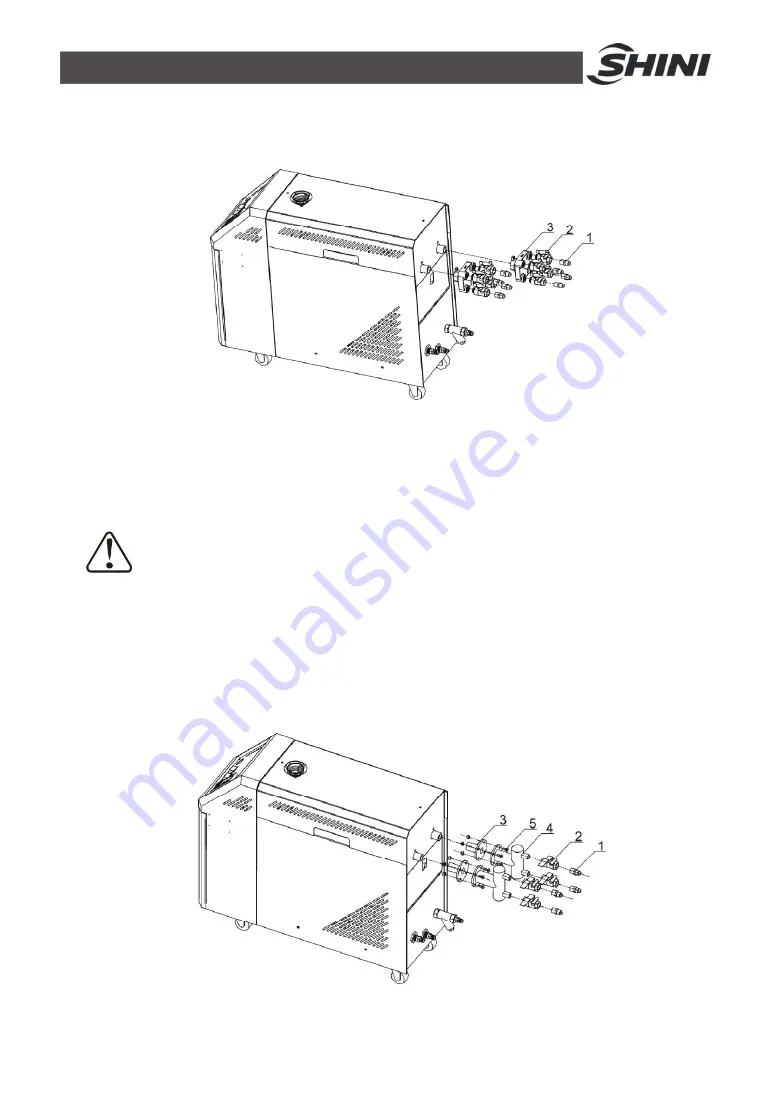
36(65)
2.5 Operation Procedures
2.5.1 Installation steps for options water manifold (dewaxing)
1) Install copper joint to the level valve.
2) Install level valve with copper joint to the dewaxing water manifold.
3) Install water manifold to the machine.
4) Install Teflon to copper joint.
Note!
For the operating temperature not higher than 200
℃
, Teflon with
temperature resistance 200
℃
is usable; for the operating temperature
from 200 to 300
℃
, must use Teflon with temperature resistance 300
℃
.
2.5.2 Installation steps for options water manifold (welding)
Содержание STM-1220-PW
Страница 1: ...STM PW Series Hi Temp Water Heater Date Dec 2014 Version Ver B English ...
Страница 2: ......
Страница 24: ...24 65 2 3 Electrical Diagram 2 3 1 Main Circuit STM PW 400V Picture 2 5 Main Circuit STM PW 400V ...
Страница 25: ...25 65 2 3 2 Control Circuit STM PW 400V Picture 2 6 Control Circuit STM PW 400V ...
Страница 26: ...26 65 2 3 3 Electrical Components Layout STM PW 400V Picture 2 7 Thermocouple and Terminal Layout STM PW 400V ...
Страница 29: ...29 65 2 3 5 Main Circuit STM PW 230V Picture 2 8 Main Circuit STM PW 230V ...
Страница 30: ...30 65 2 3 6 Control Circuit STM PW 230V Picture 2 9 Control Circuit STM PW 230V ...
Страница 31: ...31 65 2 3 7 Electrical Components Layout STM PW 230V Picture 2 10 Electrical Components Layout STM PW 230V ...
Страница 62: ...62 65 ...