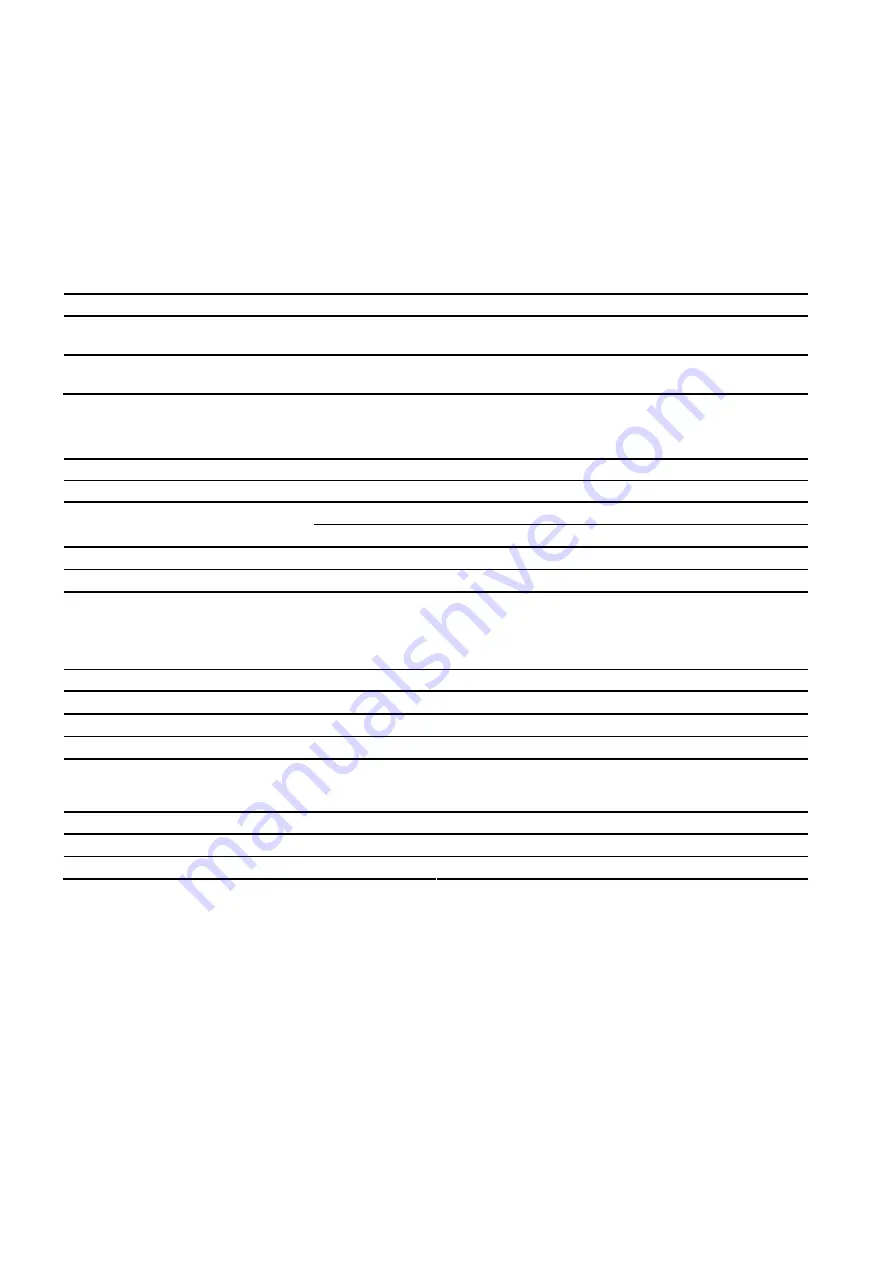
Compact Operating Instructions in accordance with EN 61010-1 and EN 60079-0
46
A5E45779389002-01, 09/2018
Differential pressure monitoring
Only applies to analyzer version Ex p with leakage compensation.
The sample gas pressure must be present in the analyzer (within the specified limits, see Technical specifications for
operation in hazardous areas (Page 42)) in a fail-safe manner. If only an operationally reliable supply is available, an
additional differential pressure switch must be provided (see also point 5 in "Special conditions" of the EC type examination
certificate).
If flame arrestors are fitted, differential pressure switches and/or relative pressure sensors must be connected via a T-fitting
between the sample gas inlet couplings and the flame arrestors (see Auto-Hotspot and assembly diagram for the version
Ex p with leakage compensation Connection diagram for the versions Ex px with leakage compensation (Page 23)).
Accessories required for differential pressure monitoring:
Differential pressure switches
Order No.
Wetted parts mate-
rials
Switching point
For corrosive and non-corrosive sample
gases
7MB8000-5AA Stainless steel
1.4571
Settable in the range -20 to +20 hPa
Accessories
Valid for the following analyzer versions:
Flame inhibitor
Device
Material
Order No.
OXYMAT 6 / CALOMAT 6
Stainless steel
7MB8000-6CA
Hastelloy
7MB8000-6CB
CALOMAT 62
Stainless steel
7MB8000-6DA
Hastelloy
7MB8000-6DB
The design of parts wetted by the sample gas must meet the application requirements and should be selected accordingly.
Applies to all analyzer versions.
Isolating relay
Order No.
7MB8000-4AB
7MB8000-4AA
Coil power supply
110 V AC
240 V AC
Contacts
8 NO contacts
8 NO contacts
Note: The relays must be installed in a separate Ex e enclosure!
Isolating transformer
Order No.
7MB8000-3AB
Output signal (safety)
18.8 V / 107 mA / 503 mW