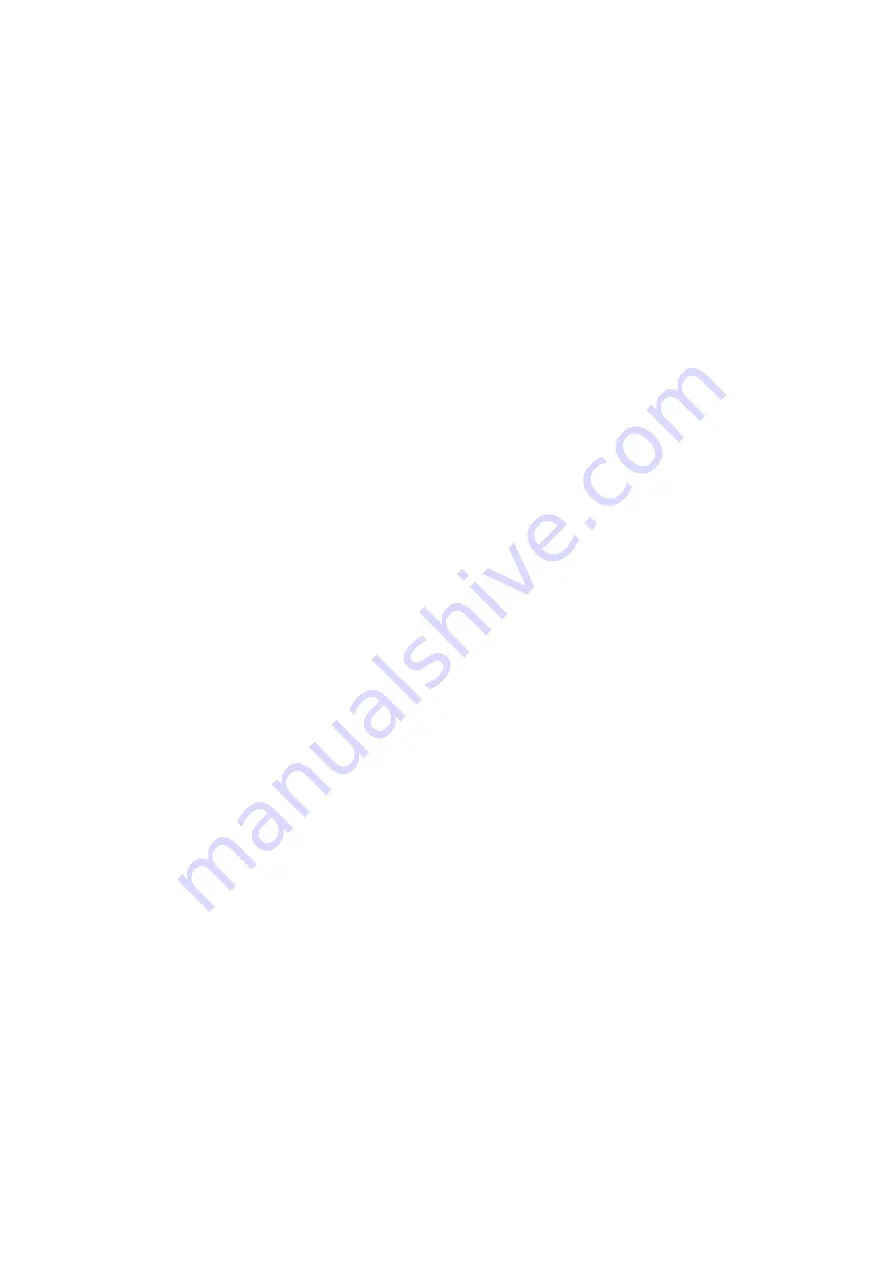
8
Siemens AG
ENGLISH
If the bearing temperature exceeds +85 °C for a prolonged period of
time, the bearing replacement intervals must be halved for each
additional 15 °C.
