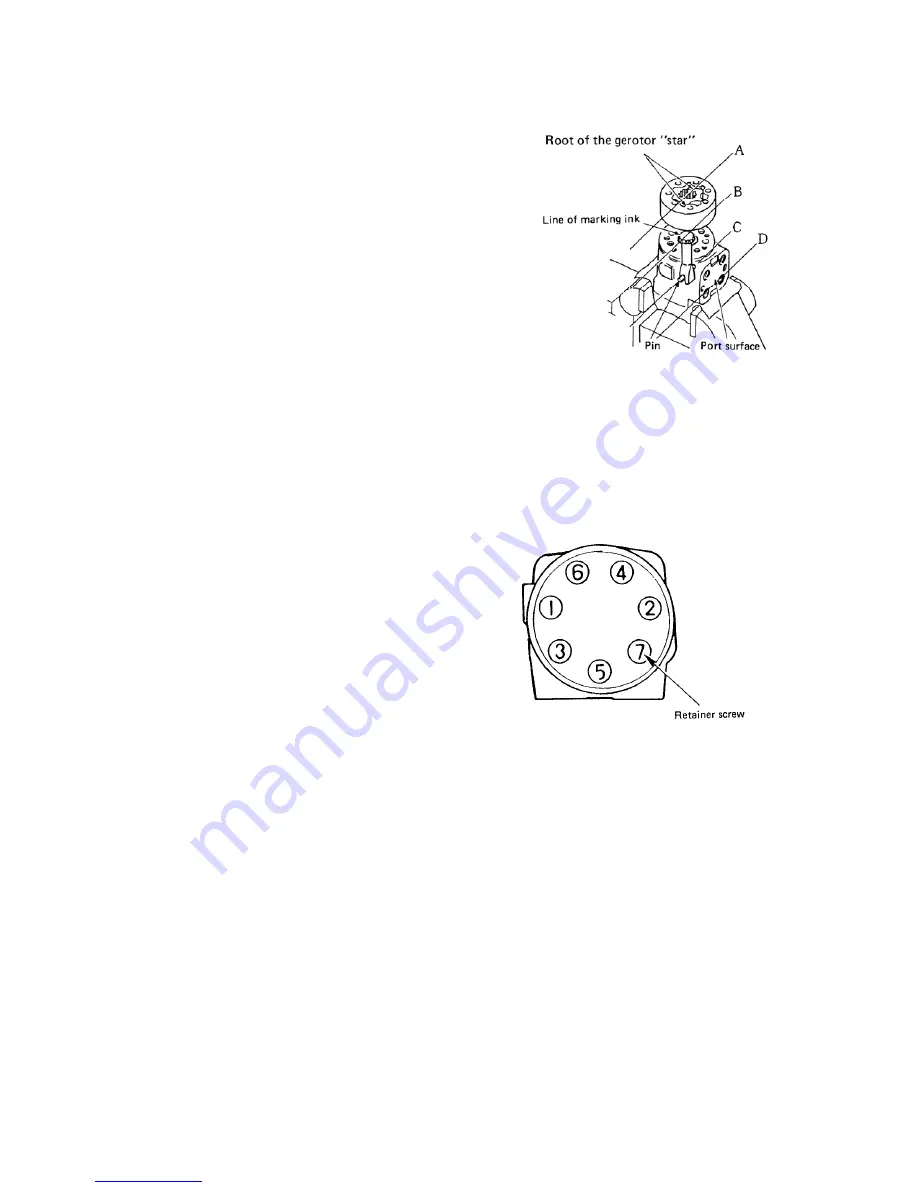
144
21. Install the O-Ring and seal (20) on the rotor (19).
NOTE: Apply a grease type lubricant to the
face of the rotor to make the O-ring
and seal adhere to the rotor surface.
22. Position the rotor in the pump ring and install the
O-ring (16) in the pump groove.
23. Position the gerotor pump assembly onto the
valve body with the seal side up. Align the drive
shaft reference line with a diametrical line
running through the center of the pump gear
valleys as shown.
NOTE: It is important that the pump drive
shaft , gear lobes and valve ports are
in the correct relationship for proper
valve timing as described above and
reference in the parallel lines A, B,C
and D.
24. Install the O-ring (16) onto the end cap (21) and
position the assembly on the valve body.
