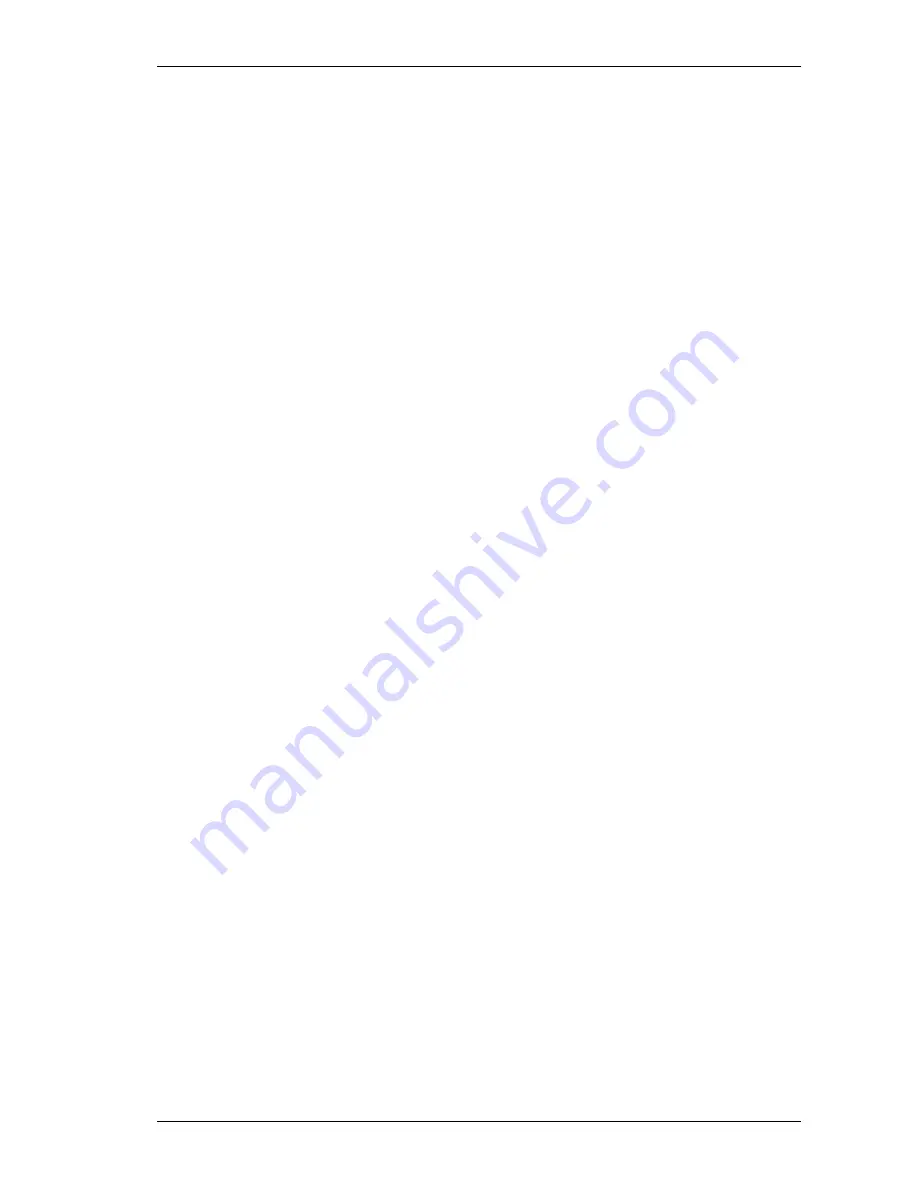
7SG15 MicroTAPP Commissioning
©2012 Siemens Protection Devices Limited
Chapter 7 Page 6 of 10
6.4.3 TPI Operation
Operate the tap changer and confirm correct indications. If the transformer cannot be taken out of service the top
tap position can conveniently be simulated by temporarily disconnecting the wire going to terminal B25 and then
shorting B25 to B23 (for a resistor type sender unit).
After replacing any temporary connections, check the indication through the full range of the tap-changer (if
possible).
In the unlikely event that satisfactory calibration cannot be obtained, the sender unit resistors should be replaced.
Suitable resistors are 100 ohm, 1 Watt, 1% tolerance metal film resistors.
6.4.3.1 Checking for Normal Operation
Set the relay to Local/Manual. Operate the tap changer in the raise direction and observe the normal correct
operation of tap changer. Immediately the "in Progress" LED goes off, operate the tap change once more in the
same direction and again observe correct operation.
Repeat a) for the lower direction.
6.4.3.2 Checking
for
Lockout
Carry out a raise operation but this time simulate a potential runaway condition by permanently energising the
‘Raise’ or ‘Lower’ contactors or, alternatively, by repeated operation of the tap change control switch. The
Runaway Prevention Unit should lock out soon after the first complete tap change operation, depending upon the
tap change operating time.
Repeat for the lower direction.
For very fast tap change mechanisms more than one tap change operation may occur before the lockout
operates. In this case great care should be exercised if the test is carried out with the transformer on load.
7 Operational Service
7.1 Off-Load Testing
Prior to being put on load but with the transformer energised, final operational checks can be carried out.
7.1.1 VT calibration
In some situations the VT output voltage may be found to be incorrect (measurement error or a non-standard ratio
for instance). Any errors can be corrected by use of the settings/transformer/VT ratio option from the relay menu
system.
For example, assume that a VT is used having a ratio of 10kV/110V but is known to actually produce 109V when
the primary voltage is 10kV. The effective ratio is, therefore, 10.09kV/110V.
Using the relay menu system the VT ratio is changed to 10.1kV/110 effectively correcting the error.
7.1.2 Tap change operation
1
Set the MicroTAPP to Local/Auto
2
Set LDC to 0%, adjust the basic setting and balance the relay, note the voltage
3
Increase the basic setting for a higher voltage so that the relay indicates ‘low’. Confirm that the 'raise'
contactor is operated
4
Decrease the basic setting for a lower voltage so that the relay indicates ‘high’. Confirm that the ‘lower’
contactor is operated
5
Return the setting to balance