1-5
Engine Core Assembly
The SGT-400 is a twin shaft, simple open cycle; non-regenerative industrial gas turbine designed
for both power generation and mechanical drive applications. The core engine consists of a
radial inlet casing through which air enters the eleven stage axial compressor for compression
prior to entry to the combustion system.
General Description
The combustion system employs reverse flow combustion chambers to mix, burn and expand the
air fuel mixture to drive the twin shaft turbine and exit through the exhaust diffuser.
The integrated compressor and compressor turbine assembly, and separate power turbine rotor
assembly, are supported and located by journal and thrust bearings in the inlet, compressor
turbine and power turbine bearing housings respectively.
An auxiliary gearbox provides ancillary drives for the main lubricating oil pump, the liquid fuel
pump (if fitted), and to provide drive to the turbine from the starting system.
Refer to the
SECTIONAL ARRANGEMENT – SGT-400 (MW-1-1)
located in this Manual
Volume.
Air Inlet Casing
The Air Inlet Casing is secured to the Inlet Bearing Housing both designed and shaped to provide
a smooth path for the incoming air to the compressor. An inlet screen and a flexible joint, which
accommodates relative movements due to thermal expansion, are fitted to the rectangular casing
entry point to which external ducting is connected.
Compressor Inlet Bearing Housing Assembly
The Compressor Inlet Bearing Housing Assembly, which is mounted on the turbine/auxiliary
gearbox support casing, provides support for the Air Inlet Casing and Low Pressure (LP)
Compressor Stator casing. Provision is made, at the bottom of the casing, for the attachment of
the front gas generator support assembly. A tilting pad journal and thrust bearing assembly
within the housing supports and locates the inlet end of the gas generator rotor.
Compressor Stator Casings
The Compressor Stator Casings consist of an LP Compressor Stator casing and a High Pressure
(HP) Compressor Stator casing.
The LP Compressor Stator casing is split along its centerline, bolted at its forward face to the
Compressor Inlet Bearing Housing assembly, and has a spigot bolted to the center casing at the
rear end. Boroscope access holes are provided in the top half casing to enable examination of
the compressor stator and rotor blades.
Variable geometry inlet guide vanes form the first row of stator vanes, with the subsequent four
rows being variable geometry compressor stator blades, which assist starting and prevention of
compressor surge. An externally mounted operating mechanism controls the movement of the
vanes. The remaining LP stator blades are retained by dovetail grooves in the casing.