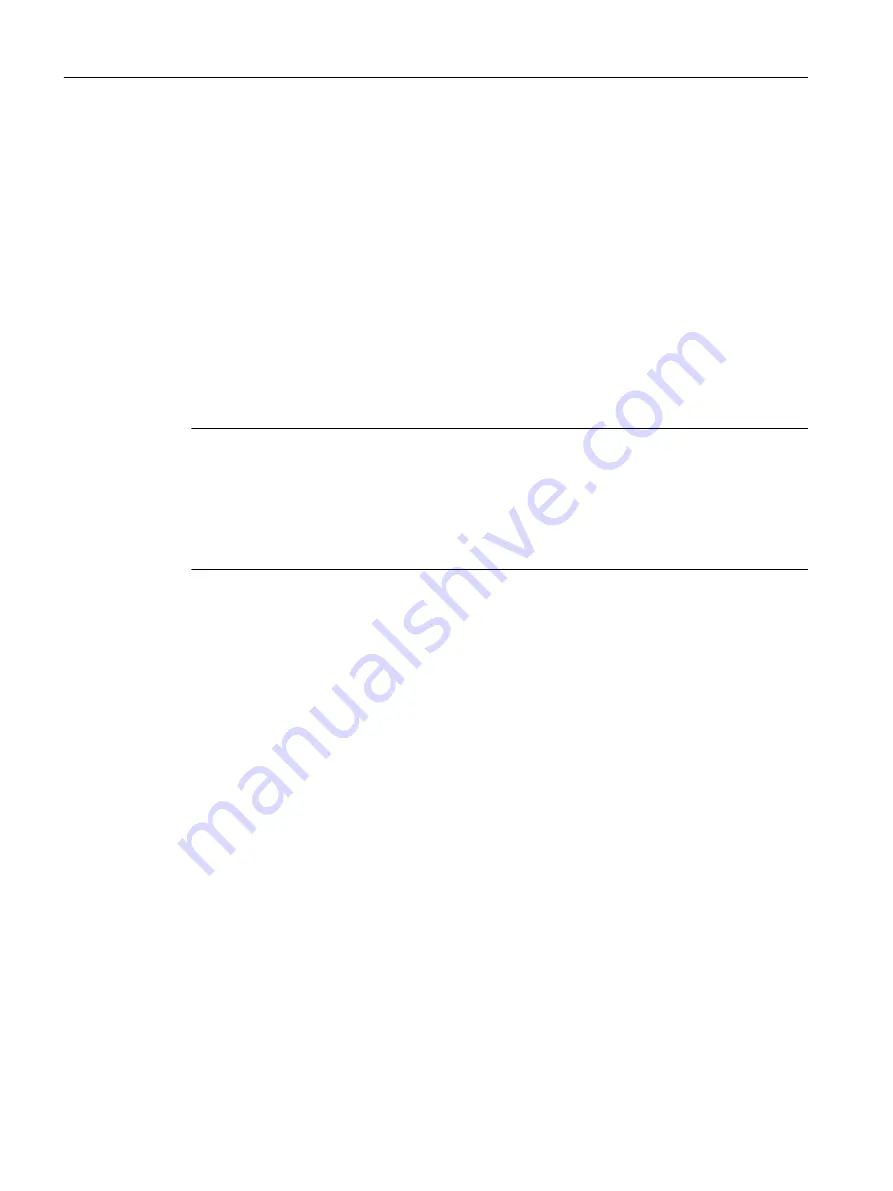
8.4
Behavior in the event of a fault
8.4.1
Power failure
After failure of the supply voltage, the device is switched off. When the supply returns, the device
is ready for operation again. For more information on power-up please refer to Chapter "Basic
versions (Page 24)", section "Power-up/self-test".
8.4.2
Internal error
The device LED shows a red light in the case of an internal fault in the device. The device must
be replaced and repair is not possible.
Note
The device LED on the 3TK2810‑1 devices can also show a continuous red light if a discrepancy
is found between the two internal processors that monitor each other. Apart from an actual
device defect, extreme EMC influences may cause this discrepancy. If this is the case, however,
the display will indicate an error code at the same time. Please notify us of this error code if the
problem occurs again. With a cold start, i.e. after the control supply voltage has been
interrupted, the 3TK2810‑1 device forgets this error again.
8.4.3
Sensor fault
8.4.3.1
Position switch protective door
When the position switches are opened, contacts P1 and P2 must be opened within t < 0.5 s. If
simultaneity is not satisfied, a diagnostics message appears on the display. After correction of
the fault, it is necessary to perform a reset (see Troubleshooting) or a restart by switching the
supply voltage off and on.
Both position switches must be closed to start output contact 23/24.
If only single-channel or two individual single-channel position switches are to be connected for
a lower category, detection of simultaneity must be disabled in the menu. Terminals T2 and P2
must be jumpered when using a single-channel position switch. If no position switches are used,
terminals T1 must be jumpered with P1, and terminals T2 with P2.
8.4.3.2
Speed sensor
If the speed sensor fails (encoder or initiators defective), the device switches to the safe state
(outputs are switched off).
A restart or reset is necessary following correction of the fault.
Diagnostics/troubleshooting
8.4 Behavior in the event of a fault
3TK2810-1 safety-related speed monitor
66
Equipment Manual, 05/2020, NEB926246402000/RS-AE/007