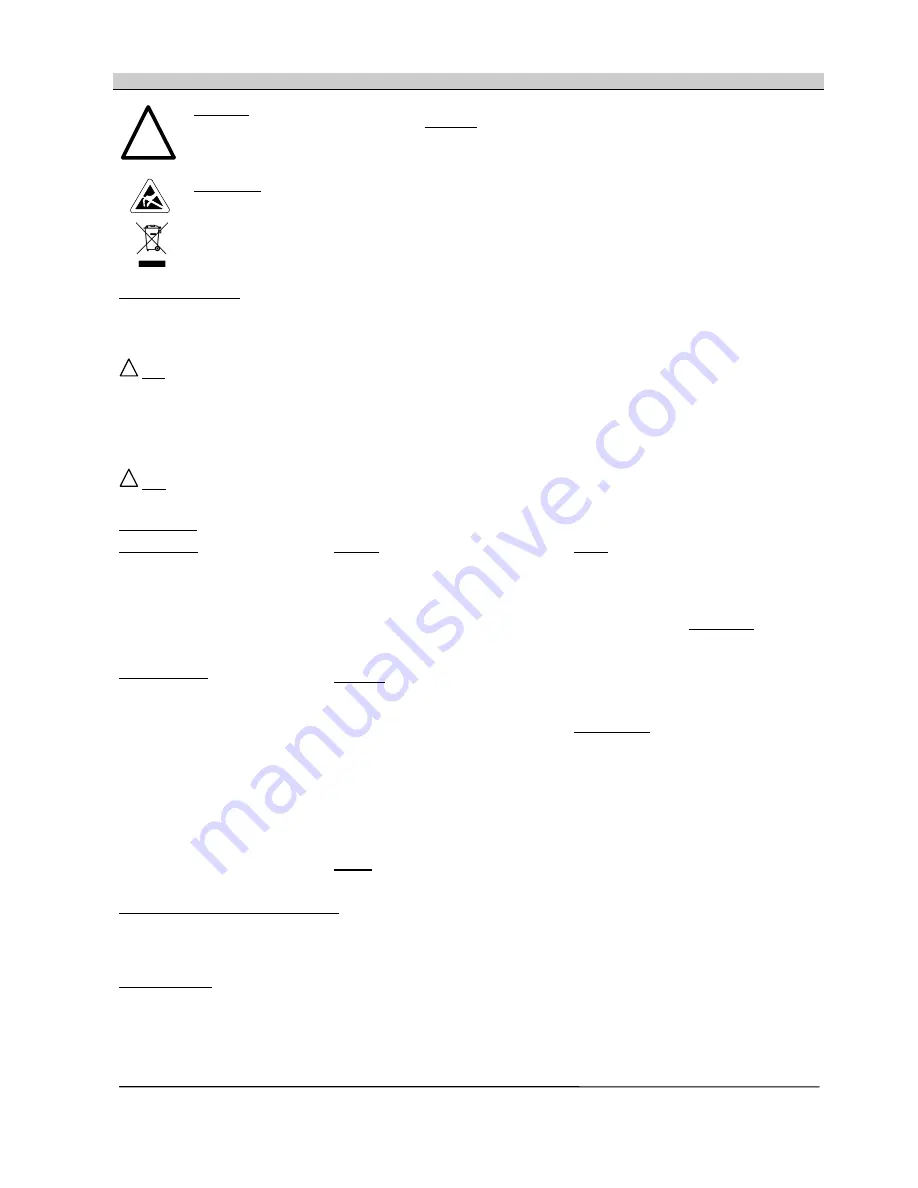
Siemens AG Österreich
Seite 5 von 6
Bestell-Nr.: C98130-A7524-A1-07-7419
SITOP select / 08.2013
Printed in Austria
English
!
WARNING
This device is only suitable for operation with 24 V
DC voltage
(safety extra-low voltage). Direct connection of these devices to the 110 V-,
230 V-, 400 V-power system, or to a power system with a higher voltage, may consequently result in death, severe personal injury or
substantial property damage. Only qualified personnel should work on or around this equipment. The product will function correctly and safely
only if it is transported, stored, set up and installed as intended.
IMPORTANT
Only specially trained personnel are allowed to open the equipment.
Electrostatic sensitive devices (ESD)
Disposal guideline
Packaging and packing aids can be recycled and should always be disposed of for reuse.
The product itself shall not be disposed of as normal domestic waste.
Functional description
SITOP select is a built-in electronic diagnostic module. It must be installed taking into account all relevant DIN/VDE specifications and other national standards.
SITOP select is designed to be connected to stabilized 24 V DC power supplies with an output current of 5 A to 40 A.
