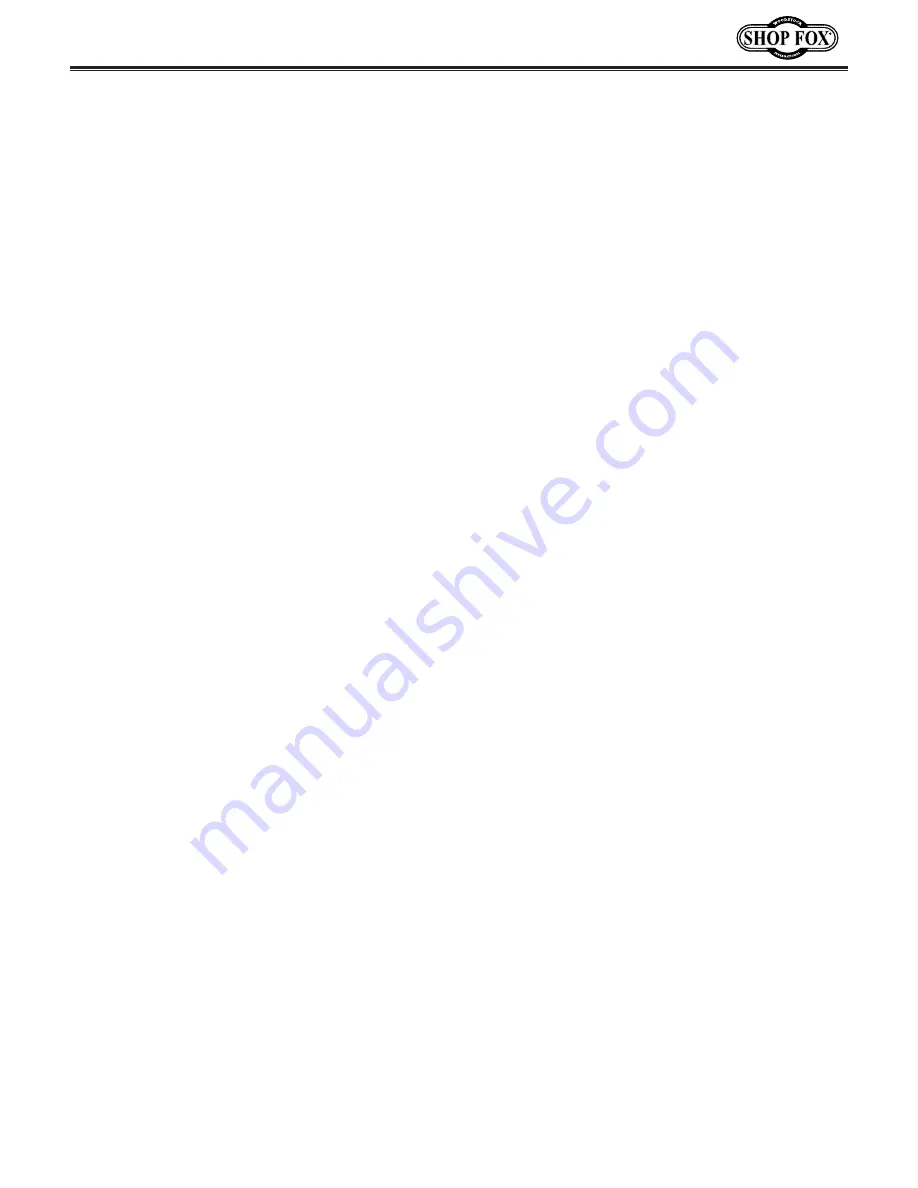
-3-
Model W1754/W1754S (Mfg. Since 7/12)
WEARING PROPER APPAREL.
Do not wear
clothing, apparel, or jewelry that can become
entangled in moving parts. Always tie back
or cover long hair. Wear non-slip footwear to
avoid accidental slips, which could cause loss
of workpiece control.
HAZARDOUS DUST.
Dust created while using
machinery may cause cancer, birth defects,
or long-term respiratory damage. Be aware of
dust hazards associated with each workpiece
material, and always wear a NIOSH-approved
respirator to reduce your risk.
HEARING PROTECTION.
Always wear hearing
protection when operating or observing
loud machinery. Extended exposure to this
noise without hearing protection can cause
permanent hearing loss.
REMOVE ADJUSTING TOOLS.
Tools left on
machinery can become dangerous projectiles
upon startup. Never leave chuck keys,
wrenches, or any other tools on machine.
Always verify removal before starting!
INTENDED USAGE.
Only use machine for
its intended purpose and never make
modifications not approved by Woodstock.
Modifying machine or using it differently
than intended may result in malfunction or
mechanical failure that can lead to serious
personal injury or death!
AWKWARD POSITIONS.
Keep proper footing and
balance at all times when operating machine.
Do not overreach! Avoid awkward hand
positions that make workpiece control difficult
or increase the risk of accidental injury.
CHILDREN & BYSTANDERS.
Keep children and
bystanders at a safe distance from the work
area. Stop using machine if they become a
distraction.
GUARDS & COVERS.
Guards and covers reduce
accidental contact with moving parts or flying
debris—make sure they are properly installed,
undamaged, and working correctly.
FORCING MACHINERY.
Do not force machine. It
will do the job safer and better at the rate for
which it was designed.
NEVER STAND ON MACHINE.
Serious injury may
occur if machine is tipped or if the cutting
tool is unintentionally contacted.
STABLE MACHINE.
Unexpected movement during
operation greatly increases risk of injury or
loss of control. Before starting, verify machine
is stable and mobile base (if used) is locked.
USE RECOMMENDED ACCESSORIES.
Consult
this owner’s manual or the manufacturer for
recommended accessories. Using improper
accessories will increase risk of serious injury.
UNATTENDED OPERATION.
To reduce the risk
of accidental injury, turn machine
OFF
and
ensure all moving parts completely stop
before walking away. Never leave machine
running while unattended.
MAINTAIN WITH CARE.
Follow all maintenance
instructions and lubrication schedules to
keep machine in good working condition. A
machine that is improperly maintained could
malfunction, leading to serious personal injury
or death.
CHECK DAMAGED PARTS.
Regularly inspect
machine for any condition that may affect
safe operation. Immediately repair or replace
damaged or mis-adjusted parts before
operating machine.
MAINTAIN POWER CORDS.
When disconnecting
cord-connected machines from power, grab
and pull the plug—NOT the cord. Pulling the
cord may damage the wires inside, resulting
in a short. Do not handle cord/plug with wet
hands. Avoid cord damage by keeping it away
from heated surfaces, high traffic areas, harsh
chemicals, and wet/damp locations.
EXPERIENCING DIFFICULTIES.
If at any time
you experience difficulties performing the
intended operation, stop using the machine!
Contact Technical Support at (360) 734-3482.
Содержание W1754H
Страница 20: ......
Страница 31: ... ...
Страница 34: ... 3 W1754 20 Planer With Mobile Base INTRODUCTION ...
Страница 70: ... 39 W1754 20 Planer With Mobile Base SERVICE W1754 Wiring Diagram ...
Страница 73: ... 42 W1754 20 Planer With Mobile Base PARTS Headstock Assembly Parts Breakdown ...
Страница 78: ... 47 W1754 20 Planer With Mobile Base PARTS Base Breakdown ...
Страница 81: ... 50 W1754 20 Planer With Mobile Base PARTS Columns Breakdown ...
Страница 85: ......
Страница 88: ......
Страница 89: ......