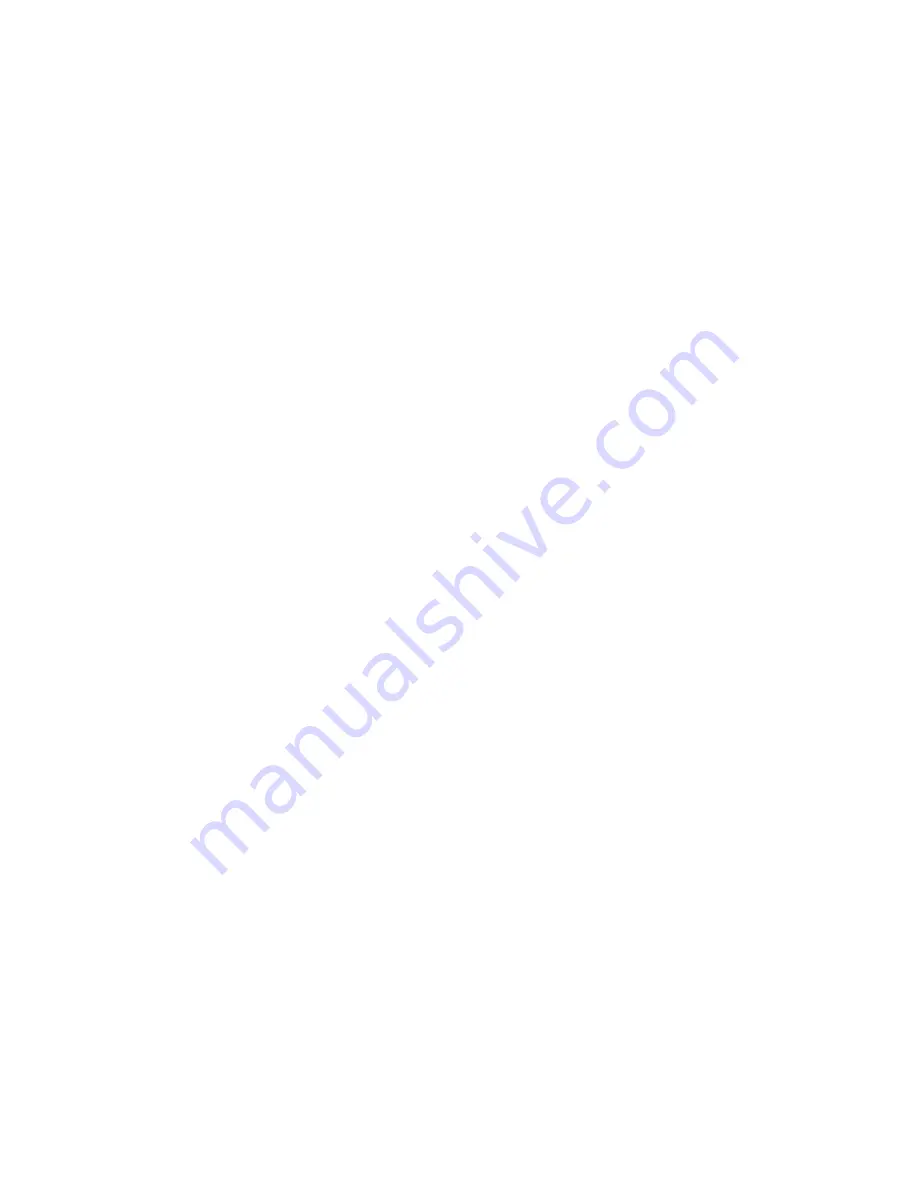
Siemens Building Techologies, Inc.
V
Table of Contents
How To Use This Manual ............................................................................................. VII
Manual Organization ................................................................................................. VII
Manual Conventions .................................................................................................. VII
Manual Symbols ........................................................................................................ VIII
Datamate Software .................................................................................................... VIII
Getting Help .............................................................................................................. VIII
Where To Send Comments ....................................................................................... VIII
Product Overview ......................................................................................................... 1
Introduction ................................................................................................................... 1
Related Equipment .................................................................................................... 1
Electronic Actuation ................................................................................................ 1
Pneumatic Actuation ............................................................................................... 1
Ordering Notes ....................................................................................................... 2
Hardware Inputs ........................................................................................................ 3
Analog ..................................................................................................................... 3
Digital ...................................................................................................................... 3
Hardware Outputs ..................................................................................................... 3
Analog ..................................................................................................................... 3
Digital ...................................................................................................................... 3
Power Wiring ............................................................................................................. 3
Communication Wiring .............................................................................................. 3
Controller LED Indicators .......................................................................................... 4
Operator Display Panel (ODP) .................................................................................. 4
Laboratory Exhaust Air Terminal ............................................................................... 5
Venturi Air Valves ...................................................................................................... 6
Electronic Actuator Assembly
...................................................................................................................................
Err
or! Bookmark not defined.
Pneumatic Actuator ................................................................................................... 8
Analog Output-Pneumatic (AO-P) Module ................................................................ 9
Differential Pressure Transmitter .............................................................................. 10
Airflow Sensor ........................................................................................................... 10
Cables ....................................................................................................................... 10
Содержание 125-5033
Страница 1: ...Two State Constant Volume Fume Hood Controller Owner s Manual 125 5033 Rev AA September 2007 ...
Страница 2: ......
Страница 4: ......