SITOP select allows the 24 V DC output voltage generated by a stabilized power supply to be split between several load circuits and the current monitored
separately for each load circuit. The rated current of each load circuit can be set with a potentiometer (1) between 2 A and 10 A.
!
Note: It is not permitted to connect several outputs (6) in parallel in order to increase the power.
Each output is monitored to determine whether its individual rated current is exceeded (green LED (3), signaling contact (4) closed). If the disconnection
conditions are fulfilled, in other words if overloading occurs, the output concerned is disconnected (red LED, signaling contact open = normal position). After
approximately 20 s (red blinking LED), the disconnected output can be acknowledged and reset by pressing the Reset button (5).
The diagnosis module is equipped with one FK2 blade-type fuse (2) per output which is accessible from outside and can be used as additional line protection if
necessary. As delivered, the diagnosis module is fitted with 15 A FK2 blade-type fuses. These can be substituted by blade-type fuses with lower rated current,
depending on the potentiometer setting (see safety/selection table). The user has to make sure that conductor cross-sections at the output of the diagnosis
module conform to the maximum current according to standards that apply.
!
Note: In order to prevent damage to the device caused by overvoltage, drawing the FK2 blade-type fuse under load is only allowed if connected inductive
electric consumers are protected by a free-wheeling arm (free-wheeling diode)!
Technical data
Input variables
Rated input voltage:
24 V DC
Working voltage range:
22 V to 30 V DC
Connection threshold:
Approx. 12 V
Max. input current:
40 A
Output variables
Rated output voltage:
24 V DC, equivalent to input voltage
Typical voltage drop with 10 A per branch:
300 mV
Branch current setting range:
2 A to 10 A, set with potentiometer
Parallel connection of several branches in
order to increase the power is not permitted.
Typical current for disconnected and short-
circuited output:
20 mA
Switch-on delay:
for all outputs alike,
setting values: 0 ms, 24 ms, 100 ms
Ambient
Temperature
Storage and transport:
-40 to +85°C
Operation:
0 to +60°C
Humidity rating:
Corresponds to climatic category 3K3 acc. to
EN 60721, Part 3, no condensation
Pollution degree 2
Natural air cooling
Signaling
Green LED:
Output through-connected
Red LED:
Output disconnected owing to overcurrent
Red blinking LED:
Overcurrent disconnection can be reset by pressing
the RESET button
Common signaling contact:
Floating relay contact
Signal contact opens (= normal position) if one or
more outputs are disconnected because of
overloading or if a fuse fails
Contact rating: 24 V / 0.5 A
Weight
0.4 kg
Safety
Standard fuses:
15 A FK2 blade-type fuses (= max. permitted value)
Manufacturer: e.g. Wickmann, FK2 series, 19 mm long
(Website: www.wickmann.com)
Lower values can be selected if necessary, depending on
the potentiometer setting. Selection table :
Max. setting
►
Min.
fuse
2
A
►
3
A
3
A
►
4
A
4
A
►
5
A
6
A
►
7.5
A
8
A
►
10
A
10
A
►
15
A
Specifications
Degree of protection: IP20 acc. to EN 60529
Safety class: III acc. to IEC 536
Safety acc. to EN 50178 and EN 60950: SELV
Emitted interference: acc. to EN 61000-6-3
Noise immunity: acc. to EN 61000-6-2
UL 508, File E197259, Vol.1, Sec.2
UL 60950, File E151273, Vol.1, Sec.11
Conformity statement EN 60079-15: ATEX94/9/EC
Kat.3;Eex, nAC, IIC, T4 U
Programming sequential switch-on delay
Sequential switch-on might be required for specific loads in order to reduce inrush surge currents. For this purpose the single outputs (6) of the diagnosis
module can be connected temporally delayed in fixed order (output 1 > 2 > 3 > 4). The time delay between the single outputs can be set at 0 ms, 24 ms or
100 ms for all outputs alike. The chosen setting is maintained even during power failures or storage for unlimited time and can be changed as often as required.
On delivery the time delay is set at 0 ms (all outputs are switched on simultaneously).
Setting of time delay: On pressing the reset button (5) permanently for approx. 8 s the diagnosis module changes into programming mode. All LEDs (3) are red
and the outputs are disconnected. If the reset button is released, the LEDs signalize the set time delay with corresponding flashing sequences. They mean:
• simultaneous flashing of all LEDs once:
0 ms
• simultaneous flashing of all LEDs twice:
24 ms
• simultaneous flashing of all LEDs three times:
100 ms
After a break of approx. 2 s the flashing sequence is repeated. By pressing the reset button shortly the next step of each setting is selected (0 ms > 24 ms >
100 ms > 0 ms).