Renewal of the D-end and ND-end bearings is recommended
after the specified number of operating hours, and at the
latest after 5 years.
We also recommend replacing a self-fitted encoder in order to avoid
the encoder breaking down.
3.3.2 Disassembly/assembly of the motor
When disassembling the motor, mark the original positions of the parts
in relation to one another (e.g. with a marker pen or a drawing pin), in
order to simplify the re-assembly procedure.
Allow the remaining cooling water to drain out of the motor.
Please refer to section 3.2. for the encoder disassembly procedure.
Undo the screws in the bearing cover and the D-end shield, then
carefully remove this shield. Pull the rotor out of the motor. Pull off the
rolling contact bearings using a suitable device (see Fig. 10.1).
NOTE:
Take care not to alter the position of the side plate when
replacing the bearings!
Do not re-use the rolling contact bearings after they have been pulled
off. Push on the new bearings, making sure that the inner ring is
flush
with the shaft shoulder! Remove all remaining sealing agents from the
D-shield and the housing. Coat the sealing surfaces with Terostat 93
or an equivalent sealing agent. Position the rotor inside the casing. Fit
the D-end shield into the motor casing without canting it. Tighten the
screws in the bearing cover. Screw the D-end shield tight. Assemble
the encoder system.
It is advisable to renew the sealing elements, e.g. the radial shaft seal
(Fig. 11), at the same time.
The screws and bolts must be tightened to the torques specified in
Fig. 7.
3.3.3 Double D-end bearings (standard version)
- Cylindrical-roller bearing (1.70) with deep-groove ball bearing (1.60
- Fig. 2)
NOTE:
It is advisable to re-order cylindrical-roller bearings from the
manufacturer, so that account can be taken of any peculiarities, such
as the bearing clearance.
Changing bearings, lubrication
The sealing grease compartments (e.g. in the end shield and bearing
cover) must be filled half full with the specified grease type (see Fig.
10.2).
Grease quantity per bearing
(see Fig. 9.2 - Deep-groove ball
bearing and cylindrical-roller bearing)
The grease must be evenly distributed around the raceway.
Heat the rolling contact bearings uniformly to approximately 80-100 °C
and push them on. Be careful not to knock them too hard (e.g. with a
hammer).
Grease type
UNIREX N3
(from ESSO); alternative greases must conform to DIN
51825/K3N.
Bearing run-in
After the bearings have been replaced, they should be run in, to
ensure that the grease is evenly distributed. The motors should initially
be run up continuously from 0 to approximately 75 % of the limit speed
n
max
within a period of 20 minutes.
3.3.4 Single D-end bearings
(Option K00, K02 or K03, see rating plate)
- Deep-groove ball bearing (1.60 - Fig. 2)
Changing bearings, lubrication, grease type and bearing run-
in:
see section 3.3.3.
Grease quantity per bearing:
see Fig. 9.2 - Deep-groove ball
bearing)
3.3.5 Arrangement of the bearings for high speeds
(Option L37 see rating plate)
Balancing
Motors with high-speed bearings are balanced with half-wedges.
Replacing bearings, lubrication
Ensure that the utmost cleanliness is maintained.
The grease reservoirs (e.g. bearing plate, bearing cover) are to be
half-filled with the types of lubricants stated (see fig. 10.2).
Do not wash the bearing out before lubricating!
Fill the bearing with the stated quantity of lubricant, ensuring that the
lubricant is evenly distributed in the track.
Quantity of lubricant per bearing
(see fig. 9.2 - High-Speed
Bearings)
Types of lubricants
LUBCON THERMOPLEX2TML (Lubricant Consult Co.)
Assembly
Heat the bearings inductively to 80°C, max. 100°C, and slide them onto
the cleaned, dust-free bearing seating.
When mounting the bearing plate, ensure that the seals are still capable
of performing their sealing function, otherwise they must be replaced
by new ones.
Running in the bearings:
see section 3.3.3