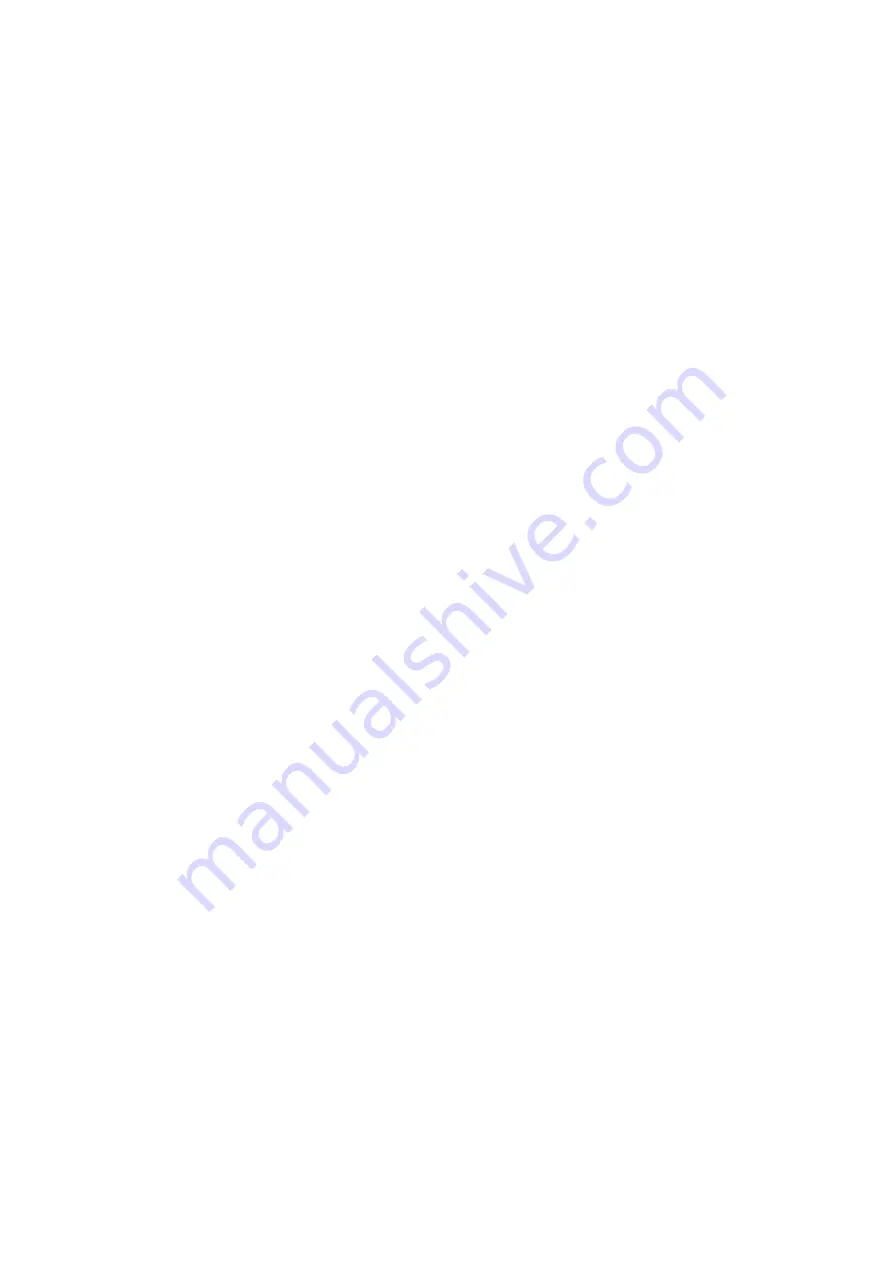
95
6 Maintenance
The filling pressure may be up to 0.30 bar over the nominal pressure curve (temperature-independent).
When filling is completed, unscrew the filling device and close maintenance flange W1 (from Dilo). Tighten the
union nut by hand (4 Nm).
6.4.5
Check Gas Pressure Gauge
The difference between the measured values on the test pressure gauge class 0.6 and the operating pressure
class 1.0 must not be greater than the sum of the permissible divergence between the two pressure gauges. This
means that with a test pressure gauge of class 0.6 having a range from 15.0 bar the divergence from the circuit-
breaker pressure gauge of class 1.0 must not be greater than 0.30 bar. A divergence greater than 0.30 bar must
be noted at the circuit-breaker pressure gauge (handwritten on adhesive tape).
6.4.6
Testing the Density Monitor
6.4.6.1
Check Function of Gas Density Monitor
Undo sealing cap on test connection W2 (the gas compartment and density monitor are separated by a nonreturn
valve) and check whether the density monitor contacts respond.
6.4.6.2
Check of the Operating Values of the Gas Density Monitor
)
Note
The adjustments of the density monitor for the SF
6
signals and the SF
6
general lockout cannot be
monitored by the filling device W423. For this the filling device W424 is required instead.
For testing the density monitor B4, a connection W2 is provided in the rear wall of the operating mechanism unit
18. (3/4" thread, Fig. 66). The hose of SF
6
filling unit W424 can be connected here without any SF
6
having to be
extracted from the circuit-breaker.