Align the bolt holes and install the retaining
bolts (22).
NOTE: Lubricate the bolt threads and
tighten to specified torque in two
steps to maintain equal pressure on
the valve body. Tighten the bolts in
the sequence as shown.
Tightening torque-----20 N·m {2kgf·m}
Recheck the valve spool to be sure it rotates
smoothly without binding.
25. Install the connector fitting (10) in the valve
pressure port and tighten to the specified torque.
Tightening torque-----69±9 N·m {7±0.9 kgf·m}
26. Install the control valve assembly on the tractor
and complete the assembly following the
removal procedures in reverse.
509X
A. Gear
Lobe
Reference
B. Drive Shaft Reference Mark
C. Drive shaft Pin Location
D. Port Face Reference
510X
Downloaded from
www.Manualslib.com
manuals search engine
Содержание CM284
Страница 1: ...FRONT MOWER CM284 CM364 WORKSHOP MANUAL Downloaded from www Manualslib com manuals search engine ...
Страница 4: ...3 Chapter 1 GENERAL Downloaded from www Manualslib com manuals search engine ...
Страница 29: ...28 13 Oil flow 045X Downloaded from www Manualslib com manuals search engine ...
Страница 84: ...83 Chapter 3 TRANSMISSION AND BRAKE Downloaded from www Manualslib com manuals search engine ...
Страница 87: ...86 4 Power Flow Range gear 304X 305X Downloaded from www Manualslib com manuals search engine ...
Страница 88: ...87 5 Power Flow PTO 306X 307X Downloaded from www Manualslib com manuals search engine ...
Страница 117: ...116 Downloaded from www Manualslib com manuals search engine ...
Страница 118: ...117 Chapter 4 HST SYSTEM Downloaded from www Manualslib com manuals search engine ...
Страница 135: ...134 Downloaded from www Manualslib com manuals search engine ...
Страница 136: ...135 Chapter 5 POWER STEERING Downloaded from www Manualslib com manuals search engine ...
Страница 150: ...149 Chapter 6 REAR AXLE ASSEMBLY Downloaded from www Manualslib com manuals search engine ...
Страница 158: ...157 Chapter 7 HYDRAULIC LIFT SYSTEM Downloaded from www Manualslib com manuals search engine ...
Страница 167: ...166 Downloaded from www Manualslib com manuals search engine ...
Страница 168: ...167 Chapter 8 IMPLEMENT DRIVE Downloaded from www Manualslib com manuals search engine ...
Страница 174: ...173 Chapter 9 MAINTENANCE STANDARDS TABLE Downloaded from www Manualslib com manuals search engine ...
Страница 177: ...176 Downloaded from www Manualslib com manuals search engine ...
Страница 178: ...177 Chapter 10 ELECTRICAL SYSTEM Downloaded from www Manualslib com manuals search engine ...
Страница 181: ...180 1000X Downloaded from www Manualslib com manuals search engine ...
Страница 195: ...194 1033X Downloaded from www Manualslib com manuals search engine ...
Страница 196: ...195 1034X Downloaded from www Manualslib com manuals search engine ...
Страница 197: ...196 1035X Downloaded from www Manualslib com manuals search engine ...
Страница 198: ...197 1036X Downloaded from www Manualslib com manuals search engine ...
Страница 199: ...198 1037X Downloaded from www Manualslib com manuals search engine ...
Страница 200: ...199 1038X Downloaded from www Manualslib com manuals search engine ...
Страница 201: ...200 1039X Downloaded from www Manualslib com manuals search engine ...
Страница 202: ...201 1040X Downloaded from www Manualslib com manuals search engine ...
Страница 203: ...202 1041X Downloaded from www Manualslib com manuals search engine ...
Страница 204: ...203 1042X Downloaded from www Manualslib com manuals search engine ...
Страница 205: ...204 1043X Downloaded from www Manualslib com manuals search engine ...
Страница 206: ...205 1044X Downloaded from www Manualslib com manuals search engine ...
Страница 207: ...206 Downloaded from www Manualslib com manuals search engine ...
Страница 208: ...207 Chapter 11 MOWER Downloaded from www Manualslib com manuals search engine ...
Страница 209: ...208 11 1 Sectional View FM60SD 1101X Downloaded from www Manualslib com manuals search engine ...