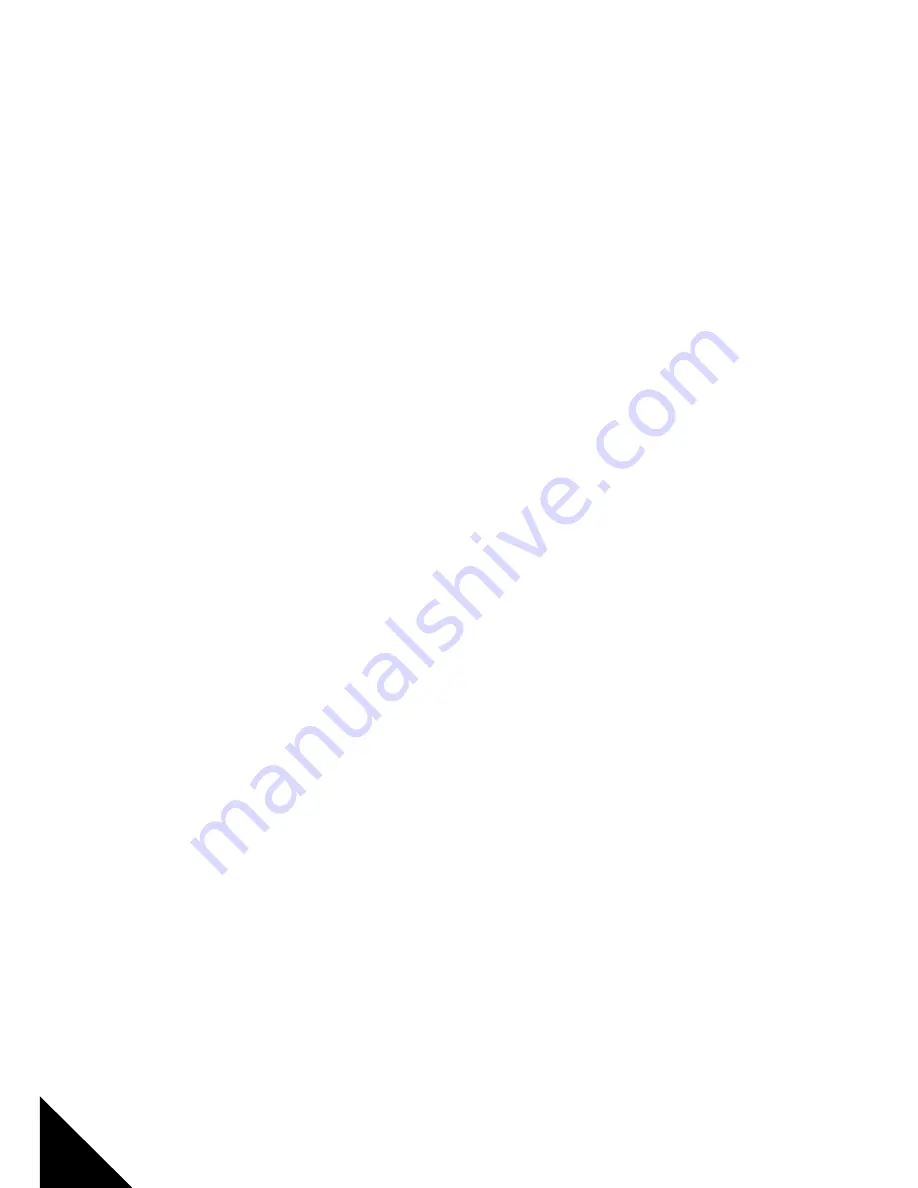
21
From a 3D model to a printing file
The real “secret” of three-dimensional printing is the transformation of three-dimensional object
into a sequence of two-dimensional slices that overlaping, reconstruct the object. Imagine a series
of slices of bread: If the stack rebuilt the loaf from which they were cut.
In the case of 3D printing every slice may consist of two-dimensional shapes not connected together
as it is their sum to create the finished object.
Thanks to this breakdown, the object can be complex as desired because the printer will draw with
the plastic one layer after another without overlap; a square or a doodle for the printer have the
same difficult.
The most important work the software makes is starting from the 3D model – usually a mesh of
triangles in space called mesh – and transforms it into a sequence of slices according to a number
of parameters (slicing). Because the process is completed correctly the mesh should be closed and
not have triangles that are oriented incorrectly confusing the “inside” and “outside”. It happens that
some model is made to art: at this point or the software that does the slicing manages to repair the
mesh or the result of errors that will prevent the correct reproduction of the object.
A good STL, a good slicing, a good print
The STL file is the starting point for the entire procedure, so from the file should be removed anything
you don’t want to print (hidden objects, etc.).
The 3D drawing must be a solid and not a solid sum interpenetrate or match. Similarly, the design
must be as clean and precise as possible: articles must have an inside and an outside well defined
so that the surfaces perfectly match each other without leaving holes. most 3D design software gives
you the possibility to carry out an analysis of borders to check for holes.
The 3D drawing must be oriented in such a way as to have a face adjacent to the XY plane of your
drawing software: in other words, the design should not “float in a vacuum”, otherwise the machine
will not print.
If you’re working on a STL downloaded from internet or given to you by a client, there are free soft-
ware for checking and correction of STL as Netfabb.
The “slices” are printed in a specific format (called G-Code); This format is nothing more than a set of
instructions for moving the instrument (cutter, laser or extruder head) along a path X, Y, and Z axes.
Each slice contains the movements on two axes, moving the press plane and motor commands that
extrudes the molten plastic to create one after another the layers that make up the object. At the end
of each layer file commands move the Z-axis by lowering the print of that plan just enough to add
the new layer.
Every 3D object can be transformed with the process of slicing in a variety of G-Code files, each differ-
ent from the others because slicing parameters generated using different: for example the slices have
Содержание Next Generation
Страница 1: ......
Страница 2: ......
Страница 3: ...SHAREBOT Next Generation USER S MANUAL...
Страница 4: ......
Страница 10: ...10...
Страница 14: ...14 1 SD Card entry...
Страница 15: ...15 1 Power cable socket 2 Power switch 3 Label with Identification Code 1 2 3...
Страница 18: ...18...
Страница 53: ...53 change the position based on which in turn will be printed so as not to find the clamp on the nozzle...
Страница 66: ...Sharebot S r l Via Montello 18 23895 Nibionno LC info sharebot it...